Introduction:-
Mr Prasad Patil, a teacher at Vigyan Ashram, informed us about an inclined flat dryer in Solar Park. Unfortunately, this dryer is not functional due to prolonged disuse and lack of regular maintenance. Several parts of the dryer are malfunctioning, prompting the need for repairs. Mr Patil intends to replace the problematic components in the system. Additionally, we are considering making the system more user-friendly and straightforward to operate.
Objective:
We aim to simplify the operation of that system.
We are exploring ways to enhance the maintenance process for the dryer.
We are evaluating its operational efficiency.
We are also investigating methods to enhance its efficiency.
8/03/2023 Prasad Sir, Mahesh Sir, and Dixit Sir were at the location for the discussion. The aim of the discussion was:
This is why we don’t use solar park dryers every day. I came to this understanding through observation.
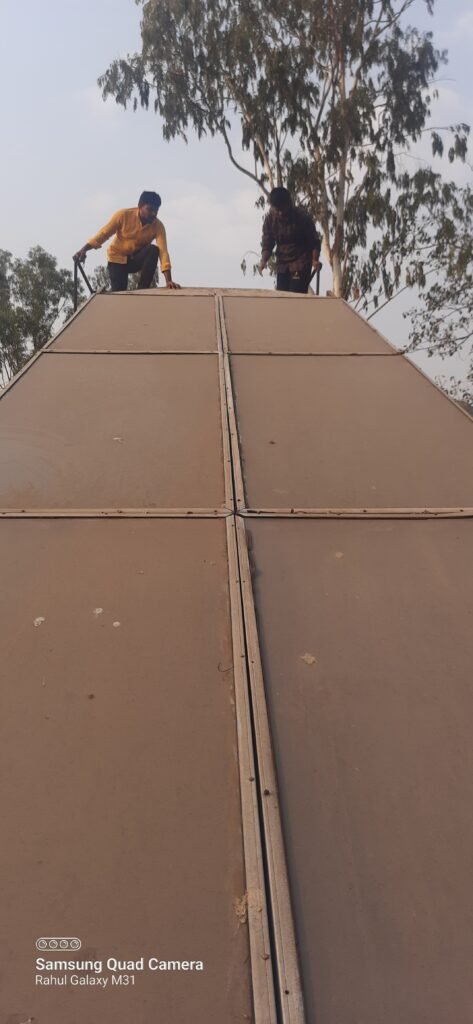
I discovered the following during the survey.
- The outer surface of the body is torn, and this chamber contains hot gas that can escape from that hole. The hole is where the air exits, which we use for food drying. We need to clean the glass as it’s dirty. If it’s not cleaned, the system’s efficiency decreases.
- Because the glass is dirty, the black absorber plate won’t let sunlight in completely. The rubber packing (gasket) around the doors is damaged.
- In the chamber, there’s hot gas that can leak if the door gasket is missing. Welding is required for five hinges. Due to the partially enclosed door, heated air can pass through it.
- There isn’t an exhaust fan to expel the air.
- A black surface is beneath the glass, but it needs repainting as the colour has faded. The heat isn’t fully absorbed due to the faded colour.
- From our survey, we deduced that the system has multiple issues following the initial investigation.
- We noted that there are only 50 trays available in the system. There are 14 trays of different sizes and shapes. The device can accommodate 80 trays simultaneously, so we need to make 30 more trays.
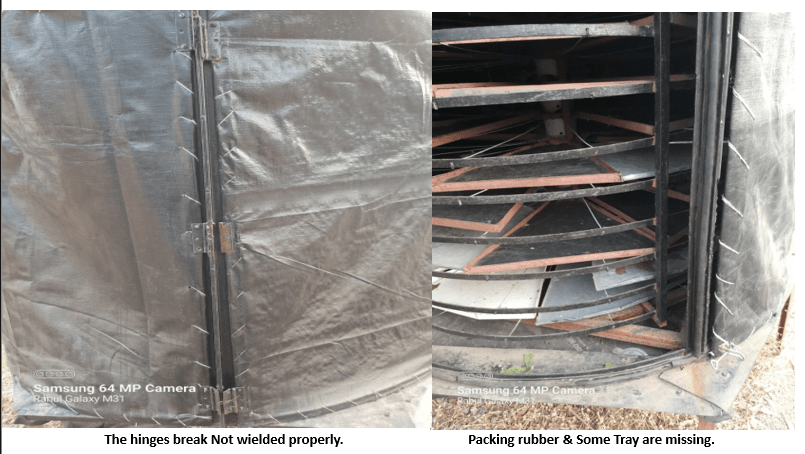
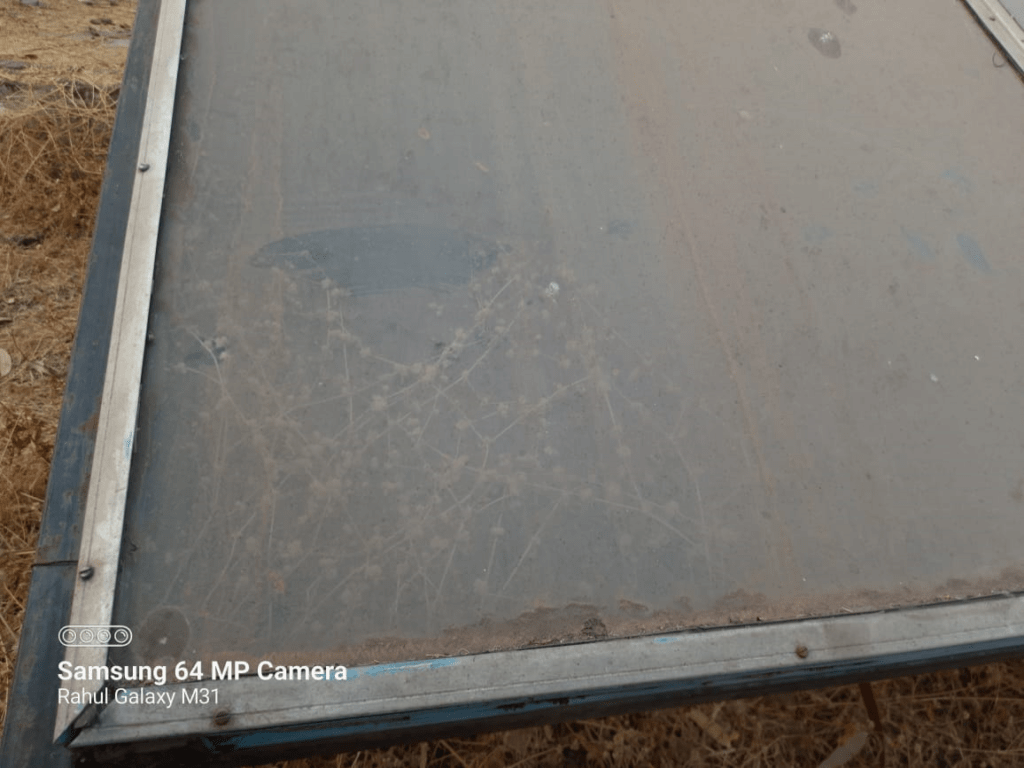
09/03/2023
I talked with Dixit Sir about the missing trays, and during that discussion, we addressed the following points:
I examined the material or solution used to attach the black paper to the tray.
