Introduction:
Bio-Gas: Biogas is easy and effective type of renewable energy. Biogas is a naturally occurring and renewable source of energy, resulting from the breakdown of organic matter such as cow-dung,kitchen waste etc.
Bio-Slurry:
What is Bio-Slurry: Biogas slurry is a secondary product produced by anaerobic fermentation of bio-materials, which has been widely used as a fertilizer in agricultural production.
- Biogas slurry is not only an environmentally friendly organic fertilizer, but also an efficiently utilized waste material.
- Biogas slurry has two main uses for plant production: it is used as a bio fertilizer with high levels of nitrogen (N), phosphorus (P), potassium (K), and other trace elements,
- It is as a biological pesticide due to its high levels of amino acids, growth hormones, and antibiotics, all of which promote plant growth.
- Bio-gas slurry is a rich source of nutrients and bioactive compounds having an important role in establishing diverse microbial communities, accelerating nutrient use efficiency, and promoting overall soil and plant health management.
Physio-chemical percentage of bio-slurry
Liquid bio-slurry Concentration Ref to be mentioned
Water % – 93.5
Dry matter %- 6.5
Organic Matter % – 30.6
Organic Carbon % – 17.8
Total Nitrogen % – 1.5
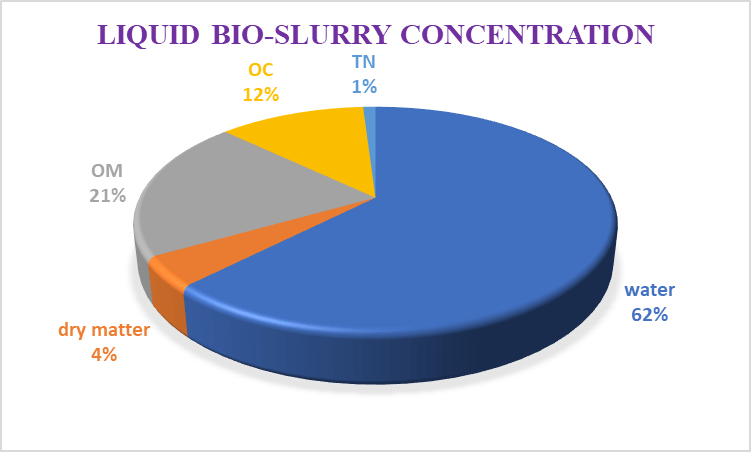
Benefits Of Bio-Slurry Manure:
1.Soil conditioner as it contains humic acid : Humic acid present in the Bio-Slurry increases the nutrient supply and hygroscopicity of the soil. In low-humus tropical soils, this humic content is very essential for stimulating plant growth.
2.Comprehensive nutrition and high-quality: The decomposition and breakdown of food and dung waste produce digested sludge as a residue which is fast-acting nutrients that enter into the soil easily, thus being readily accessible for plants. They contain all the primary nutrients for the development of soil organisms.
3.Organic fungicide: Bio-Slurry is an organic fungicide that fights against any disease-causing organisms for plants. It replaces some synthetic pesticides against pests/disease. Proper utilization of Bio-Slurry on crops or plants reduces the growth of weeds by 50%.
4.Reduces soil erosion : Bio-Slurry contributes to more rapid soil-humification, this in turn helps reduce the rate of erosion. It improves soil’s fertility, structure, crop productivity making it an excellent fertilizer.
4.Probiotic microbial-derived bio-activator : The probiotic microbial-derived bio-activator is naturally present in Bio-Slurry , which is a food source for earthworms. Earthworms are farmer’s friends, they stimulate microbial activity, promote plant growth, and reduce soil-borne diseases.
How Bio-Slurry is better than synthetic fertilizer
- Synthetic fertilizers replenish only a small part of nutrients to the soil. Poor management and application of synthetic fertilizer mean not all nutrients are absorbed by the soil. Which means less crop yield. But applying Bio-Slurry for crops has been acknowledged to improve crop yield and retain soil nutrients.
- Synthetic fertilizers are expensive and cannot be affordable for small-scale farmers.
- Overuse of synthetic fertilizers increases nitrate and nitrate contamination in vegetables, crops become susceptible to insects, microbial attacks, and weeds. Bio-Slurry reduces the growth of weeds and acts as an organic fungicide.
- High ammonia emissions due to over-fertilization using synthetic fertilizers are another growing global concern. Therefore when Bio-Slurry is combined with chemical fertilizer shows much better yields than using Bio-slurry on its own.
- Using synthetic fertilizer reduces soil’s moisture content hence more water is needed for irrigation. Bio-Slurry contains humic acid which retains soil’s moisture content.
WHY WE NEED TO FILTER SLURRY ?
1. ‘GRAM URJA FOUNDATION’ noticed that most slurry of biogas plants installed by them was wasted or not used for effective purpose
2.Transportation and collection of bio slurry is also a challenging and difficult part for maintaining biogas.
3.It is easy to use if we extract solid cake or manure from bio- slurry
4.To dewater or to extract solid cake from slurry commercially is done by 10 HP motor based ‘DEWATERING MACHINE’ is used which is very costly and cannot be easily afforded by middleclass farmers.5. Filtration process is low cost and easily can be used by small farmers.
OBJECTIVES:
- Separation of solid manure from bio slurry.
- To decrease the cost of separation process.
