Functional Components of Developed pulverizer hopper:
The mechanism to be developed would be comprised of a number of working components viz., supporting stand, hopper, blades shaft, chain and sprocket bush-bearing, etc. These individual components could be explained in detail as below.
- Hopper
- Blades
- Shaft
- Bush-bearing
- Chain and Sprocket
- Supporting stand
- Motor
1. Hopper :
The main function of the hopper is to store the dry material to be placed into the pulverizer for pulverizing. The pulverizer had a large hopper for storing the material and delivers it through conveying mechanism into the pulverizer. The hopper was provided for easy placement of dry material for shredding. Another purpose is to reduce the time required to put material into the pulverizer. The selection of the shape of the hopper was done with the basic consideration that hopper should carry the desired quantity of dry material and their bulk density. The hopper was situated at top of the conveying mechanism.
Hopper of the pulverizer was made of GI sheet. The design methods were adopted as given by Sharma and Mukesh(2010) for fertiliser boxes as follow
Volume of hopper is given by,
Vb = 1.1*Ws/Ys
Where,
Vb = Volume of box
Ws = Weight of briquettes, gm
Ys= Bulk density of briquettes, gm/cm3.
Now,
For lightweight and easy operation of the mechanism, the capacity of the hopper was considered as 1 kg hopper. So, the theoretical volume of hopper required,
= 1/45.71
= 0.218 m3
= 21800 cm3
size of the hopper ,32×32×31cm then the capacity of hopper was 1.03 kg.
for 2 kg of hopper, Vb = 1.1*2/45.71
=2/45.71=0.0437 cm3 =43700 cm3
size of the hopper should be 38*38*31 cm = 44764 and the capacity of the hopper was 2.05 kg
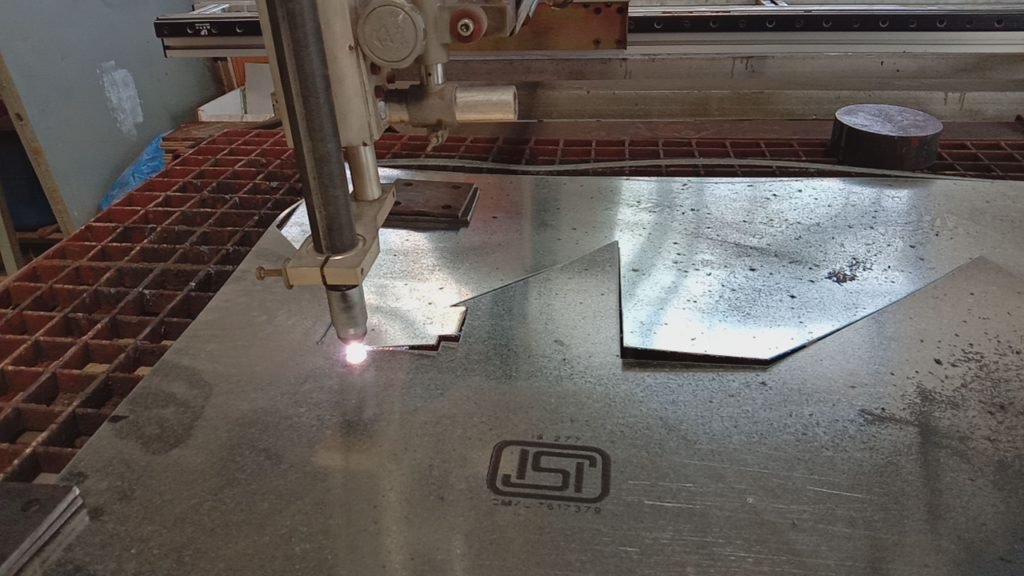

Inclined hopper sheet:
The inclined portion of assembly which was design in solid work on the basis of pulverizer inlet source.which was also cut on the plasma cutter machine.