We conducted tests with various options. Fevikwik, a hot air gun, and a glue gun were tried for attaching the paper to the body. However, all of these methods failed.
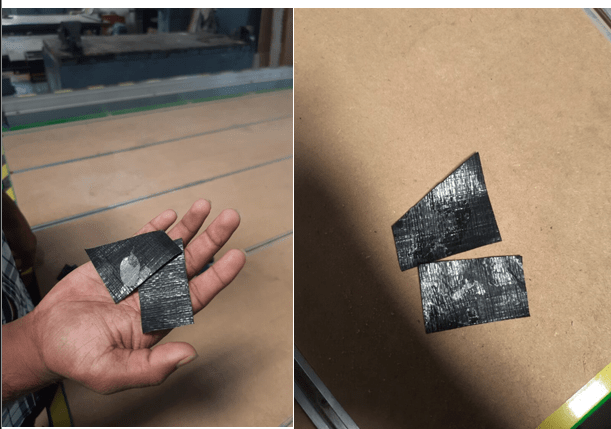
- I confirmed that the glue gun was able to bond black paper to paper, but we found out that the glue gun wasn’t effective for this purpose.
- I rechecked to ensure that the solution wasn’t used to attach white paper to black paper, and we confirmed that it wasn’t.
- I confirmed that the hot air gun had been used to attach black paper to paper, but They’re not gonna attach.
The conclusion of the experiment is.
We patched it using a pin and a small wire. We placed paper over the hole, secured it with pins, and sealed it to prevent air from escaping. Then, we added another layer of paper and sealed it using adhesive tape. In this manner, we created an airtight seal.
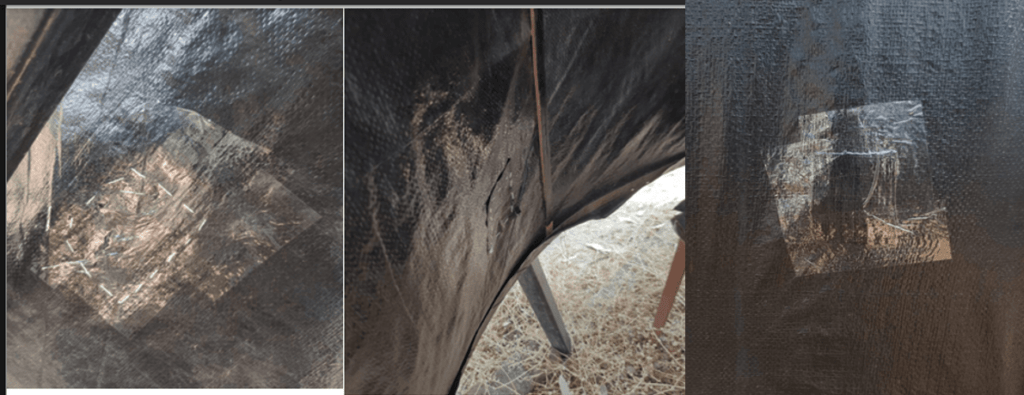
objective of discussion
We’ve concluded that the door’s gasket is entirely absent. This means the door has the most significant issue with hot air leakage.
To address this, we’re exploring different soft materials to create an airtight seal for the door. We’re using these materials as makeshift gaskets to prevent air from escaping.
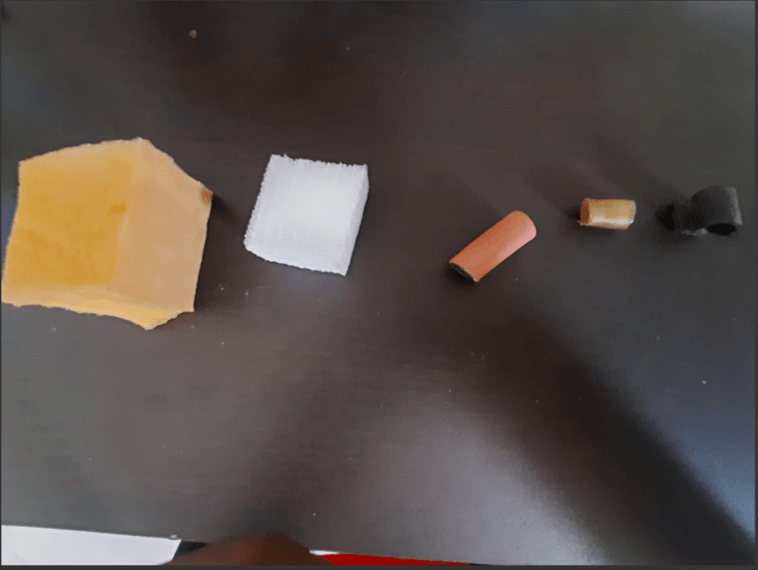
we chose the second one for the door ceiling.
