Vigyan Ashram was approached by Provenant system a startup based in Pune to design an enclosure for their motion sensing light.
I was given the responsibility to take this project forward. During this project, I used a lot of hand sketching and Solid works modeling to do the design. I used the Accucraft 3D printer to print my files.
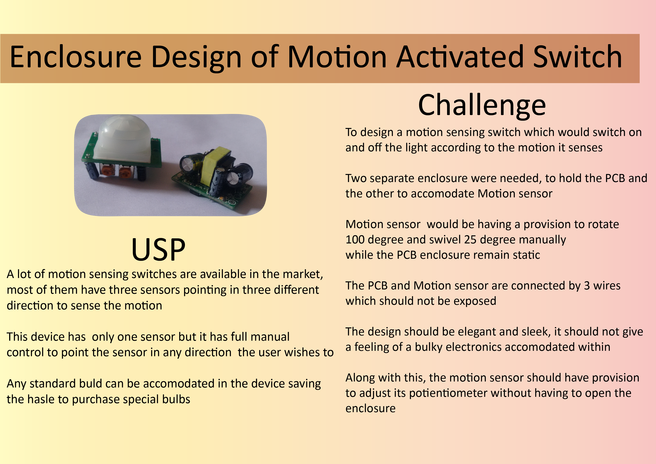
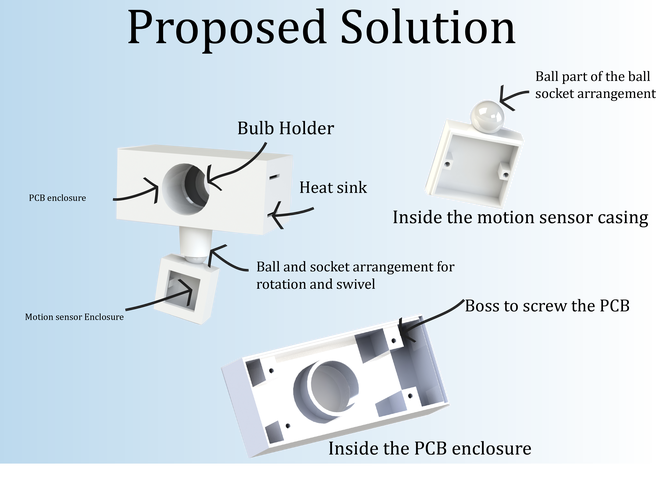
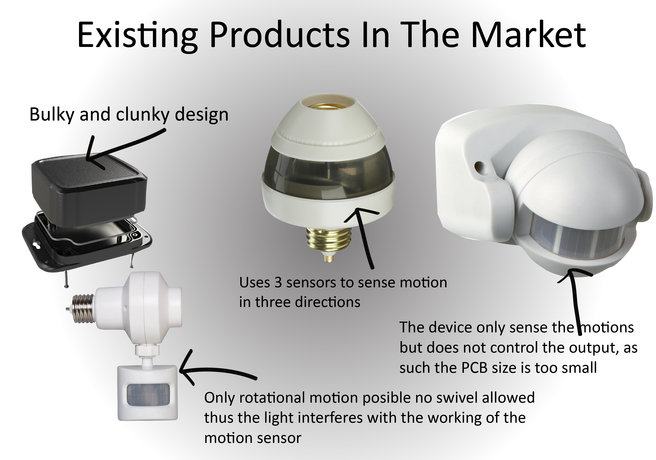
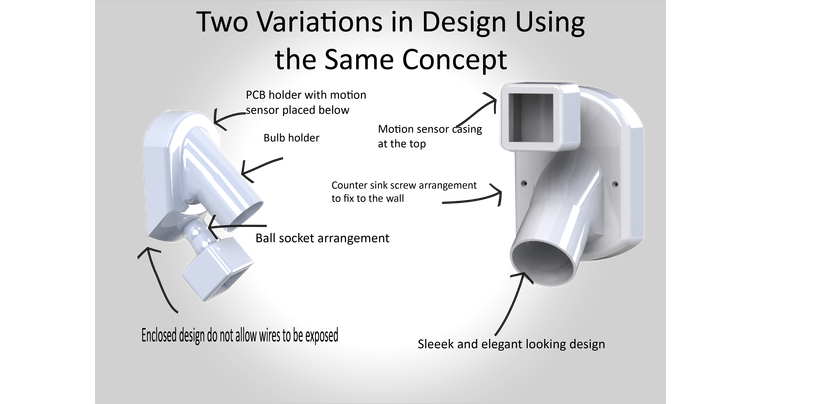
Week 13&14(September 16-September 23)
As the print quality was not as good I got the design printed from a commercial 3d printer.
This design was apprroved by the client. After a little tweaking the design was finalized, this enclosure will be taken as a reference to design the PCB.


