PROBLEM DEFINITION:
- Low capacity- Capacity of their apparatus is low and they want to increase it.
- Stirrer- right now they are manually operating stirring operation, which is time consuming ,so they need a stirrer to minimize time requirement as well as human effort.
- They required timer for their apparatus.
So, I visited Pen for observing their Nirgundi Oil Extractor.
Procedure of Nirgundi Oil Extraction AT PEN
- It is 3 days process.
- In cylinder their is mixture of Rai oil, Sesame oil, Nirgundi leaves and Garlic.
- This mixture is heated daily for 1 to 1.30 hours for three days.
- Heat is given by convection through water to avoid burning of materials.
- vapour in cylinder is condensed and water removed out by vacuum pump.
- Tap is provided to collect oil in open vessel.
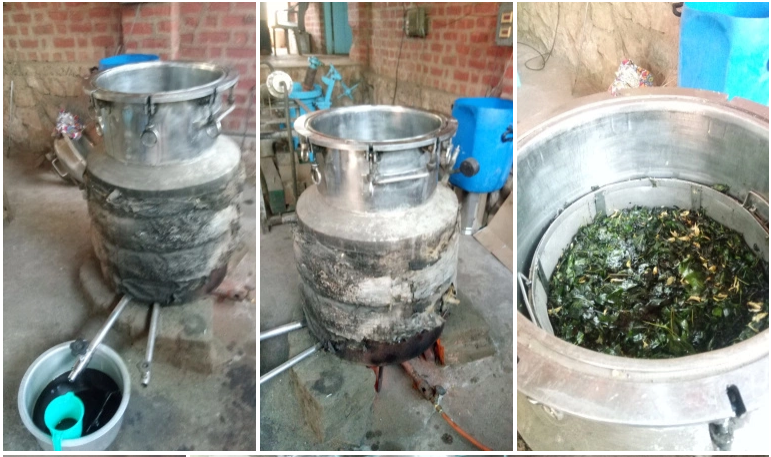
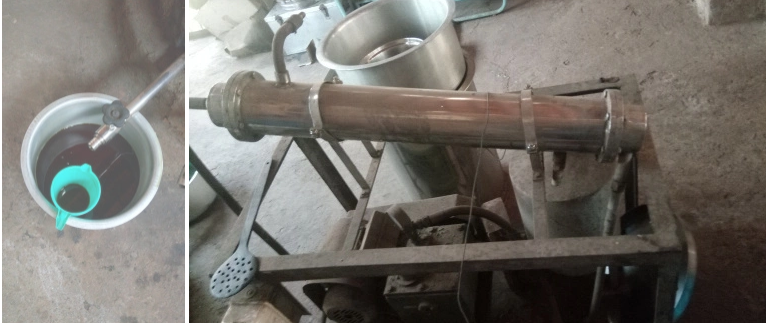
So, after discussion with Ranjeet Sir and Dixit Sir, we found that drawbacks of Nirgundi Oil Extractor at Pen.
- High cost
- The essence of Nirgundi leaves is not completely mixing with oil
So we decided not to follow same procedure.
afterwards, we have decided to follow the procedure which is defined by our customer.
Trial-
I have tried to extract Nirgundi oil by using this procedure.
Materials:
- Nirgundi leaves-250 gm
- Sesame oil-250 ml
- Water-250 ml
Procedure:
- First I have collected nirgudi leaves.
- Then measured 250 gm of leaves on weighing balance & then also 250 ml water measured with the help of measuring cylinder.
- Measured nirgudi leaves & water added in the mixer and crushed.
- Then leaves and water mixture Sieved through a cotton cloth.
- Took open vessel & poured sesame oil in it & then heated up to 5 minutes.
- Then sieved extract of leaves & water is added in sesame oil.
- This mixture is heated daily for 15 to 20 minutes for three days.
- While heating, water was evaporated from oil.
- Remaining oil is again sieved through cotton cloth.
- Rested it for 15 minutes to cool down and then after cooled oil was filled into bottle.
- The weight of leaves after extraction of water from leaves- 320 gm
- Extract- 270 ml
- The final weight of oil- 235 ml
- Waste from extract- 0.020 gm
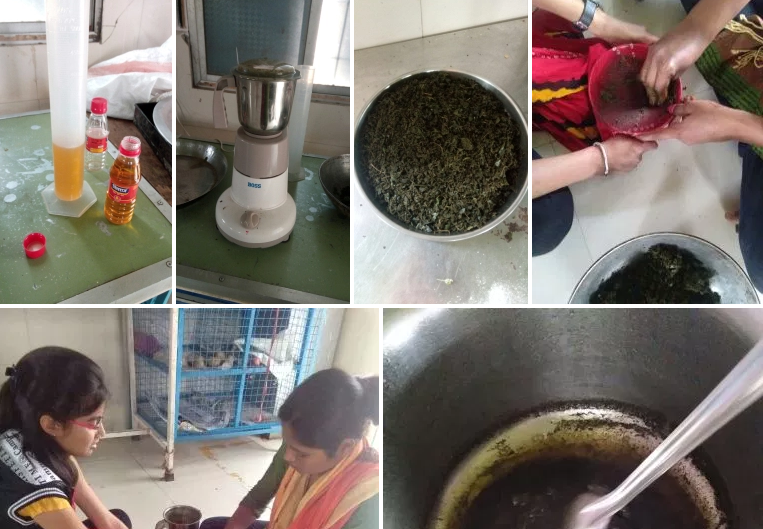
We made Nirgudi oil by using this procedure
Then, Ranjeet Sir told me to search about Autoclave, open vessel, commercial cooker, Over head stirrer, burner with stand, motor, Gear box on indiamart.
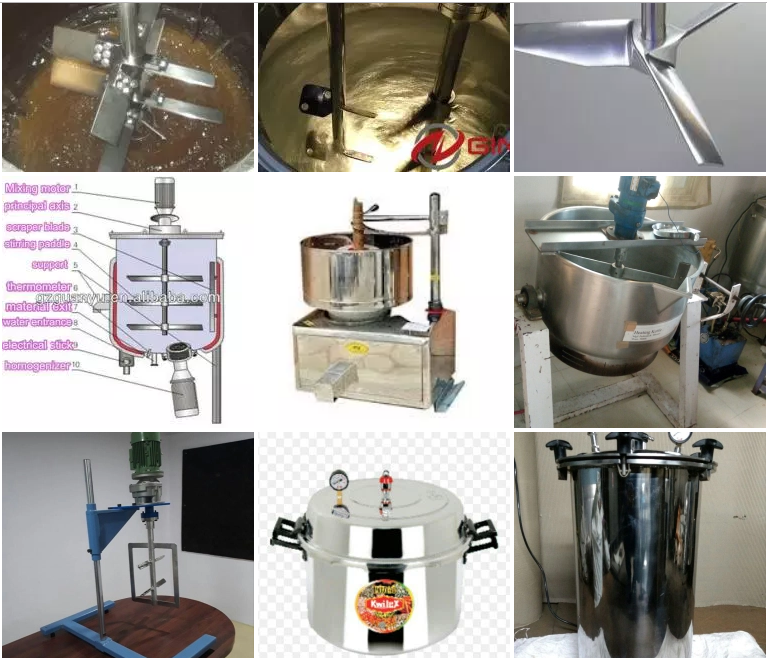
Then we decided one design,