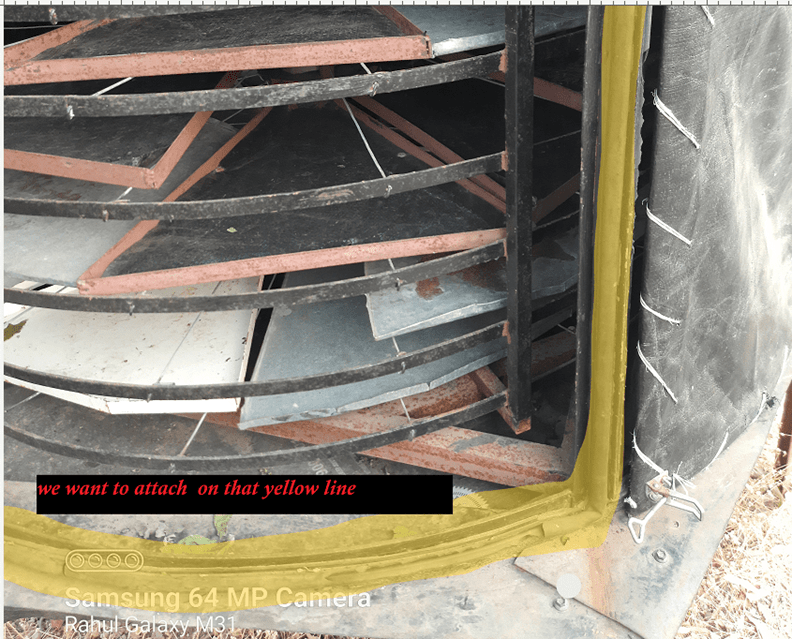
The Gas Kit cannot be properly attached to the door.
Conclusion of discussion.
Self-locking screws and double tape are used for that. (We use double tape between the door and that plastic. We employ a self-locking screw for impenetrable attachment.)
Thinking about the next problem. That is as follows.
The 4 hinges haven’t been properly welded, so please weld them securely. We use vending machines to assist in the fixing process. It’s necessary to wash 6 glasses. We take care of washing the glasses. Up until now, this much fabrication has been completed.
13/03/2023
objective for the meeting.
We had a discussion with Mahesh Sir, Prasad Sir, and Dikshit Sir regarding the possibility of replacing the glass with a polycarbonate sheet.
During the discussion, we explored the advantages of using a polycarbonate sheet as a replacement for the glass.
Conclusion of discussion.
Using polycarbonate instead of glass brings simplicity in handling, operation, and maintenance. We gain these advantages by making this switch.
Another significant benefit is the improved efficiency of the system.
We discussed this topic during a meeting.
Start remaining fabricating.
After this meetings remove the glasses from the dryer. For cleaning the glass and painting the observer plate.
15/03/2023
Remove the glasses from the dryer. For cleaning the glass and painting the observer plate.
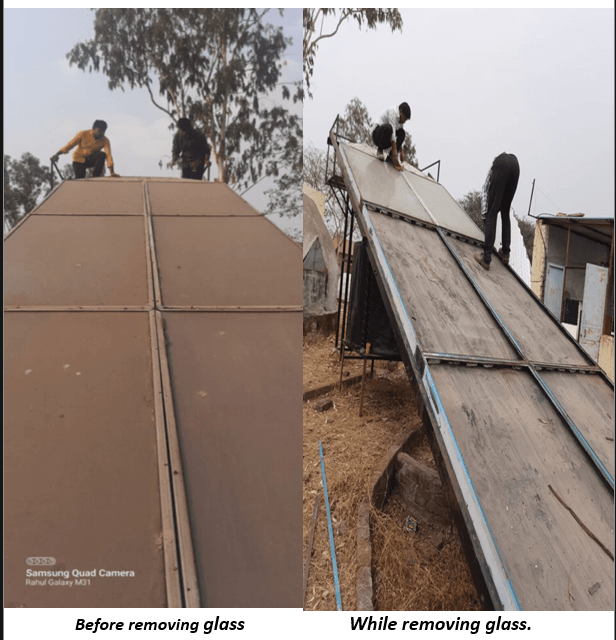
16/03/2023
Fabrication
For reprinting, use a wire brush to remove color from the surface.
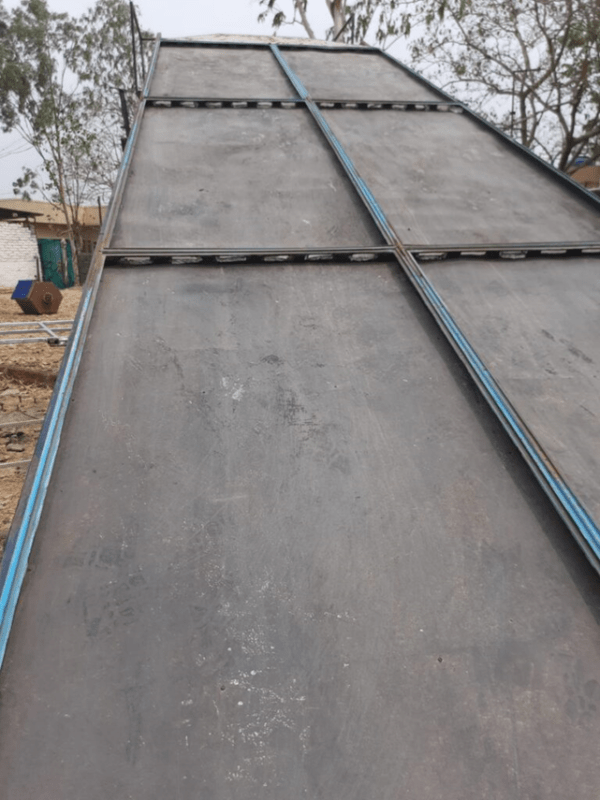
21/03/2023
Once the colour has been removed. We Dixit Sir, talk about the exhaust fan.
The purpose of the discussion is as follows:
- Determine the appropriate exhaust fan for the dryer.
- Calculate the amount of heat being emitted from the surface.
- Calculate the necessary amount of heat for our requirements.
- Calculate the area that absorbs solar energy, which is 11.97 square meters.
- Calculate the energy absorption from the sun per square meter, which is 23.11 megajoules.
We reevaluated the previous exhaust fan selection criteria for the dryer due to incorrect calculations.