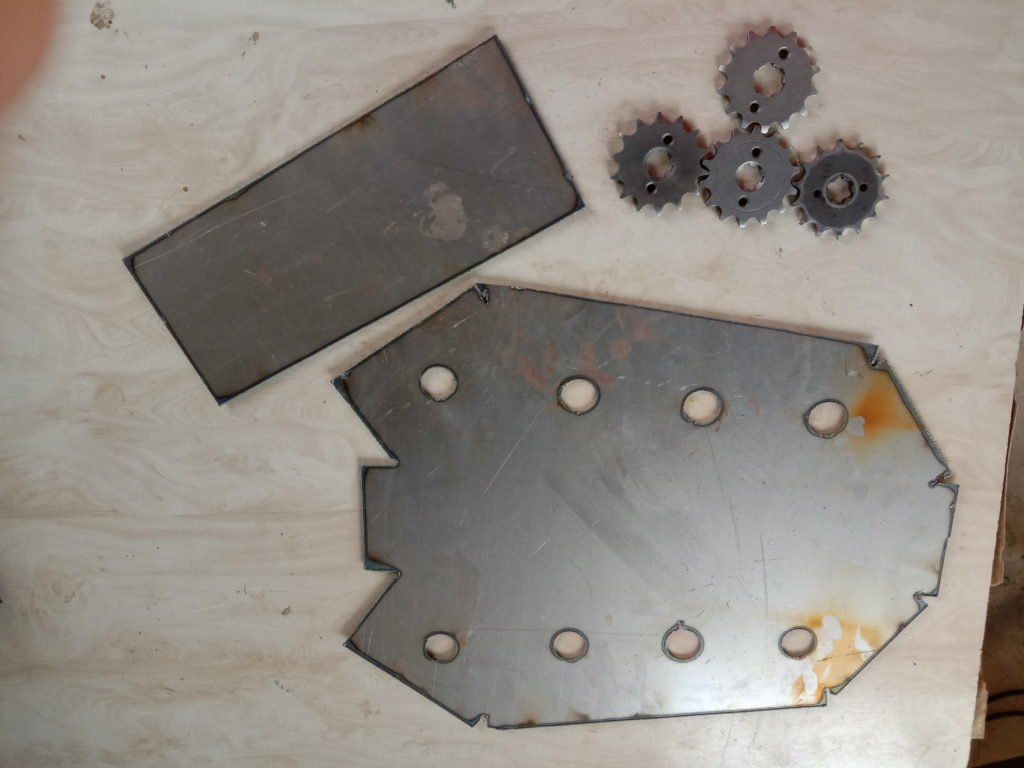
2.Blades :
The shredder blade plays a major role in the dry matter shredder machine. There are many types of shredder blades and the one which is used is a three-edged blade and tow edges blades. Space is also provided between each of the Blades for the shredded pieces to come down.
The blades which were made up of MS sheet of 0.8 mm size, the dimension of the blade was selected from the hopper inclined portion, to convey the material through mechanism the blades are made mild steel and of length of different dimensions, four types of blade all blade fixed to the shaft with the help of the fixing nut.
specification of blades,
Table no. 4.6
Sr. No. | Shaft | Two toothed blades Dia. | Three toothed blades Dia. |
1 | first shaft | 110 mm | 110mm |
2 | second shaft | 92mm | 92mm |
3 | third shaft | 82mm | 82mm |
4 | fourth shaft | 72mm | 72 mm |
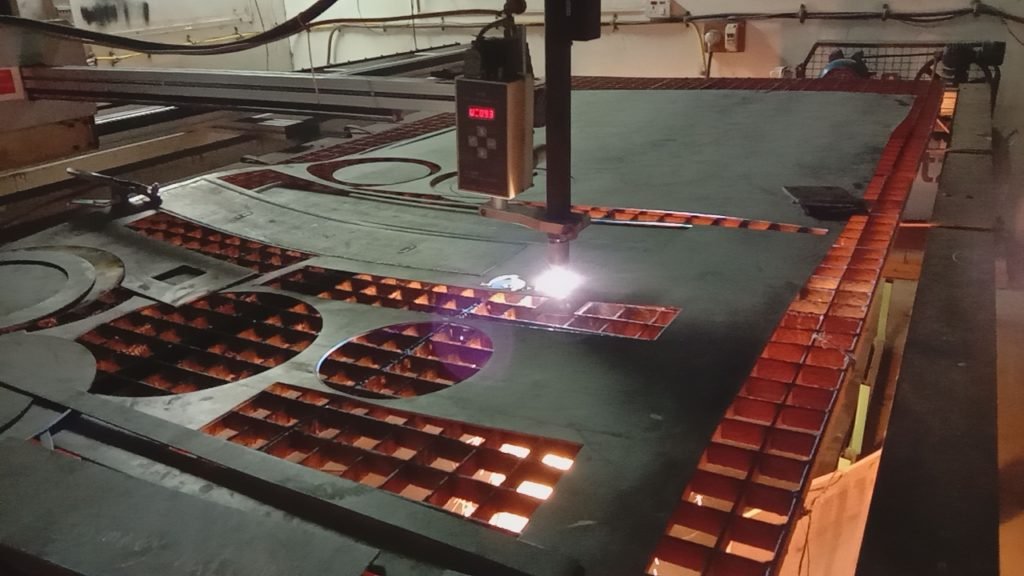
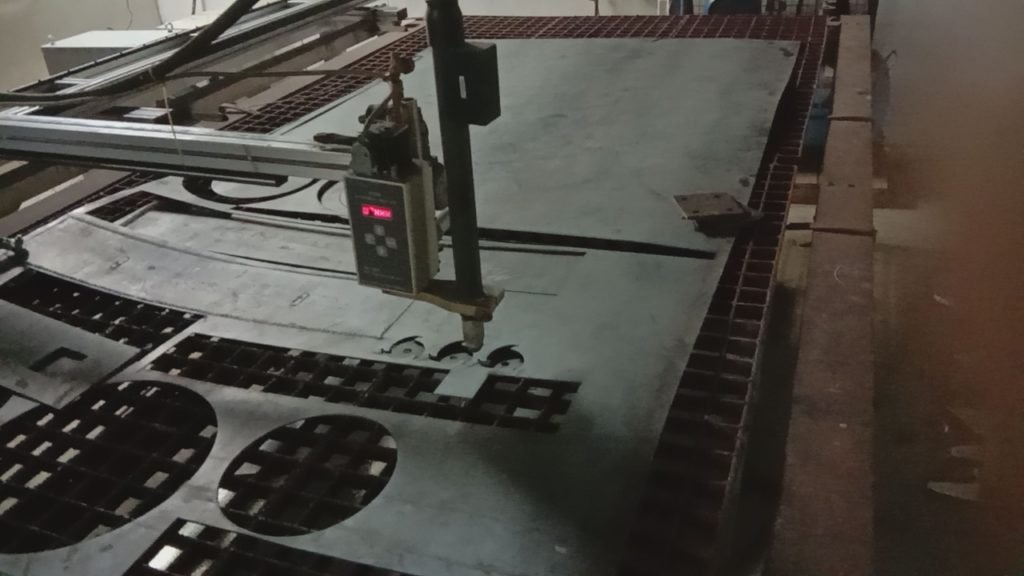
3.Shaft:
In this chapter, the general design considerations related to to the plastic shredding machine are discussed. This chapter highlights on general design considerations and procedure of main components and accessory components of the developer conveying mechanism of pulverizer. The conveying of material is done by different conveying systems. screw conveyor belts etc which was used to convey the material.
Main Shaft
A shaft is a rotating machine element which is used to transmit power from one place to another. The power is delivered to the shaft by some tangential force and the resultant torque (or twisting moment) set up within the shaft permits the power to be transferred to various machines linked up to the shaft. The shafts are classified as follows,
Transmission shaft
These shafts transmit power between the source and the machines absorbing power. The countershafts, line shafts, overhead shafts, and all factory shafts are transmission shafts. Since these shafts carry machine parts such as pulleys, gears chain and sprocket, etc,
A 12 mm outer edge diameter high strength shaft was selected for the mechanism, they were cut into the three same length and single one took extra large for large sprocket mounting.
Calculations,
width of mechanism =150mm
maximum blade size :110 mm
area of blade =2ԥr.h
=2×ԥ×55×0.8 =2.76 cm2
Volume of MS material = Area×Density
Density of MS material = 7.85 gm/cm3`
= 2.76×7.85
=21.66 gm of material in single blade.
The mechanism consist of four shaft ,and each shaft mounted with 3 and 2 blades alternatly.
