For fabrication of designed chopper it was necessary to select a rigid material which will give stability to the chopper during operation. Hence, the proper material was selected for all parts.
1) Chopper assembly
- Crank
- Connecting rod
- Chopper
2) Vessel
3) Support structure
1) Chopper assembly
i. Crank
A designed crank length was 15 cm. Therefore mild steel plate of width 38.1 mm and thickness 5 mm was selected.
ii. Connecting rod
Length of connecting rod was calculated as 23.84 cm. Therefore mild steel plate of width 38.1 mm and thickness 5 mm was selected. In design one end of connecting rod was connected to crank and other end was connected to chopper. These revolving joints were joined together. For joining these bearing 6301 (inner dia = 12 mm, Outer dia. = 37 mm) was selected.
iii. Chopper
As per trials observations, the weight of chopper was selected 5 kg and length 50 cm. Therefore an already made chopper with pipe diameter 25 mm made up of mild steel was selected.
To restrict the horizontal movement of the chopper the guide of length 8.5 cm was provided.
2) Vessel
Temporarily it was decided to use a bucket as vessel. The bucket i.e. vessel dimensions were as per design.
3) Support structure
The support structure was decided to make with 1.5″ x 1″ rectangular tube.
⸫ Calculating strength of the cross section of tube with dimensions, 38.1 x 25.1 and thickness 1 mm.
Now, calculating crippling load for material
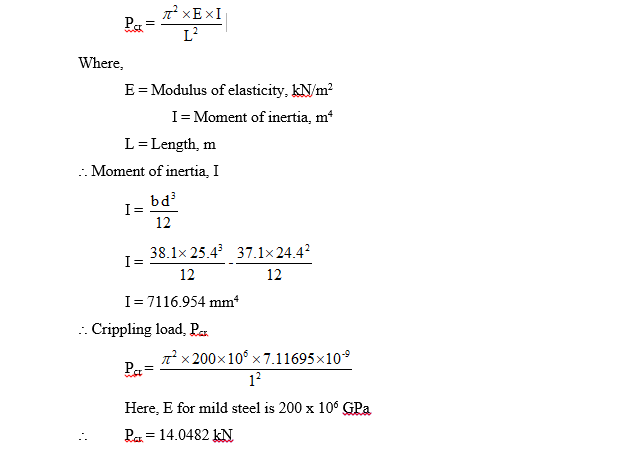
This is within permissible limits. Therefore it was safe to use for structure.
4) Motor selection
As the main purpose of development of chopper is to reduce the man power. Power requirement of chopper was 47.12 Watts and calculated torque was 22.50 Nm.
5) Chain sprocket selection
To get reduction up to 20 rpm the chain sprocket of 1:3 ration was selected. Also the torque was increased 3 times which will overcome the torque from system losses.