Solution of objectives
The efficiency of flat plate solar dryers=30% (minimums 30% because evacuated tube water heater efficiency is 55-60% we calculated on our privies blog)
how much energy do we receive from the sun in that area
=11.97*23.11*106*0.3……………………………………………(our area, in one m square how match light or rya fall & 30% efficiency of dryer)
=82.98*10^6 joule
For fan selecting (cfm)
Convert joule to kilojoule.
=82980*10^3 ………………………………….1000 lit
1.29kg (air density)
=3319.2 kg/ (1.29)
=2573 m^3………………………………………….m^3 to ft^3(Switch calculate fan speed with the help of CFM means cubic feet per minute.)
=90865 ft^3…………………………………………. for cfm
=90865/ (12*60)……………………….. (Daytime in two seconds).
=126.2 ft^3/min
Our requirement is 126 CFM (If you want to use that fan for 12 hours a day, then we use a 126 cfm fan.)
In VA two fans are available so want to use that fan as an exhaust fan. So, we calculate the cfm of the fan of that fan.
After the selection of the perfect fan, we create a bill of material. Of the dryer how much does it cost goes for repairing purposes?
So the final bill of material is as follows.
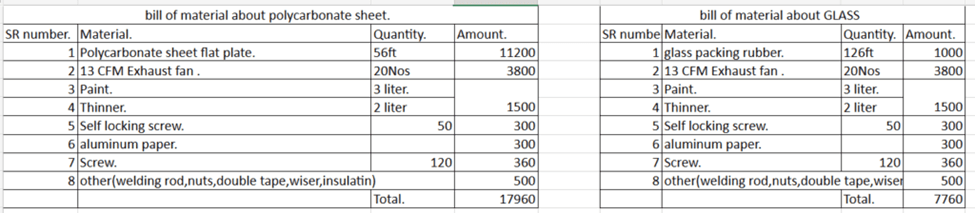
Book1.xlsx bill of material
22/03/2023
the objective of the discussion.
We talked with Dixit Sir about how frequently and for how long we should run the fan. I gave it some thinking. for the purpose of removing humid air.
conclusion of discussion
1>For 12 hours, we continuously move humid air using a fan.
or
2> After a while, we utilize a fan. When the dry air exits the absorber plate, it is then captured in the chamber. The dry air will then take on water molecules from our product, turning into humid air. That humid air, which we detect with the sensors and expel after a while.
Since there are only two fans in VA, you should use one of them as an exhaust fan. As a result, we determine the fan’s cfm. We were instructed to determine the fan cfm, thus we did the following calculation:
- We construct a duck to calculate the cfm using the two fans.
- Their air spreads out everywhere, therefore We created a duck. As a result, we want to collect afterwards. As a result, we created that duck.
- We may determine the air velocity using an anemometer, which provides a reading in feet per minute.
- Determine the surface area of that fan.
- You need change those feet per minute to cfm.
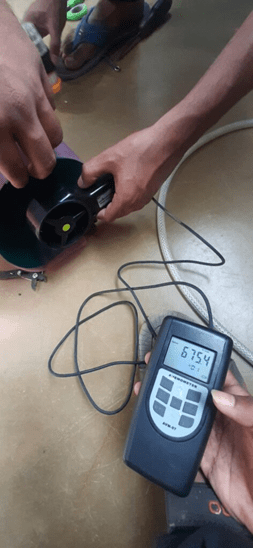
https://www.easycalculation.com/unit-conversion/fpm-to-cfm-calculator.php
With the help of this link, you can calculate
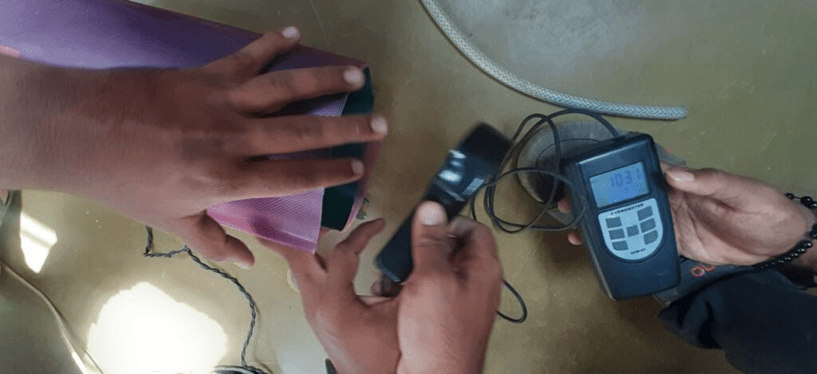
1>First reading of fan fit per minute reading is 1000& the area of that fan is 28.700 inches square.
CFM=199.3056
2>second reading of fan fit per minute reading is 2000 & the area of that fan is 203 inches square.
CFM=2819.44
23/03/2023
We came to do the rest of that dryer work.
Clean all absorber plates with water in preparation for painting.
25/03/2023
We started the rest of the painting work.
For painting purposes, water alone can not effectively remove dust, therefore we also use sandpaper and a grinder to remove pigment. We must clean it because the colour is not directly affixed to the surface. earlier colour.
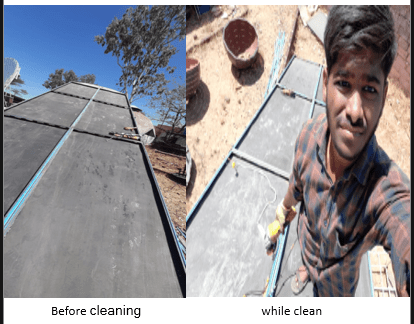
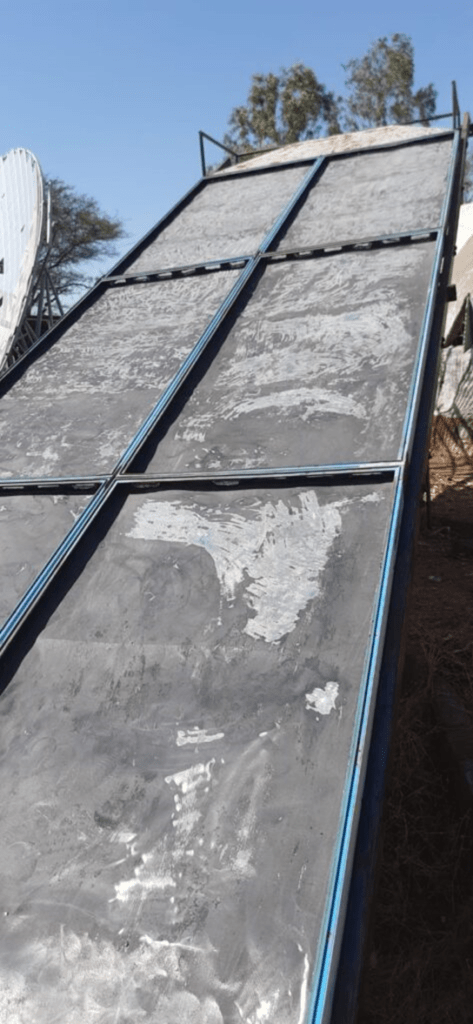
After cleaning.