Area of shaft = 2ԥ×r×h
= 2×0.6×150
=3.76 cm2
Volume of shaft material = area × density of material
= 3.76×7.85
=29.51 cm3
4.Bush and bearings :
The 6201 deep-grooved ball bearing were used for the mechanism.deep-grooved ball bearing is used to transmit loads from rotating parts to housing with minimum friction loss.this will be obtained by a high hardness. minimize the deformation of the bearing elements. Single row deep groove ball bearing are the most widely used roller bearing type in the world due to their versatility and overall performance.
The bush was made by the polypropylene material to fix the bearing into it. the polypropylene is a tough and rigid crystalline thermoplastic produced from propene or propylene monomer. It is a linear hydrocarbon resin.
The chemical formula of polypropylene is C3H6.
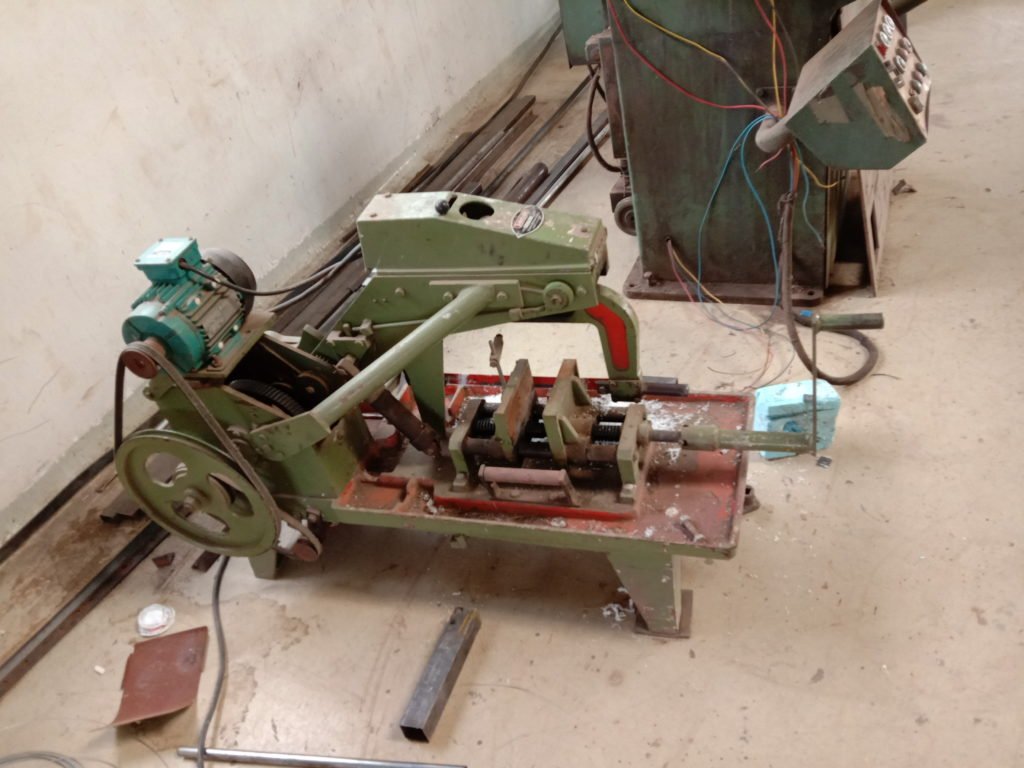
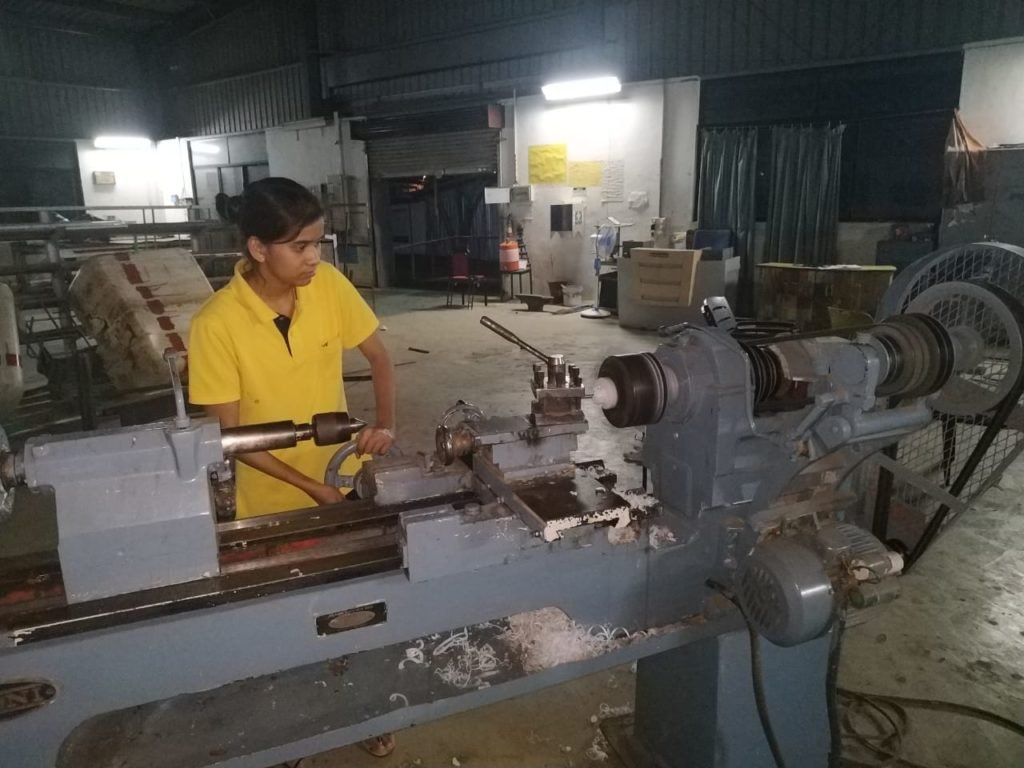
Fig. bush and bearing
5. Chain and sprocket :
Chain drives ,gear drives and belt drive system are all effective power transmission systems each offer advantages and disadvantages with respect to each other,