- We needs to work on stand, their additional support required for stand which adds cost and motor is offcentered its better support to these design as these difficulties.
- Rate of evaporation was drop because it was close vessel therefore it should be open vessel.
- Then we decided not to final this design as it will not operate properl because of close surface evaporation will not happen.

- Theses design of open vessel whose bottom shape is incline, so that remaining water can be drain out through tap.
- But these design was also cancelled because as per discussion with vaishali mam all water should be evaporated.
We zero down on the process & the process is the evaporate water completely, we will not separate water, we are supposed to evaporated water completely the sludge which remains at the bottom when press with fingers should form thread is confirmatory test for complete dehydration. Hence we decided not to go with separation process, hence fixed with open vessel to accelerated rate of evaporation.
IIT/YMC equipment did not have stirrer hence there was principle possibility of low mass transfer, homogenized mixture, even temperature with in the bulk.
The typical batch size expected by our customer is 25 or 30 litters of nirgudi oil. 25 kg of nirgudi leaves and 25 or 30 litters of water extract is supposed to be mixed with equal amount of oil. These oil and water mixture is subjected to heating to evaporate water these will result in active ingredient of nirgudi of oil.
We had no clear idea of temperature profile of these process. as describe in Ayurveda & mention by our customer we decided to take a trail to get feel of the process & temperature profile.
Trial-2
I have taken, 100 ml of water & 100 ml of oil measured with the help of measuring cylinder and taken thermometer using by measured temperature of this mixture.
This was the temperature reading while making Nirgudi Oil:-
From this reading the process is not going onwards 120 degrees Celsius. After taking trials and colleting some data we have finalised some procedure that how will machine work.
Time(min) | Temperature( ˚C ) |
0 | 30 |
1:00 | 75 |
1:30 | 85 |
2:00 | 85 |
2:30 | 94 |
3:00 | 97 |
3:30 | 100 |
4:00 | 110 |
5:15 | 115 |
6:00 | 120 |
Ideation:-
We have to take vessel for maximum batch of oil they want to make. To final that dimensions of open vessel we carried out following calculations:-
- Diameter=60 cm, Height=30 cm then, Volume=70 litre
- Diameter=50 cm, Height=36 cm then, Volume=70 litre
- Diameter=55 cm, Height=33 cm then, Volume=70 litre & L/D ratio =0.6
- Diameter=55 cm, Height=30 cm then, Volume=71.27 litre & L/D ratio= 0.5