25/03/2023
We had a discussion with Mahesh, sir after we had completely removed the color.
Objective discussion.
How many layers of paint are sufficient for painting the absorber plate?
conclusions of meeting
Because the absorber cannot fit in the first layer, due to the thinness of the surface paint. We must thus make a plate that is darker. We colour the two layers for this reason. to absorb heat more effectively.
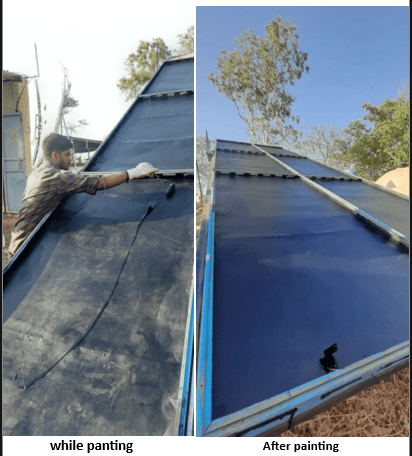
27/03/2023
We are unable to use the corner side’s rubber gasket since the rubber had dried out. We remove the hot air and clean the glass because they are unable to seal it.
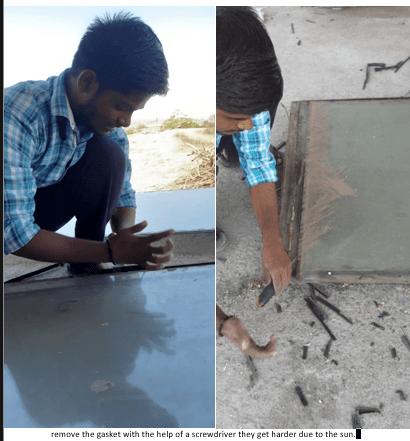
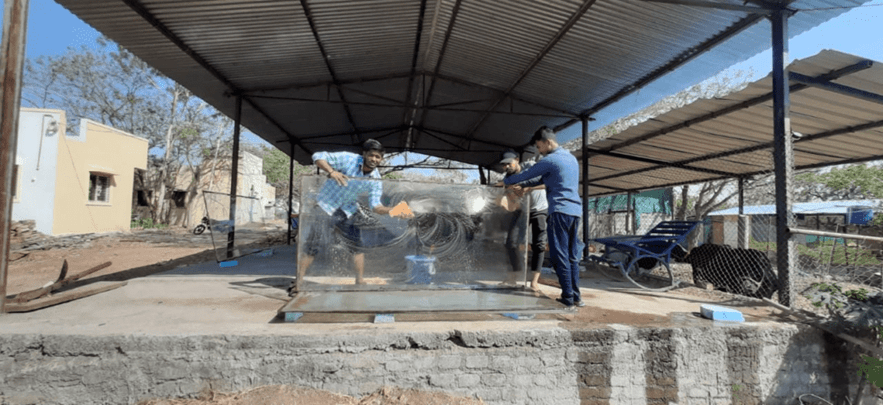
The glass washing.
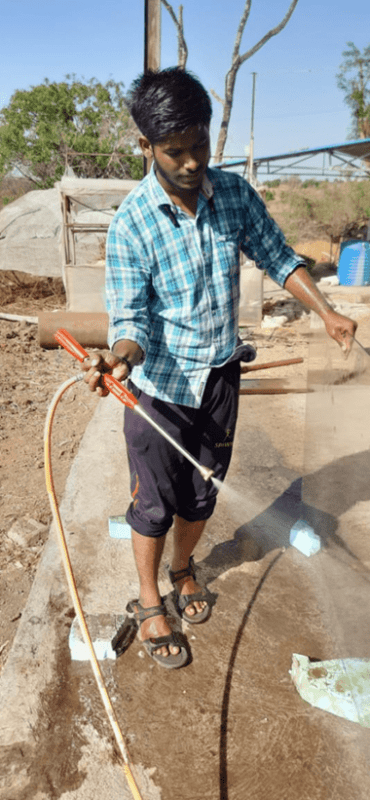
28/03/2023
The main issue is that this technology is quite challenging to use to open the glass for future maintenance requirements.
After these upkeeps, we believe that a fresh student would find it challenging to sustain.
The primary issue is as follows:
1> Glass removal
2> Alternatively, clean the chamber before painting the black absorber plate.
3> Leaks in the spaces between the two chambers
For avoiding this term, we redesign the system
we discuss this with Dixit sir about this
in this meeting we discuss are as fellow:
1> How we remove the glass.
2> how to paint.
the conclusion of our meeting
We talk about how to open the glass at that meeting. How should I clean the glass? In that meeting, the first thought that occurred to me was how to paint the absorber plate. The absorber plate is opened from the box’s base up.
One issue arises from doing this, and the solution is a box or absorber plate construction. Before we can open the glass, we must first remove the three layers (beam layer, horizontal metal strip layer, and insulation layer) that are below the absorber plate. Opening the three levels is really challenging. This is why we decided against this strategy.
Is that doing the glass frame and adding hinges so we can open the glass easily?
29/03/2023
So, in order to design a frame for the glass, we conducted a market survey.
Make a bill of materials that details how much it will cost to build the frame according to our calculations.
Therefore, we make a bill of material from that. Download Frame’s bill of materials
30/03/2023
We talked about the bill with Prasad and Dixit sir, respectively.