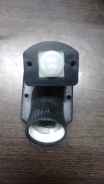
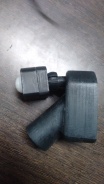
Week 11& 12(September 1- September 15)
After the approval of the client final 3d print of the design was done at DIY lab, Vigyan Ashram. The material used was ABS and the 3d printer was Accucraft i250(Single extruder).
The print quality was not up to the mark, the object lacked strength and a lot of damage was done while cleaning the object. Although this was a good representation of final product.
Week9&10(August11-August24)
In most of the cases, the sensor is blocked by closets or other things kept below the bulb socket thus the performance of the sensor is hampered.

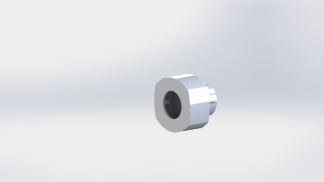



This arrangement puts the motion sensor on the top of the PCB holder. This arrangement solves our problem of sensor being blocked by closets and other things.
This design was approved by the client and we will be going for our final prototype after finalizing the shape and size of the PCB.
Week 7&8(July 28-August10)
I had few more client meetings, I redesigned the whole structure and concentrated more on the aesthetics and the look of the product.
I made arrangement for standard parts to assemble with the casing.


The design was very well received by the Client, especially the PCB holder.
Although it was decided to make the sensor casing in line with the PCB holder.
Week5&6(July14-July27)
The following design was printed on a 3d printer and tested.



3D printed model
The model was having all the features that were in the .stl file, although the finish was not up to the mark and the threads were not printed to accuracy.
I following model was presented to the client, after physically getting the feel of the product a lot of things got clear. There was a detailed discussions on the product pertaining to the shape,size, mechanism, finish of the product.
It was also decided to buy a few standard elements of the product available in the market to reduce the parts to be manufactured.
The 3D print did not have the quality as required, the finish was not good and the product lacked strength. I inquired with a few workshops in pune, I found their finish product as we required.


Week4( July 7-July13)
After making a few design trials on paper I moved to Solidworks.
First Rendered Product
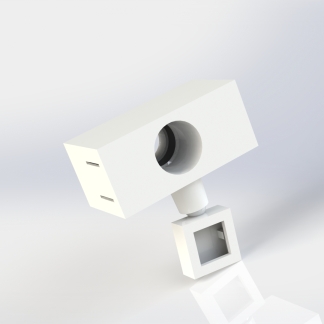

Inside of the casing

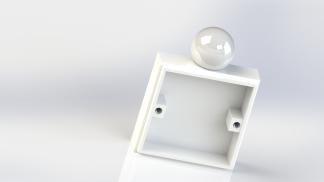

Week3(June 30-July6)
After a few more meetings with the client we decided on the problem statement. It was as follows
1 To design a working prototype of an electronic casing, the casing should be divided into two parts to hold a PCB in one part and motion sensor in another.
2 The PCB casing will be static while the motion sensing casing will have the ability to rotate and swivel to a few degrees.
3 Also there would be three wires connecting the the PCB and motion sensor which needs to be concealed and a semitransparent plastic to the motion sensor which needs to be exposed.
We also formulated a contract which was reviewed and modified by both the parties several times and a final contract was drafted and signed.
Week 2(June 23-june 29)
In order to know what the client expects we made a questionnaire and asked the client to answer the same. We also sent in a few design available samples to the client in order to work on similar paths.
Week 1( June 14-June 22)
Provenant system approached Vigyan Ashram with a design problem, the problem was to design a casing for motion activated switch.
The client had the designed the PCB of the device, we were responsible for printing the PCB and design the casing of the device.