Problem Definition:- Input power is large as compared to output (dry product).
Input power give means electricity large as compared to dry product improve the output of heat pump dryer increases also efficiency of dryer .To improve efficiency of heat pump dryer used a perforated tray and used smart switch.
Why Use Perforated Tray ?
- For uniformly drying product.
- Hot air direct contact with product
- In this tray hot air direct contact with product and product are less time for drying as compared to solids tray less time for drying less energy consumption take place improve efficiency of heat pump dryer.
- It is light weight as compared to solids tray.
- To improve the efficiency of heat pump dryer.
Why Use Smart Switch ?
In summer season hot air is present in the outside atmosphere which contains less humidity, this air directly passes in the dryer with the help of a valve, electric energy consumption takes place and improves the efficiency of the dryer. In some time atmospheric air temperature is low and humidity is large this time output means air after drying of product is temperature large as compared to atmospheric air and humidity is less as compared to atmospheric air this time atmospheric air does not pass heat pump dryer circulates air after drying of product heat pump dryer electric energy consumption take place also input is less and efficiency improve heat pump dryer.
Ideation
Objective:-
- To make a perforated tray.
- To make a perforated tray.
1.To make a perforated tray.
Ideas:-
- Make a perforated tray used Iron flat plate for making frame of tray and Iron mesh net fix on frame drying on product. but tray heavy as compared to solids tray. not select these idea.
- Make a perforated tray frame wood and PPE Mesh fix on frame. wood are less cost material but wood not used for eating purpose food drying these idea not selected.
- Make a perforated tray frame Used a M.S Square Pipe tube make a square and middle support of the PPE Mesh provided by Iron flat plate 3 vertical and 3 horizontal fix the PPE Mesh. These tray weight are less and less prize as compared to solids tray. select idea to make perforated tray.
2.To used smart switch.
Ideas:-
1. Used valve before the evaporator and used another valve outlet provided air after drying of product heat pump dryer, these ideas are selected.
Making the Perforated Tray.
Why make Perforated tray ?
- For uniformly drying product.
- Hot air direct contact with product.
- To Improve the efficiency of dryer.
- It is light weight as compared to solids tray.
- In perforated tray hot air direct contact with product less time for drying less electric energy consumption take place and also improve efficiency of heat pump dryer.
Work done status:-
- First set 45 angles on grander for cutting of M.S.Square pipe tube for making of tray frame.
- Cut M.S.Square pipe tube 97.5 cm distance with help of a grinder machine.
- Cut M.S.Square pipe tube 97.5 cm distance species for making 11 frames.
- Finishing of cut M.S.Square pipe tube species on the grander machine.
- Cut the Iron flat plate on grander machine 94.1 cm distance species.
- The iron flat plate used to support the PPE Mesh.
- Cut the Iron flat plate 94.1 cm distance for each frame 6 species 3 vertical and 3 horizontal.
- Cut the Iron flat plate species for 11 frames.
- Finishing done the Iron flat plate species with help grander machine.
- Join the M.S.Square pipe tube species help of welding used the L-angle for accurate form square frame.
- Welding is two types used arc welding and carbon dioxide welding.
- Arc welding for joining two-part and carbon dioxide welding used for filling some part two metal.
- Join the M.S.Square pipe tube 97.5 cm distance four species with help of welding and join welding of the Iron flat plate 3 vertical and 3 horizontal for support PPE Mesh.
- After frame welding finishing done the welding for uniformly frame done by hand grander machine.
- After welding finishing polishing done by polish paper.
- Polish the frame because of removing the corrosion on metal.
- After polishing done give the Red oxide to protecting the corrosion of M.S.Square pipe and Iron flat plate.
- Red oxide mix the thinner.
- After Redoxide gives the paint white color all frame.
- Give white color frame because the white color tray sees attractive.
- After painting done set the PPE Mesh on the frame used a self-lock screw with the help of hand drill machine.
- Completed the perforated tray date 16/3/2018.

Cut M.S.Square pipe tube 97.5 cm distance with help of a grinder machine

Cut the Iron flat plate on grinder machine 94.1 cm distance species.
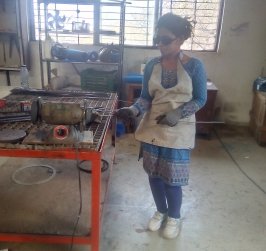
Finishing done the Iron flat plate species with help grinder machine.
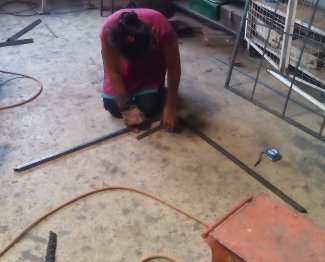
Join the M.S.Square pipe tube species help of welding used the L-angle for accurate form square frame.