Selection of Idea:-
We are decided the final dimensions of open vessel. And these are,
- Diameter=55 cm, Height=30 cm then, Volume=71.27 litter & L:D ratio= 0.5,
We have to take vessel which is nearly equal to this dimensions.
Basically this project was related to automate the whole process of Nirgudi Oil. We had finalised some designs and materials and processes how we will make this machine.
Design:-
We have finalised this kind of design:-

We discussed all materials required for this automation process. All material should be stainless steel as per ayurveda for oil making process. So we make all material list and purchased this from various markets in Pune.
We have finalised this project material list for making this machine:-
Sr. No. | Part | Sub-Material |
1 | Open Steel Vessel 90 litre | ● Ball Valve● Socket |
2 | Burner | ● Gas Pipe |
3 | Stirrer | ● Shaft(Stainless Steel Rod)● Sleeve with 6205 Bearings● Bush● Steel thick plates● Threaded rod● Nuts● Bolts● 4mm hollow pipe,● Nut and Bolts, Washer |
4 | Tube frame for supporting motor | ● S.S. plates frame supporting for Motor and Stirrer |
5 | Motor | ● Torque:-28 kg cm● 1 RC● Siemens Box for RC● Insulation for wire● 3 core wire● 3 pin |
We bought this material from Rameshwar Chowk, Bhori Ali, Shukrwar Peth, Pune.
Some material was provided by Anil sir from his workshop. We bought S.S. material from Milan Metal, Katraj. We bought Ac synchronous motor from Srijan Control Drives, Katraj.
Costing:-
- Raw Material Cost :-
Sr. No | Component | Material | Rate(Rs.) |
1 | Shaft | S.S | 850 |
2 | Bearing | S.S. | 1800 |
3 | Sleeve | M.S | 1550 |
4 | Bush | S.S | 950 |
5 | Blades/Plates (Stirrer) | S.S | 1200 |
6 | Vessel Holding Material | M.S. | 800 |
6 | Baffles Plates | S.S | 2100 |
7 | Tube frame | S.S | 3582 |
8 | Siemen Box Frame | S.S. | 1100 |
8 | Simple frame | S.S | 800 |
9 | Machining | S. S. | 4000 |
10 | Filter | Plastic |
- Manufacturing cost :-
Sr. No | Machine used | Time (hour) | Rate/hour | Total |
1 | Lathe | 4 | 200 | 800 |
2 | Shearing | 2 | 180 | 360 |
3 | Press brake | 2 | 180 | 360 |
4 | Welding | 4 | 400 | 1600 |
5 | Cut off | 1 | 160 | 160 |
6 | Drill | 2 | 120 | 240 |
7 | Grinder | 1 | 180 | 180 |
- Standard component cost :-
Sr. No | Component | Quantity | Rate/unit |
1 | Burner | 1 | 1500 |
2 | Open steel vessel | 1 | 7200 |
3 | Hardware(Ball valve, Socket, Check nut) | — | 2030 |
5 | AC Synchronous Motor | 1 | 5817 |
6 | Love Jaw Coupling | 1 | 371 |
7 | Insulation Box (Siemen box) | 1 | 645 |
8 | 3 core cable | 1 | 40 |
9 | Three pin | 1 | 50 |
12 | M12 Stud*1000 | 2 | 500 |
13 | M6 Stud*1000 | 1 | 90 |
14 | M12 Nuts | 16 | 288 |
15 | M6 Nuts | 24 | 54 |
16 | Washer(M12) | 16 | 80 |
17 | Washer(M6) | 24 | 38 |
Manufacturing Process:-
- We fabricated burner to fix steel vessel, the fabricated burner will hold the 90-liters volume of S.S. vessel to heat.


2. After that we fabricated steel vessel and give outlet port of ball valve and socket drain out the oil, steel vessel is fabricated and fixed with one ball valve with socket to drain out final product.
3. We fabricated 4mm thick hollow tube frame to hold the motor and stirrer, hollow tube frame will hold the motor and stirrer
4. We have fixed motor and stirrer shaft in sleeve with bearings, Motor will rotate the shaft of stirrer through love jaw coupling and sleeve will hold the motor and stirrer shaft
5. Again we fabricated stirrer blade in bush, stirrer blade is fixed in bush, this will rotate stirrer shaft and will create vertex, mixture of sesame oil and extraction of Nirgudi leaves.