PROCESS CHART:
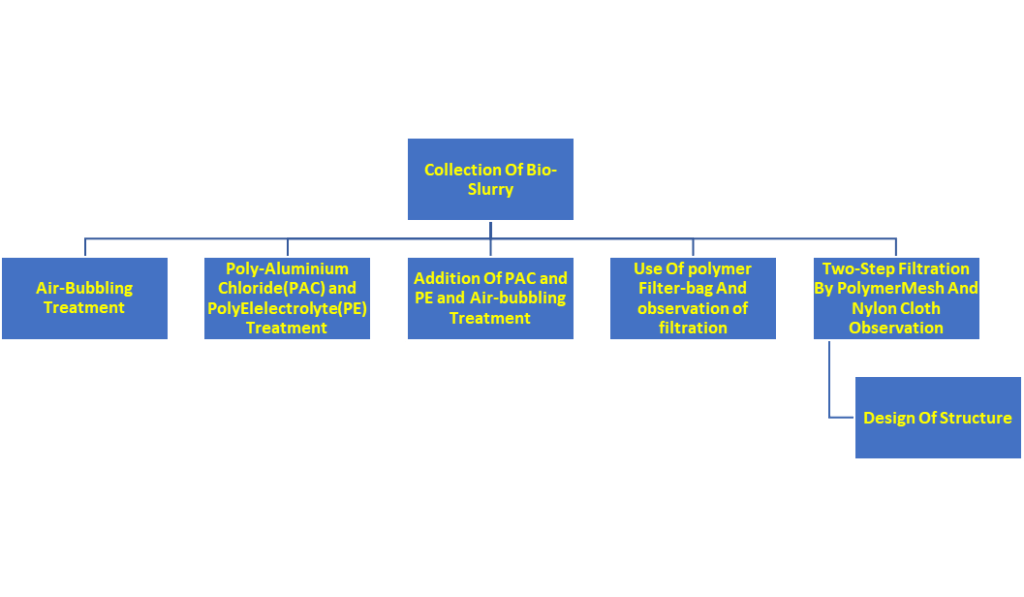
3 AUG.2022
Collection of bio-slurry from biogas plant of Ashram.
- We collected around 60 lit. of bio-slurry and put it in a plastic drum.
- In each cycle we collected around 15 lit. of slurry
4 AUG.2022
Experiment No : 1
Air bubbling in bio-slurry:
- Bio slurry contains most of anaerobic organism.To settle down the slurry we need to kill all anaerobic organisms, we did air bubbling in bioslurry.
- For bubbling air we chosen 2 air bubblers , one of 1 watt and another of 2 watt.
- Put slurry for bubbling 24 hours.
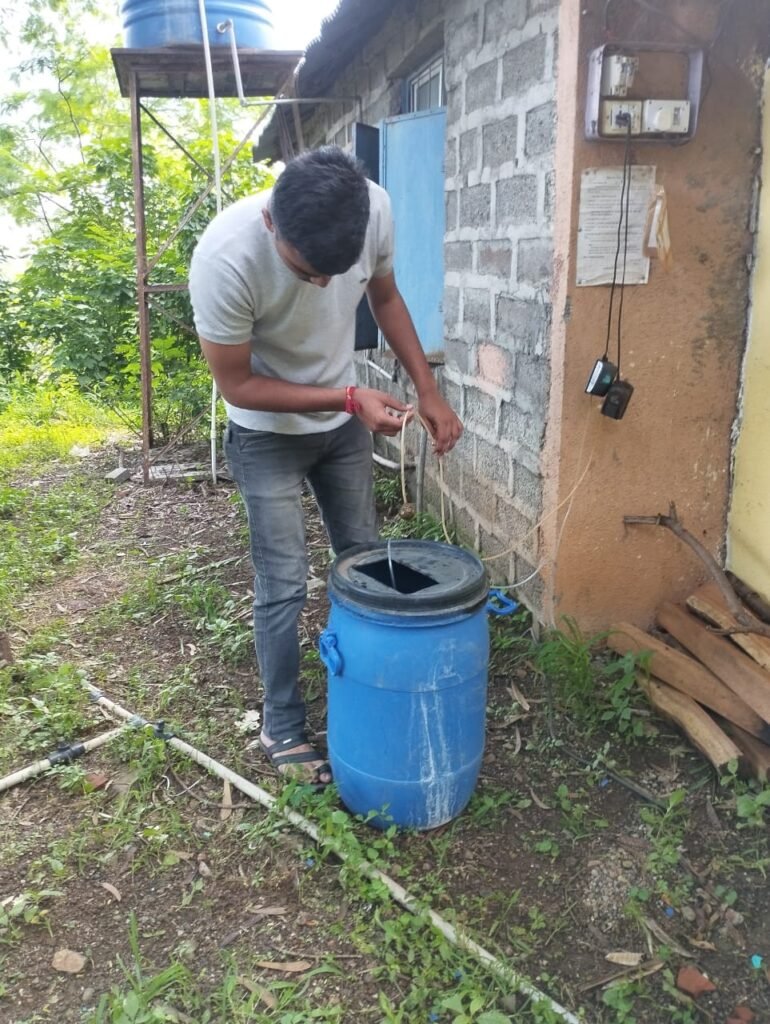
OBSERVATIONS (4-8-22):
1.We didn’t noticed any change, no settlement of slurry.
2.Hence, We concluded that air bubbling has not any effect for sedimentation of bio-slurry
6 AUG.2022
Experiment No-2
Use of chemical mixture of POLLY ALUMINIUM CHLORIDE and POLLY ELECTROLYTE.
- Polly aluminium chloride and polly electrolytes mixtures are used to settle down solid materials in solution
- Polly electrolyte and poly aluminium chloride are used in water treatment industries and to purify manufacturing products in industries.