We talked with a fabricator to construct a glass frame because we are aware that we are unable to make the frame.
for doing all of the tasks we desire, Bom, so this is as a fellow
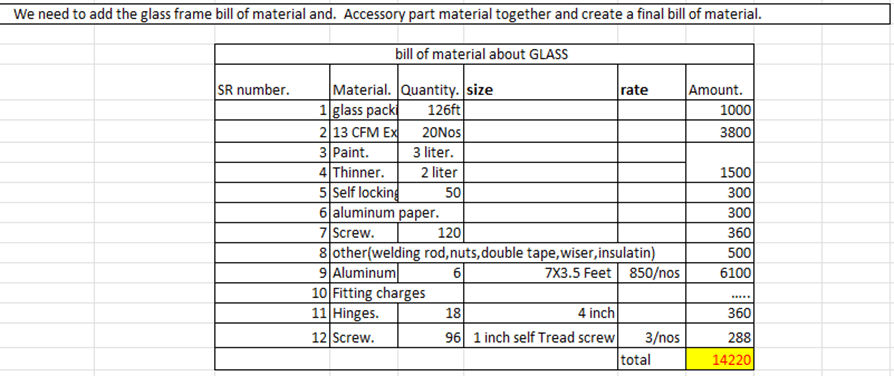
05/04/2023
This match conversation has so far been ongoing. We now consider how many days it will take for income to start coming in, and we figure out how to equal that income per day.
We contrast the two methods, inclined plate drier and flat plate dryer. Which system is going to give you the best income? We compared them.

10/04/2023
Discuss this with Kulkarni sir above bill. They told me that fit the glass without frame and take a reading at least once within a season.
11/04/2023
After that, we fix the glass and add the rubber for air sealing.
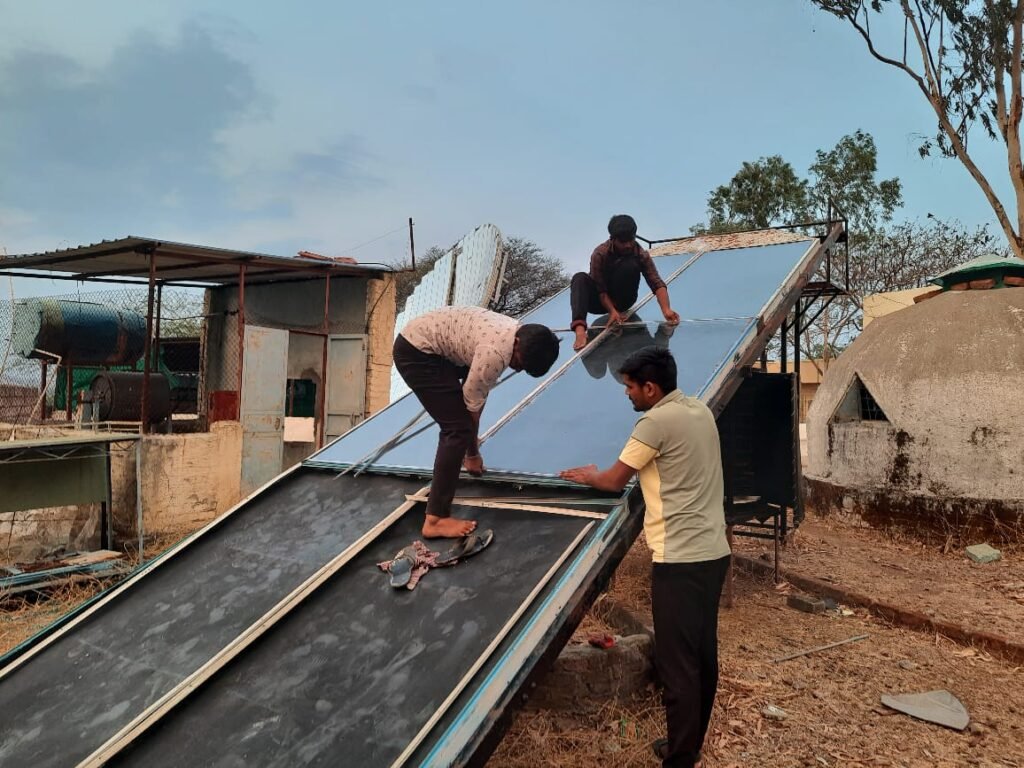
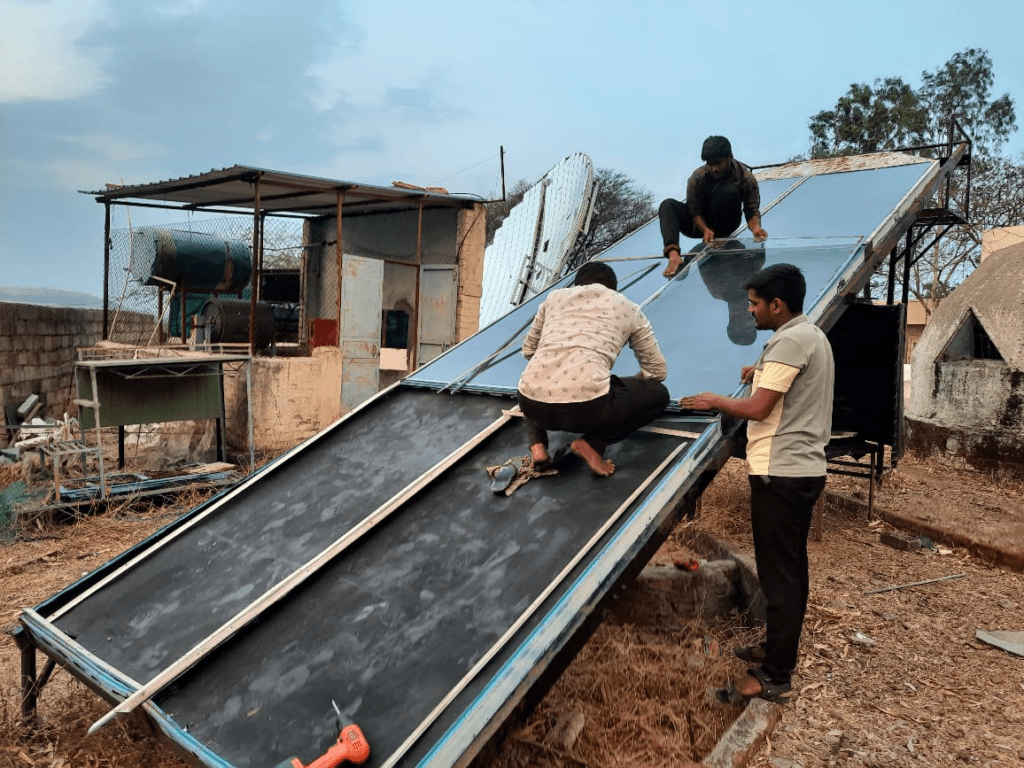
I get assistance from Amol, Mahesh sir, Sumedh, and Ghansham dada to fix the glass.