A chain drive is relatively easy to installed assembly tolerance are not as restrictive as those for gear drive .chain performance better than the gear under shock loading conditions.chian drive does not require tension on the sack side. chain drive required less space for a given loading and speed condition than the pulley and belt. It is less costly to build and maintain.
For the conveying mechanism, we used the 1.2 m chain, 5 small sprockets and one large sprocket to transmit the power from motor to the mechanism.
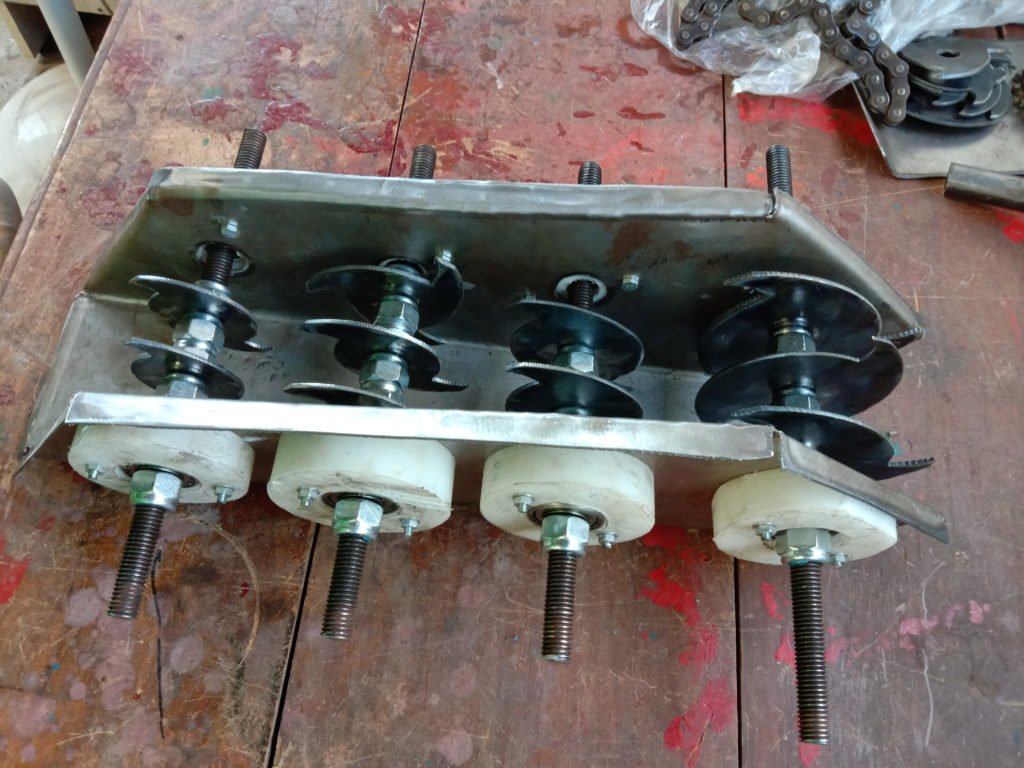
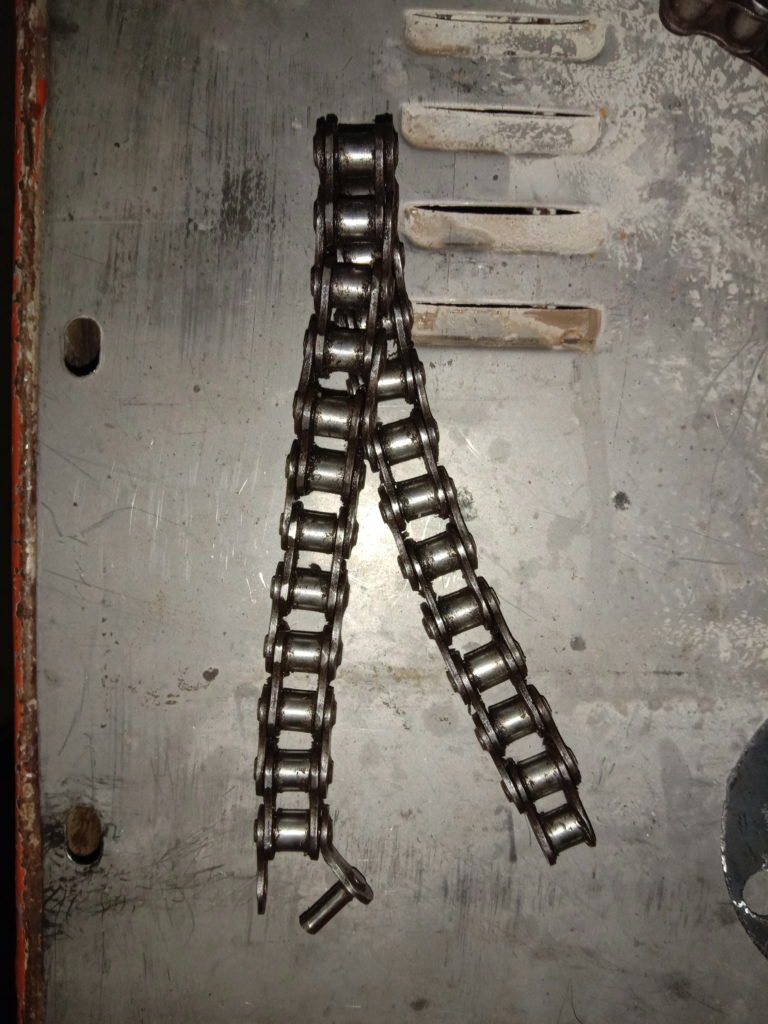
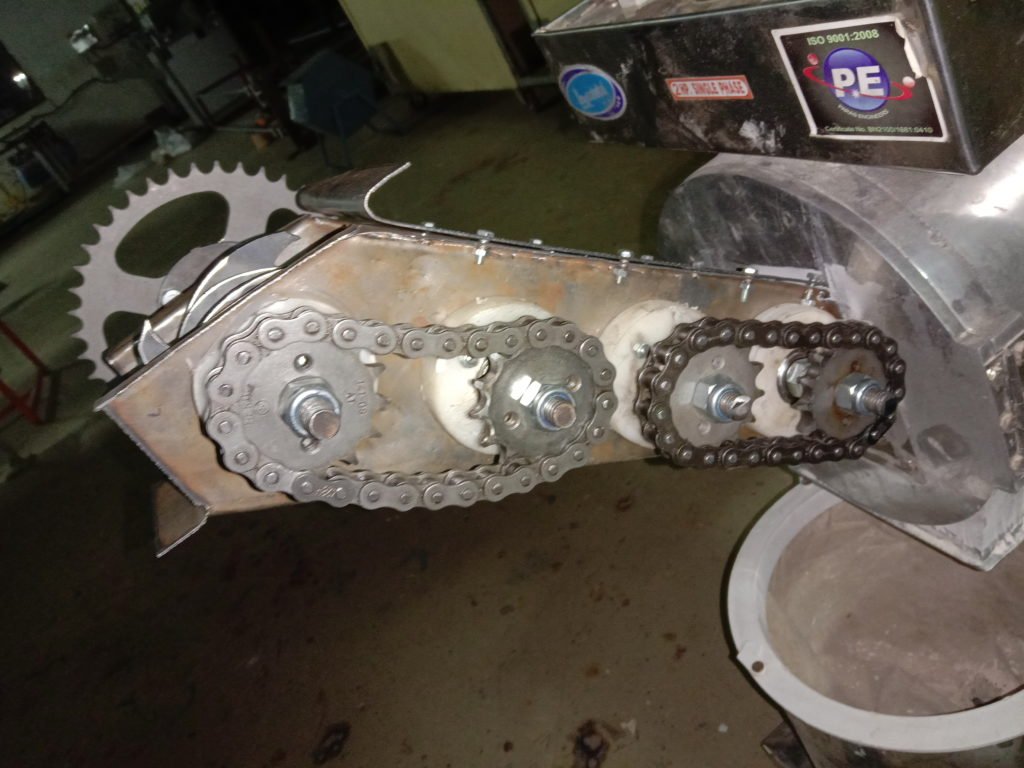
Design calculations:
Feedrate of actual pulverizer machine was 500 gm/min.
Therefore material convey per second = 8.3 gm/sec.
Now,
The volume of hopper empty space = length × width × height
= 36.5×8.7×4
= 0.12702 m3
Tray volume = 45.71 kg/cm3
=0.045714 m3
Mass = density × volume
= 0.045714×1270.2