- Dr. DIXIT suggested me to use proportion of PAC and PE as 1 gram. to 100 lit of slurry
- 4. So, I used 0.60 gram each for 60 lit. of slurry
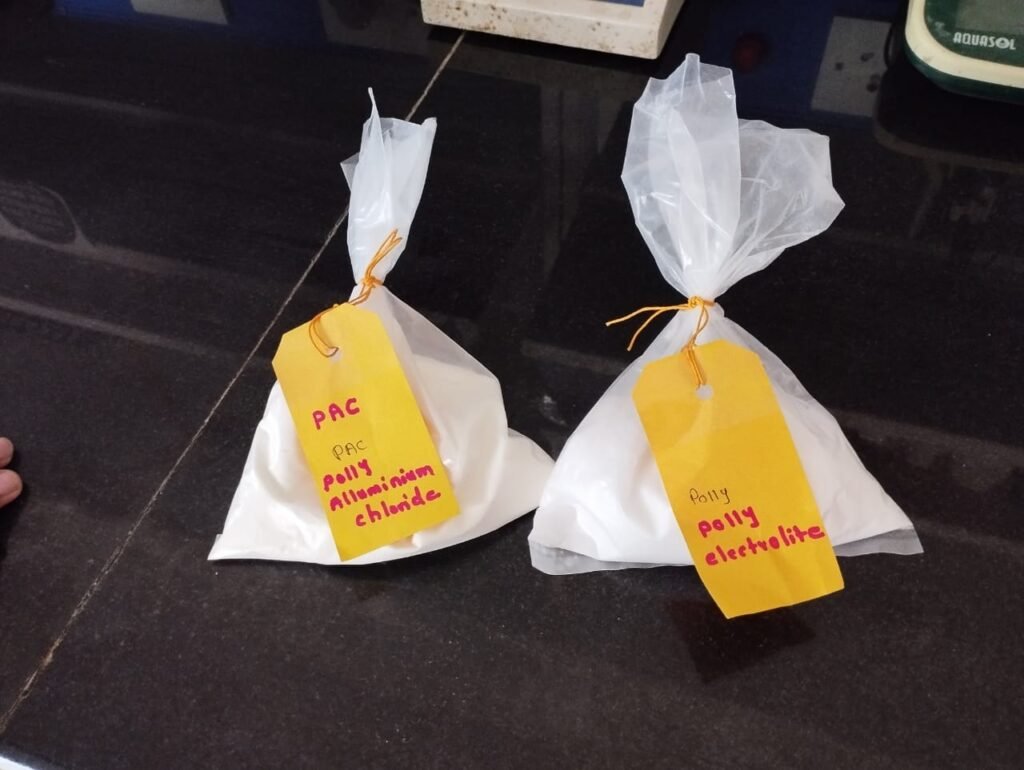
OBSERVATIONS 6-8-22
1.Poly-aluminium chloride and poly-electrolyte does not effect on sedimentation of bioslurry.
8 AUG.2022
Use of Polymer filter-bag for filtration process
- For making structure we first took measurements of filter bag.
- Filter bag has 115 cm height and 55 cm width.
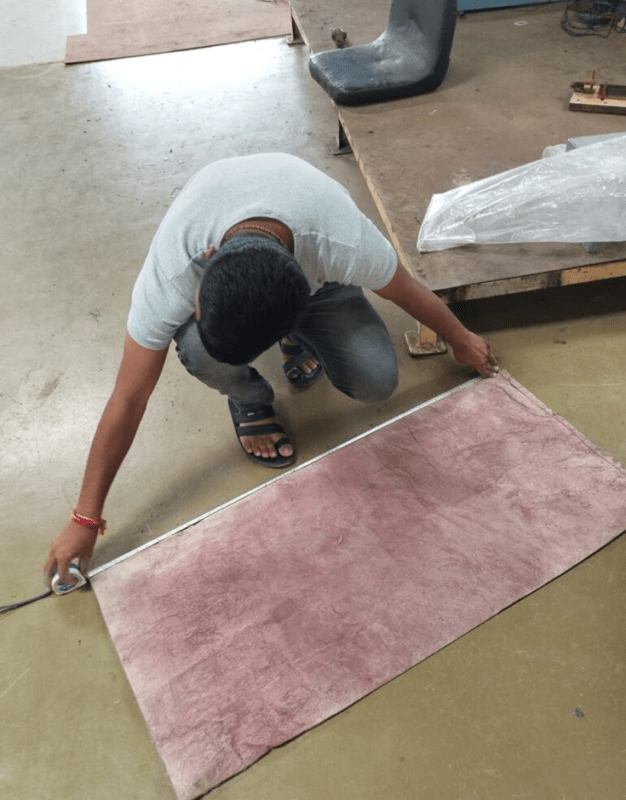
10 AUG.2022
Preparation of rough design of structure
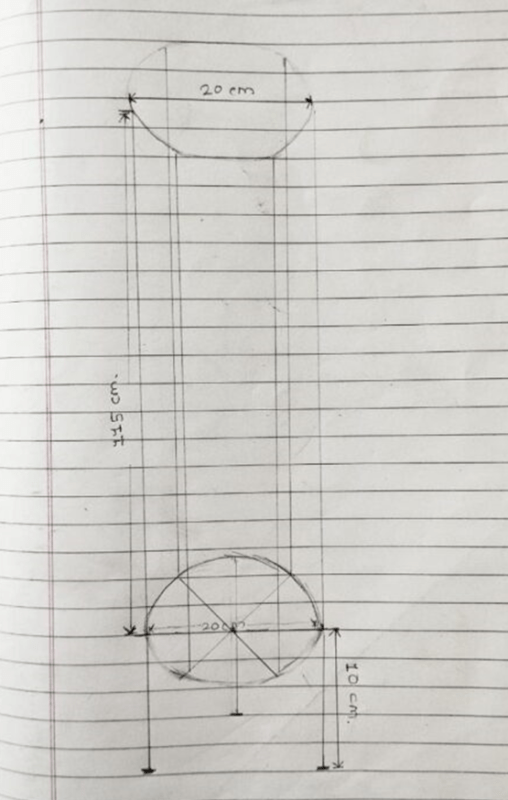
16 AUG.2022
- For making structure takes time, so we decided to put the slurry in filter bag without providing structure.
- Also collected scrap material for making structure for bag.
19 AUG. 2022
Experiment No.3
- We checked bio slurry condition of bag , and 90% slurry was successfully filtered, so our primary objectives are successfully passed.
- For further trails, research and improvement of project I continued to develop the structure for bag.