13/04/2023
Perform a final survey with Prashad sir to determine any lingering issues before handing everything over to the lady. I discover a few issues. I made it better.
Complete the glass’s repair.
While taking out the glass, I see that two strips are missing, so I add two more of my own.
Fix each tray. We patch the surface by adding a screw and repairing the base cover.
Fix the door’s hinges.
And I handover dryer to Reshma Madam.
We must prepare one of the dryers after handing over the other.To dry the vegetables, we take 6KG. on April 14, 2023. After placing it in the dryer and calculating the LOD, we discovered that the vegetable contained 90.6% water. preceding dryer
Additionally, read the chamber without a fan.
Late and outlet pipe temperature in that chamber. Temp. of the absorber plate’s inlet and outflow. temperature and humidity of the air.
We are aware that the absence of a fan prevents dry air from entering the chamber since the height of the chamber’s absorber plate is different (see fig).
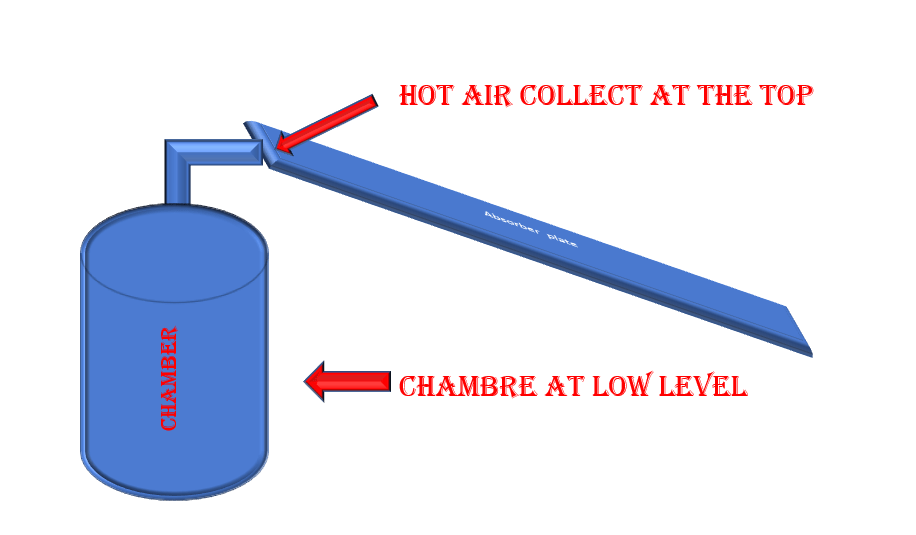
The density of the hot air is so low that lower levels of air cannot be reached. Therefore, convectional flow is necessary. We decided to take a one-reading till the fan we purchased arrived. The data sheet looks like this.
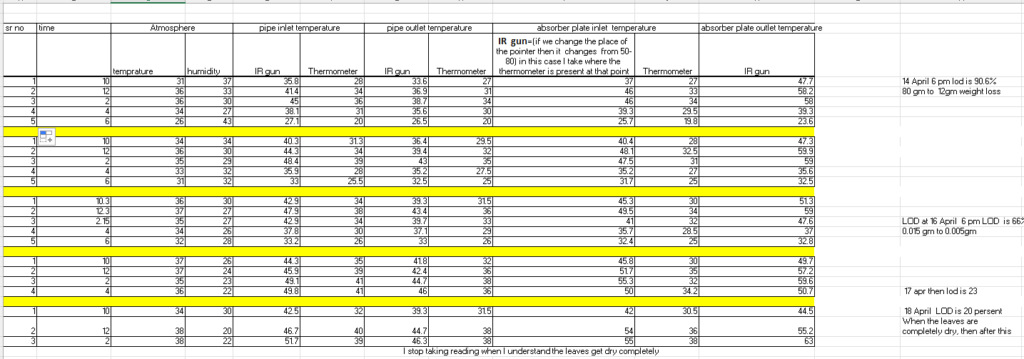
This makes me wonder how much spinach we would obtain if we added 6.100 kg of spinach.
We require 4 days in that chamber without a fan for it to be entirely dry.