6. RC(Regulating circuit) unit and Motor :-
This box is input of Motor, motor requires 230V and 10A. This RC unit is providing exact power input to motor.
7. Programming box of temperature :-

In this box we have set temperatures for buzzer. At 60 degree Celsius buzzer will sound two times and green LED will blink. At 80 degree Celsius buzzer will sound four times and yellow LED will blink. From 110 to 1250C buzzer will beep continuously sound and red LED will blink continuously. After 125 buzzer will sound continuously and red light will on. Red LED and buzzer will indicates that we have to stop the heating process and turn off the gas.
8. Final assembly of this unit :-

After making this unit we have to take trial on this model. So we did whole process and take trial on this model with Rural Communes.
Trial in Final Model:-
- While chopping the Nirgudi Leaves:-

2. While grinding the Nirgudi Leaves:-

3. While mixing water in grinded Nirgudi leaves to make extract:-
4. While filter the extract from grinded Nirgudi leaves:-
5. Remaining dried Nirgudi leaves after extraction:-

6. While pouring the Sesame oil in vessel:-
7. While heating sesame oil up to 60 degree celsius:-

8. While adding extract of Nirgudi leaves in vessel of heated Sesame oil:-

9. While stirring the mixture of Nirgudi extract and sesame oil:-
Results:-
After all these procedure I have taken trials on the mixture of sesame oil and nirgudi extract for 3 days.
1st day:-
Sr. No. | Time(min) | Temperature(˚C) |
1 | 02:00 | 34 |
2 | 02:10 | 40 |
3 | 02:30 | 48 |
4 | 02:40 | 57 |
5 | 02:50 | 66 |
6 | 03:00 | 75 |
7 | 03:10 | 85 |
8 | 03:20 | 94 |
9 | 03:30 | 104 |
10 | 03:40 | 111 |
11 | 03:50 | 112 |
2nd day:-
Sr. No. | Time(min) | Temperature(˚C) |
1 | 04:25 | 35 |
2 | 04:35 | 41 |
3 | 04:45 | 49 |
4 | 04:55 | 58 |
5 | 05:05 | 68 |
6 | 05:15 | 76 |
7 | 05:25 | 94 |
8 | 05:35 | 105 |
9 | 05:45 | 112 |
10 | 05:55 | 120 |
3rd day:-
Sr. No | Time(min) | Temperature(˚C) |
1 | 03:07 | 34 |
2 | 03:17 | 47 |
3 | 03:27 | 60 |
4 | 03:37 | 76 |
5 | 03:47 | 85 |
6 | 03:57 | 95 |
7 | 04:07 | 104 |
8 | 04:17 | 111 |
9 | 04:27 | 115 |
10 | 04:37 | 117 |
11 | 04:47 | 117 |
12 | 04:57 | 119 |
13 | 05:07 | 120 |
14 | 05:17 | 120 |
After three days water from the mixture is not evaporated completely, since oil is not ready. Then we have to extend the procedure and give more heat:-
4th day:-
Sr.no. | Time(min) | Temperature(˚C) |
1 | 03:00 | 34 |
2 | 03:10 | 45 |
3 | 03:20 | 56 |
4 | 03:30 | 67 |
5 | 03:40 | 88 |
6 | 03:50 | 97 |
7 | 04:00 | 111 |
8 | 04:10 | 114 |
9 | 04:20 | 114 |
10 | 04:30 | 115 |
11 | 04:40 | 117 |
12 | 04:50 | 119 |
13 | 05:00 | 119 |
14 | 05:10 | 120 |
5th day:-
Sr. No. | Time(min) | Temperature(˚C) |
1 | 03:00 | 35 |
2 | 03:10 | 41 |
3 | 03:20 | 49 |
4 | 03:30 | 58 |
5 | 03:40 | 68 |
6 | 03:50 | 76 |
7 | 04:00 | 94 |
8 | 04:10 | 105 |
9 | 04:20 | 112 |
10 | 04:30 | 120 |
Conclusion:-
- The process describe by Vaishali Gavande mam was heating of oil-water mixture 2 to 2:30 hour for 3 days. we observed that these resulted in 14 to 15 % evaporation of water with in the bulk.
- The process becomes easy, less time consuming and cost effective with more safety. Large scale production can be happen upto maximum 40 litrs.
- Through out the process excessive splashing was not observed or splashing of oil stroke water outside the container was never observed.
- Process was free from human intervention & does not need attendant in case of power failure the process could result in uncontrolled splashing & needs alarm which apropos which is part of system.