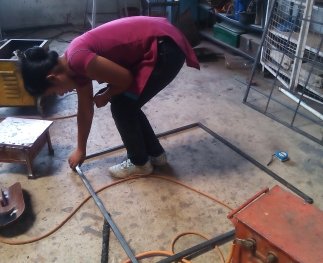
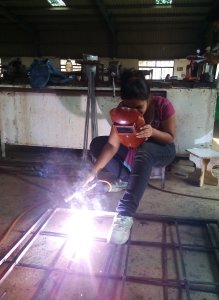
Join the M.S.Square pipe tube 97.5 cm distance four species with help of welding and join welding of the Iron flat plate 3 vertical and 3 horizontal for support PPE Mesh.
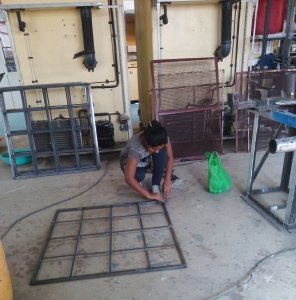
After welding finishing polishing done by polish paper.
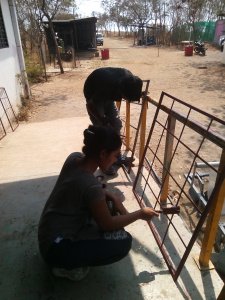
After polishing done give the Red oxide for protect the corrosion of M.S.Square pipe and Iron flat plate.
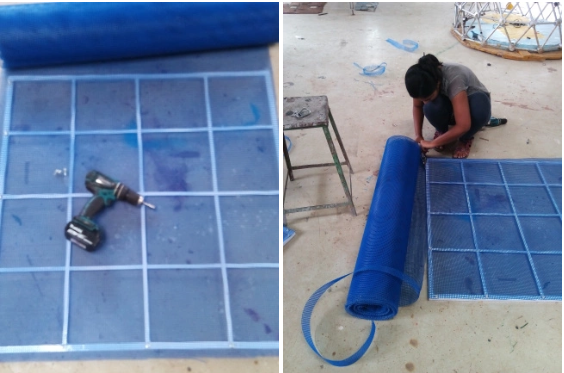
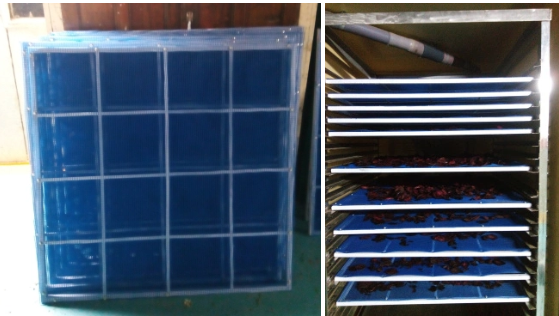
Trial
Input Table:-
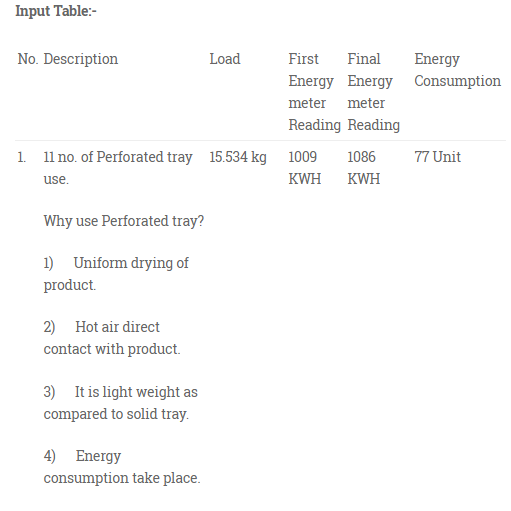
Output Table:-
No. | Water Evaporate (Kg) | Dry Product Weight (Kg) | EnergyConsumption(Rs./Kg water) | Energy Efficiency% |
1. | 14.22 | 1.314 | 36.4 | 11.57 % |
Calculation:-
Energy Consumption=77 Unit
Per Unit Rate=Rs.6.73/Unit
Water Evaporate=14.22 Kg
- Calculate Energy Consumption Rate (Rs./Kg water)=14.22/(77*6.73)
=36.4 Rs./ Unit
2.Total Energy Supplies = 77000*3600
=277200000 J
3.Total Energy Utilised = Mass of water evaporate * Latent Heat
=14220*2257.3
=32098.806 J
4.Calculate Energy Efficiency % = Output/Input
=Energy Used/Energy Supplies
=32098806/277200000
=0.115
=0.116*100
= 11.57%