OBSERVATIONS (16 TO 19 AUG.2022):
1) It takes 72 hours to dewater 90% water from 60 lit. of slurry.
2) filtration rate decreased after 48 hours in filter-bag
3) i.e Its difficult to remove fine saturation of slurry which we get after 50% weight of slurry filtration
22 AUG. 2022
- For making structure we need to understand the strength of material .
- On the basis of design we also need to understand whether design will survive or not after applying stress.
- So, I started studying about stability, equilibrium and centre of gravity topics to develop a stable structure.
24 AUG.2022
- Calculated maximum Hoop stress for system f= 12.65 N/cm2.
- Selected a scrap material which will bear up to 12 kg weight over a foot of material.
Calculations:
Data:
Diameter Of Bag= 46 cm
Area Of Bag=17766sq.cm
Thickness of filterbag =1mm
Density of slurry = 1
calculation:
Therefore
We Know Internal Force is p= f/A
But F= m.g
= 100.9.8
= 980 N.
Now
p=980/17,766.12
p=0.055N/cm2
For Hoop Stress
f=PD/2t
=0.055*46/2*0.1
=12.65 N/cm2
Therefore
Hoop Stress = 12.65 N/cm2
Conclusion: Selected material can bear load of bag easily

29 AUG.2022
Updated Design for structure
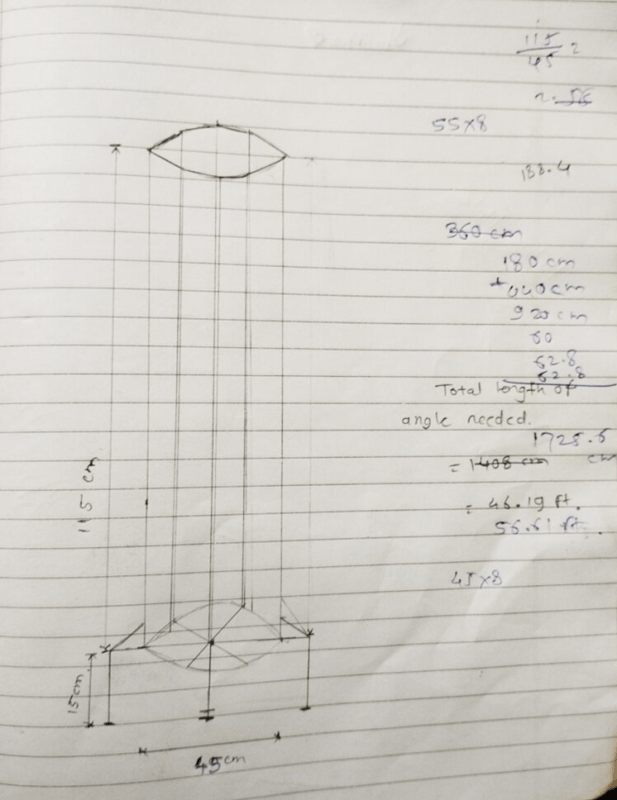
30 AUG.2022
CHOOSING OF SCRAP MATERIAL FOR STRUCURE.
- We chosen scrap material to make a good structure.
- Scrap material is easily available so we collected a quality scrap material.
2 SEP. 2022.
Fabrication Work
- I did welding of selected material , it took 2 days to learn basics of welding.