= 58.06 gram material present in the empty space of the hopper
The material contact with single blade
= 58.06/4 = 14.5 g/sesc.
500 gram was the feedrate of pulverizer then,material pulverize per sec.
= 500/60 =8.33 g/s.
Rpm required to convey the materail of 8.3 gram was ,34.3rpm =35 rpm
Force:
Force = mass × acceleration
Force required to convey the material on single blade ,
Material =14.5 Gram
Required force =0.0145 kg
=0.0145×9.81 acceleration due to gravity.
= 0.1421 N
Torque required (T) :
= force × radius (Fr)
= 0.1421×0.0425 = 0.006040 N-M
6. supporting stand :
The which made to gave support to the mechanism because of its heavy weight, with 73cm height and 10cm width. The L-angle were used for the shand.
7. Motor :
The motor used to drive the mechanism was AC synchronous motor of the capacity of 3 kg-cm torque. Single phase motor with a voltage of 240 V and the dimension of the motor should be 86×86×68 mm.
Summary:
The modification of pulverizer hopper for brown material was modified in a different manner firstly we took a test on the assembly available in the vigyan ashram, the second trial was carried on the same mechanism with changing the clearance between the blades. the result indicates that the mare clearance increases the conveying capacity of the mechanism. another trial took on the assembly which was designed by us and the result shows more efficient than other mechanim.therefore we select that mechanism for the final product.
conclusion :
In this problem defination, we design and test different types of cutting and conveying blades. from the above design and development, it concluded that the trials took on the double edge blade and triple edge blade it is suitable for the conveying system of the dry or brown material.
A shaft is a rotating machine element which is used to transmit power from one place to another. The power is delivered to the shaft by some tangential force and the resultant torque (or twisting moment) set up within the shaft permits the power to be transferred to various machines linked up to the shaft. The shafts are classified as follows,