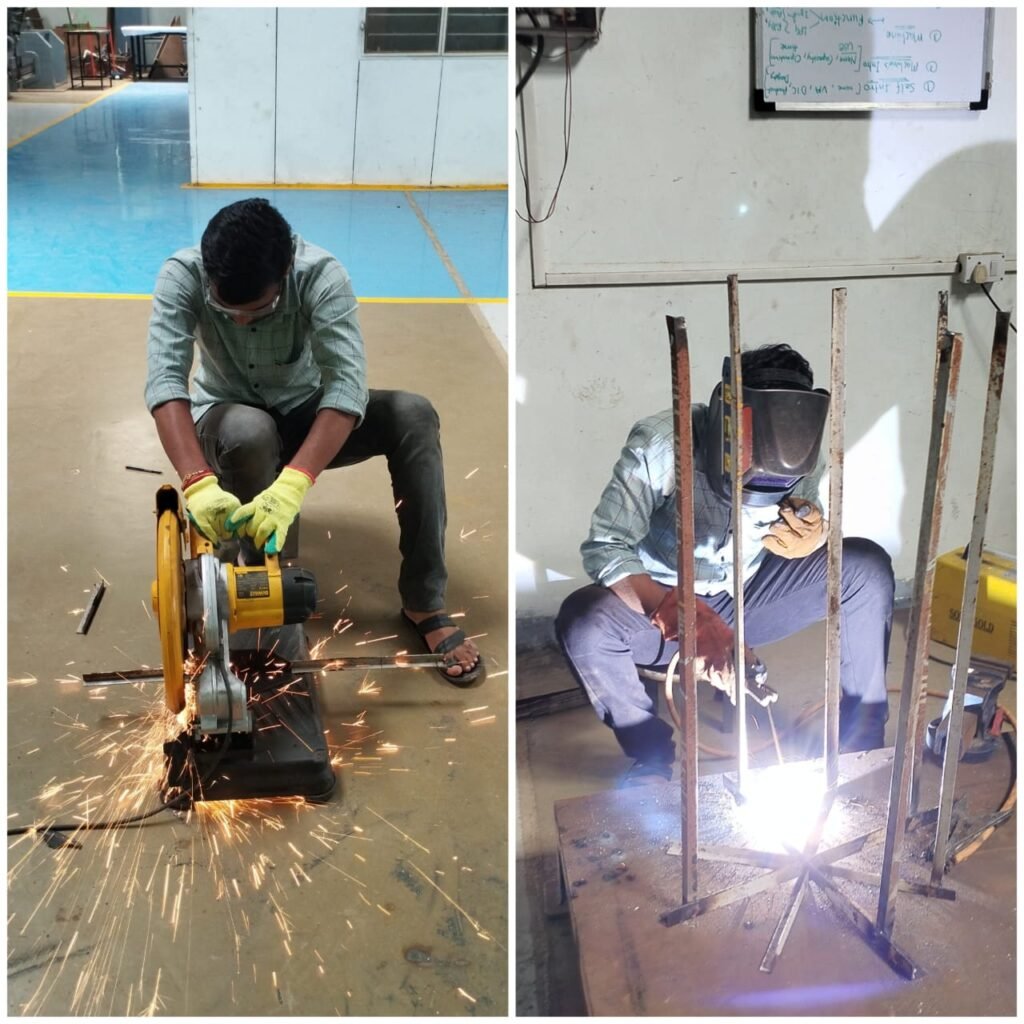
6 SEP. 2022.
Experiment No.4
- I put the slurry in filter bag in structure.
- 20 kg and 23 lit. slurry is taken in filter bag and structure.
7 SEP.2022
1.After 36 hours the slurry is 90% filtered
OBSERVATIONS (7-10 SEP.2022)
Time(hrs.) | Decreased Lit. In Slurry | Remained Lit. Of Slurry |
0 | 0 | 27.3 |
6 | 13 | 14.3 |
22 | 19.5 | 6.5 |
30 | 20.5 | 5.5 |
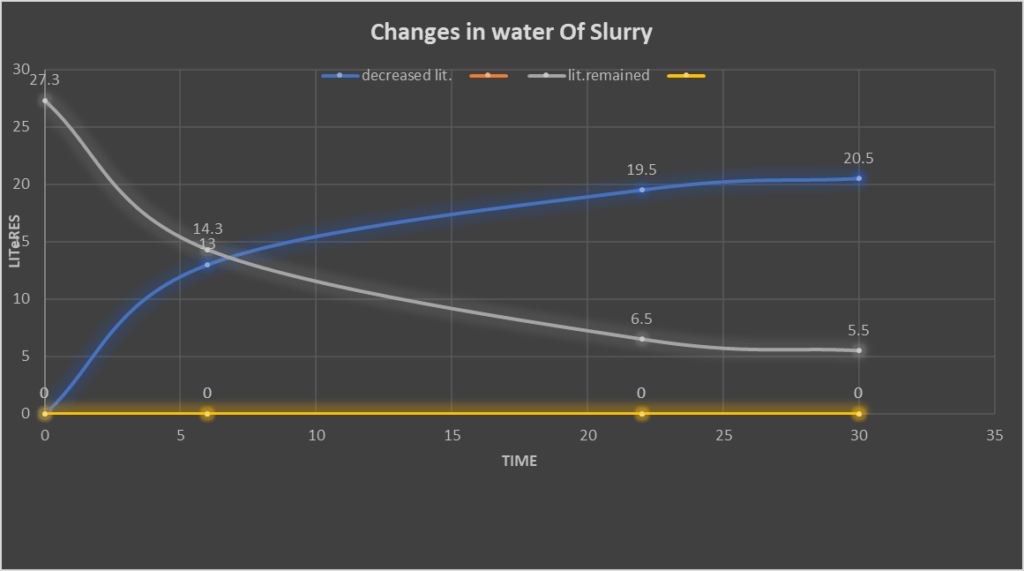
OBSERVATIONS: (14 SEP.2022)
- We noticed that first 50% (13 Lit.) slurry is filtered very fast in 6 hours of time.
- The remaining 50% slurry requires more time ( 3 time ) for filtration.
- We want to easier this process to filter remaining 50% of slurry easily and in less time.
16 SEP.2022
- We began to search the various mesh size filter cloths for bio slurry filtration.
- I searched information about filter cloths , I got some types of filter cloths, such as
- Polypropylene filter cloth
- Nylon filter cloth
- Polyester filter cloth.
21 SEP.2022
- We wanted to arrange proper filtration process step by step so that we can separate cake easily in less time
- We found that using different size mesh by two or three steps can help to filtration easily and can reduce filtration time
- Contacted and discussed with Sangeeta Garments, Thane about selection of filter cloth and mesh size
- We concluded that to use 30 micron mesh is may be suitable for slurry
8 OCT. 2022.
Visit and information collection:
- We visited BAIF( Bhartiya Agro Industries Foundations), Wagholi campus., to see the bio slurry filtration system.
- I found that they have used 1.5mm of rubber mesh. for just 1 part of filtration system.
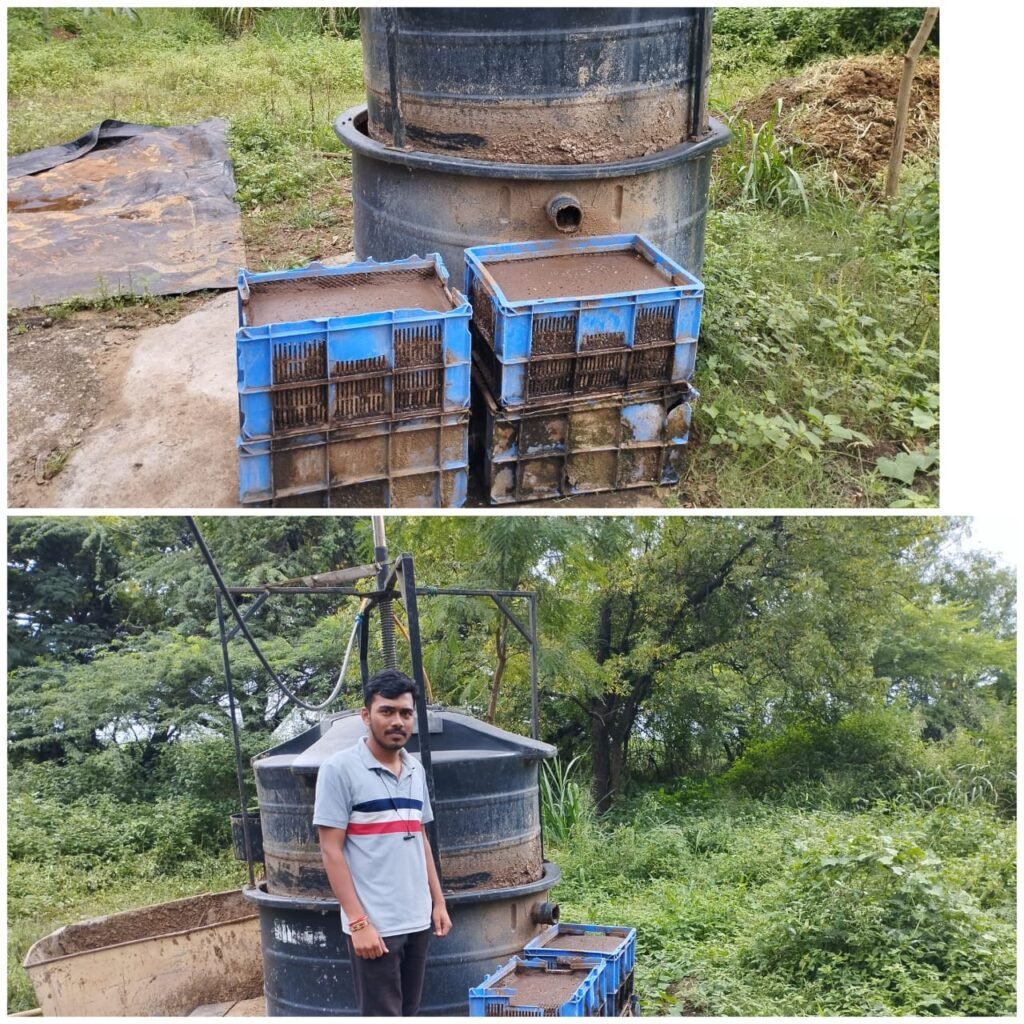
13 OCT.2022
Experiment No:5
- I took 500ml slurry of having weight 540gm.
- I have taken a mini test of filtration by using 5mm square mesh at first position and below that nylon cloth at second position.
- We found that the water at the end of filtration is so clear and easy to give plants by venturi system.
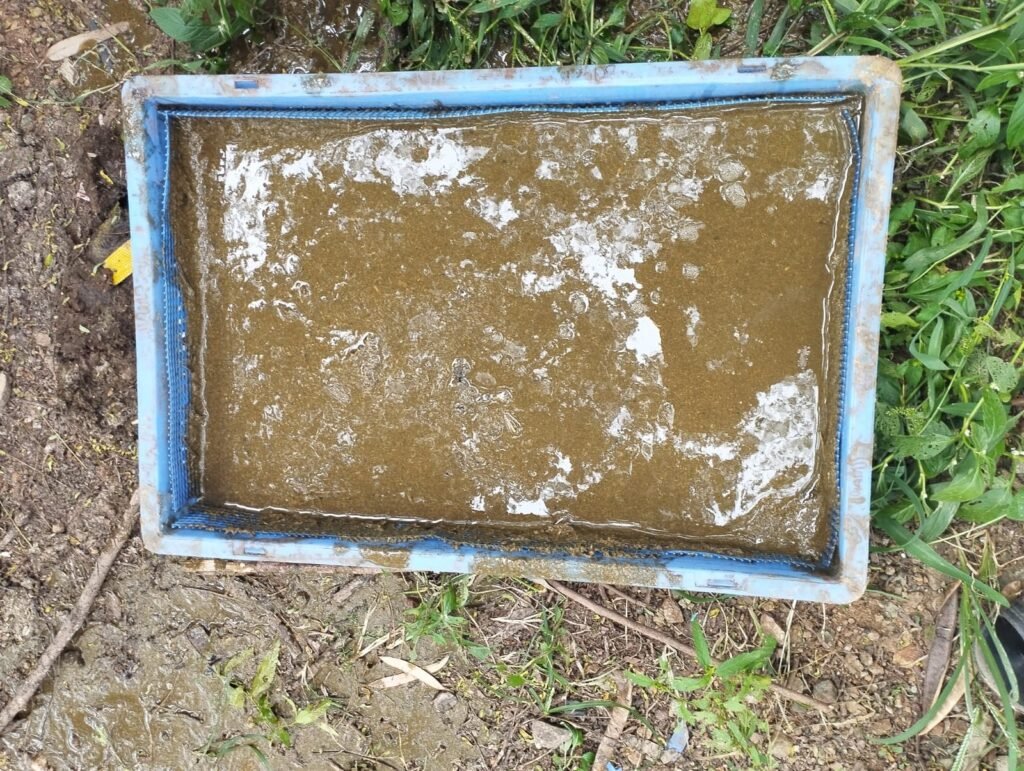
29 OCT.2022
OBSERVATIONS:
- Quantity of filtered water of slurry was weighed 290.5gm and 280ml
- Amount of solid cake or solid material 190gm
1 NOV.2022
UPDATED-DESIGN FOR STRUCTURE:
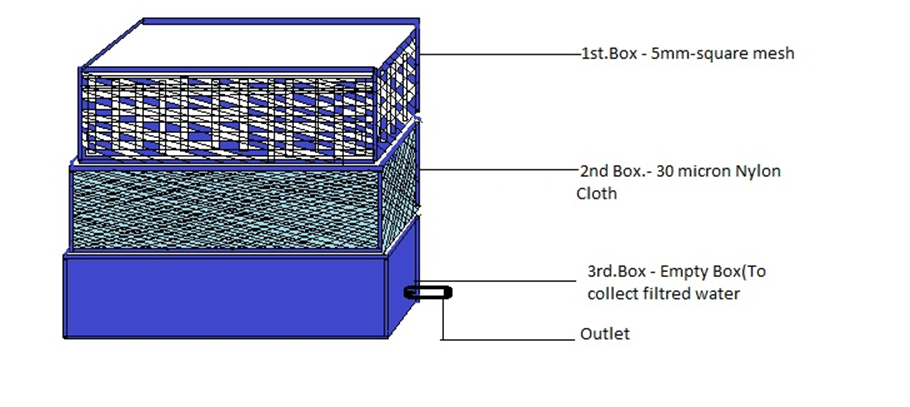
23 Nov. 2022‘
Attached 5mm square mesh to crate and made system ready to take trial.
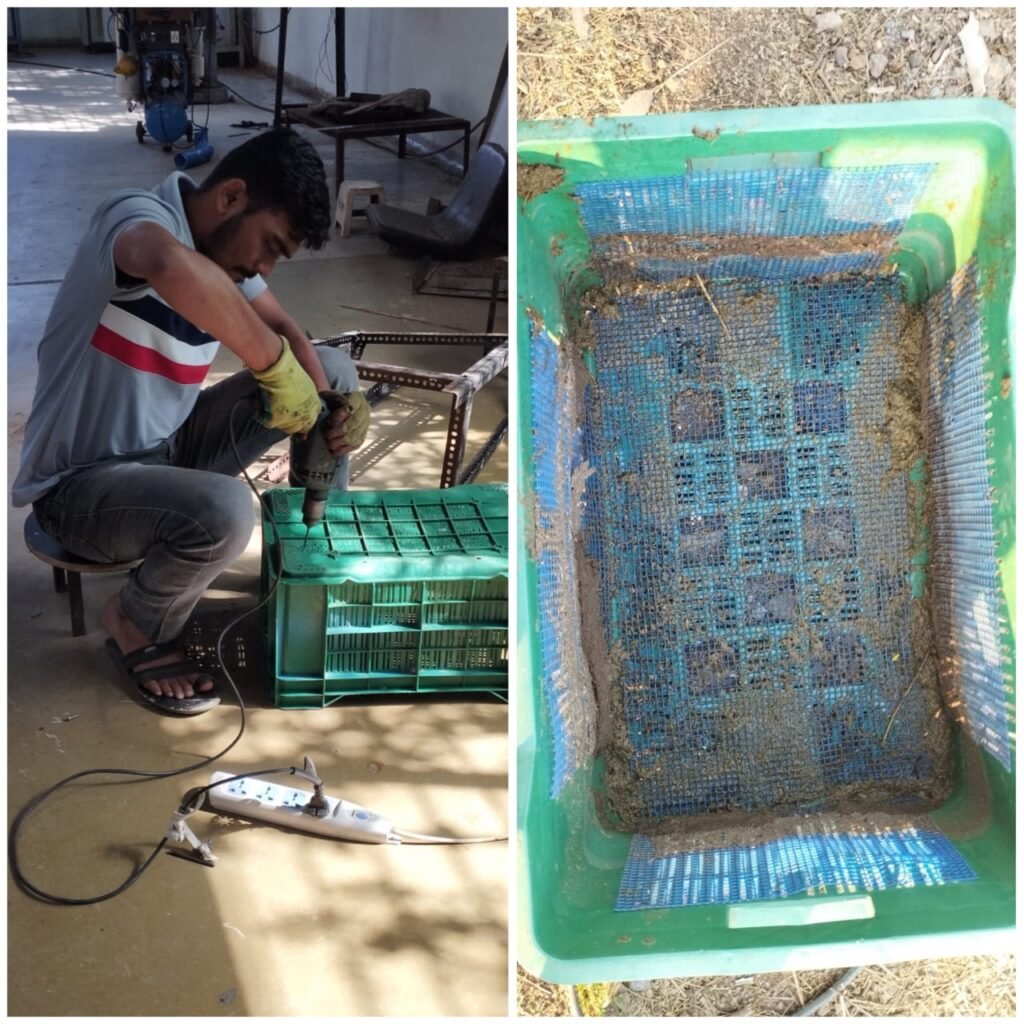
24 Nov. 2022
Experiment No: 6
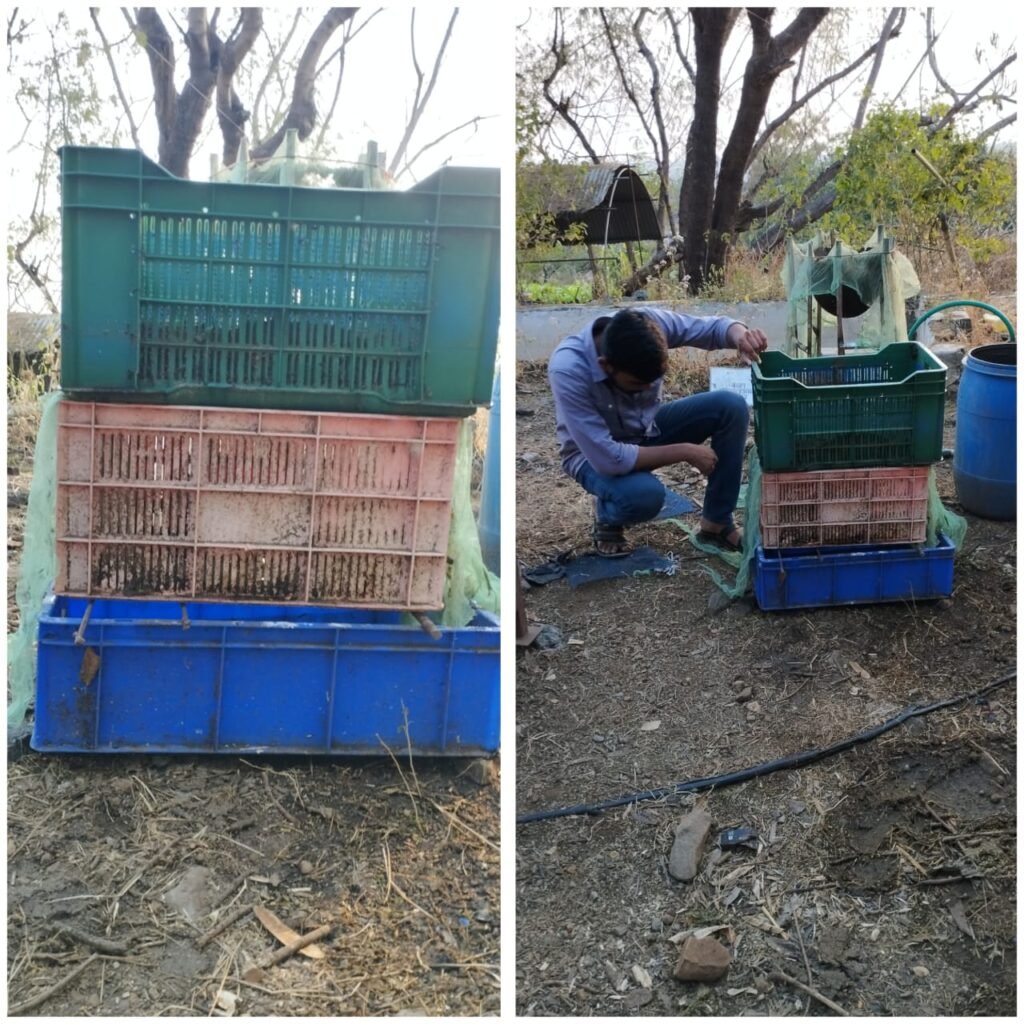
- I put 11 Kg. of slurry in updated system and leave it for 18 hours.
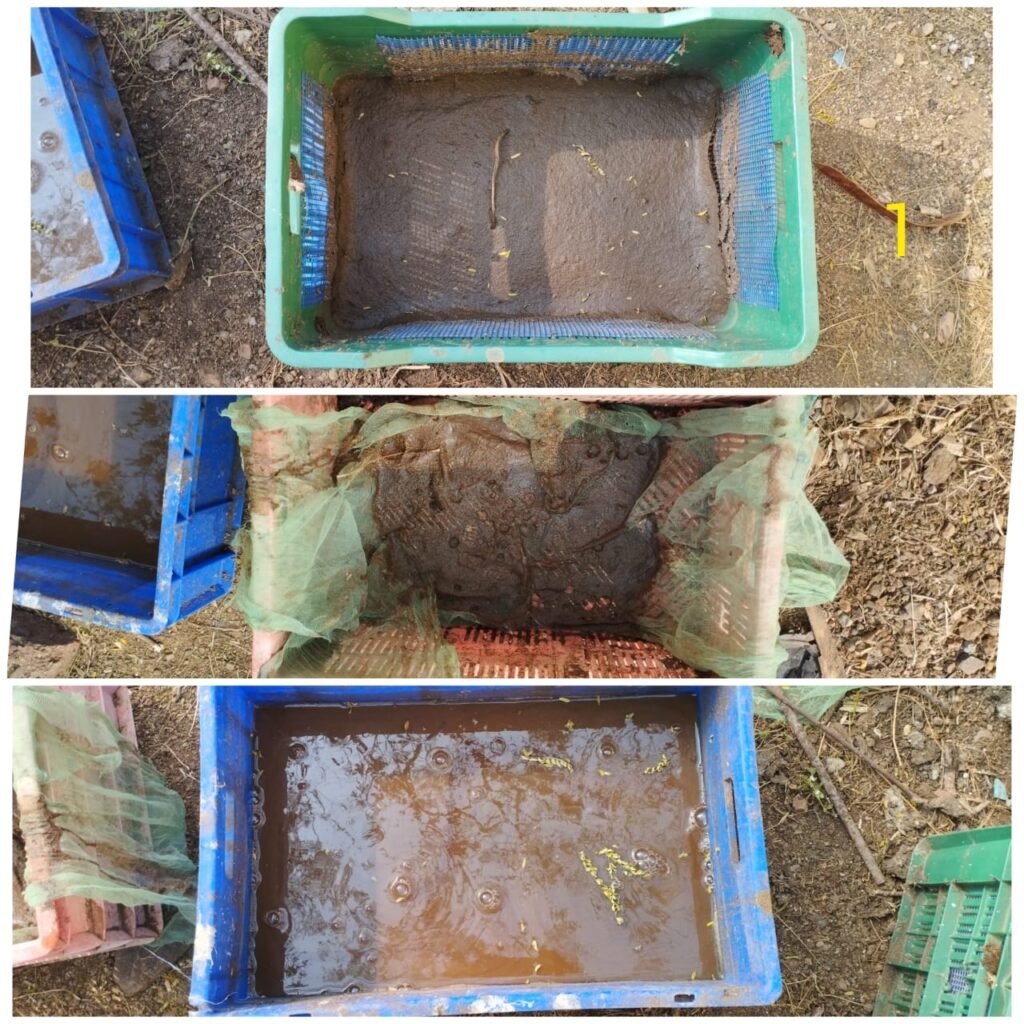
Observations
- I weighed first crate( 5mm square mesh)- 4.5 kg solid cake.
- second crate weighed(Fine Mesh )- 400 gm solid cake.
- In last crate amount of water was(Empty Box) – 5.4 kg and 5 .3 lit water.
- Solid cake is 40% water is 60%.
Final–Conclusion Note :
- Air bubbling or aeration did not showed any effect on sedimentation of bio-slurry.
- Chemical like poly aluminium chloride and poly-electrolyte which are used to settling particles in liquid ,doesn’t show any results on bio-slurry.
- Filtration rate of slurry lowers after 50% of filtration of slurry.
- Using different mesh size cycle for filtration is more effective way for filtration to obtain solid cake quickly
- Need to work on moisture reduction of obtained cake of slurry.