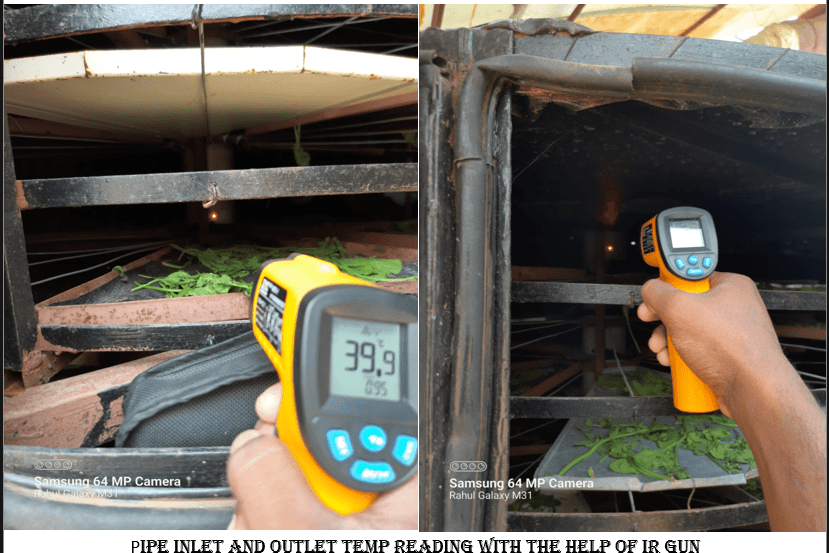
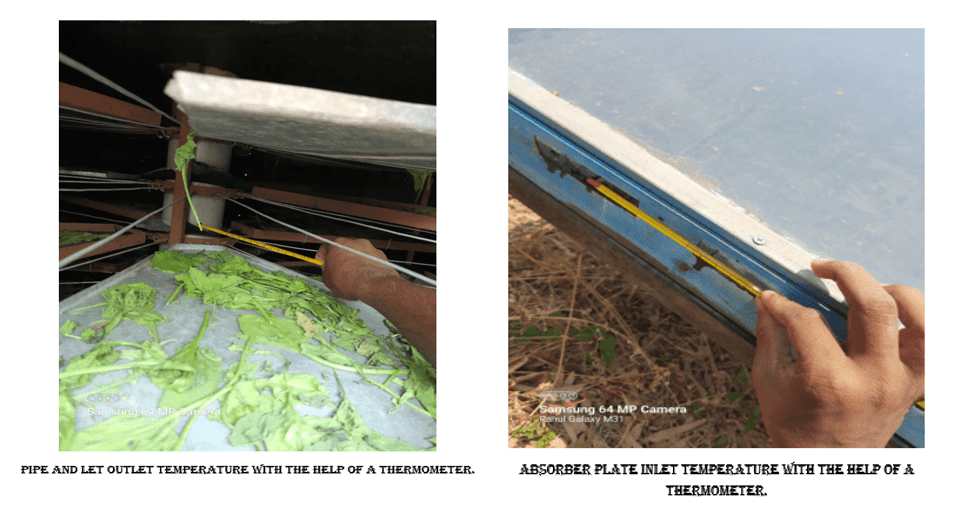
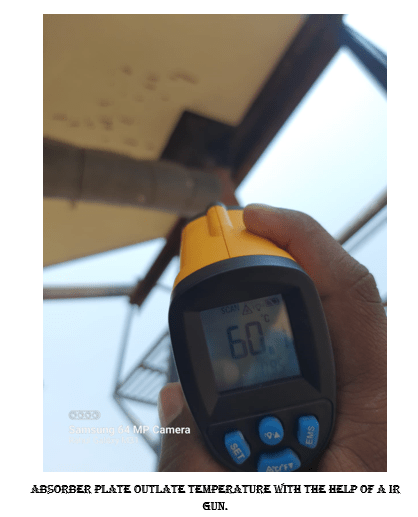
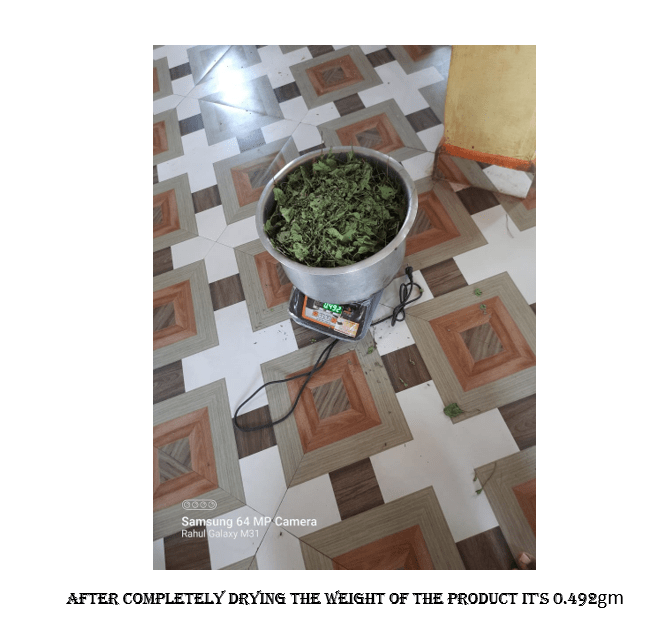
After that, we calculate the efficiency of the dryer, which we are using with high of following data.
Given data
water weight loss=5,608 gm
area of absorber plate =11.96m square
the light intensity with time =25.6
latent heat=2260kj/kg
Output Formula.
=weight loss*latent heat/are
=5608*2260/(11.96)
1059705.68
convert to megajoules
1.059705*10^6
input
=light intensity
=25.6*10^6
= (Output/input.)*100
=4.13% efficiency
This is the efficiency of the dryer without a fan. Now we install the fan to the dryer.
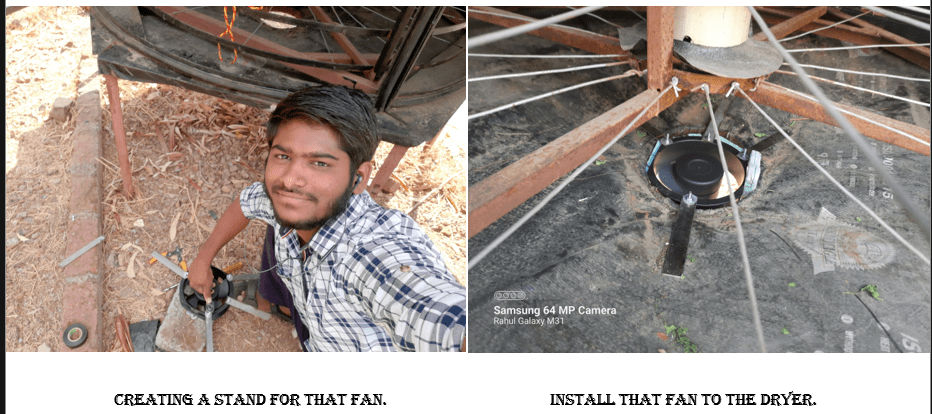
Now, seven kilograms of beet were chopped and loaded onto a flat dryer. & and evaluated it, taking into account its weight, temperature, and measurements; we then assessed its efficiency, which was found to be 4%. 559 g of dry beets were obtained from seven kilograms of beets. a few dried beets in their entirety. We can infer from these two readings that adding a fan results in a much quicker turnaround time.
The first product I dry in that drier is spinach, and the second is beet. To flip the spinach while the fan wasn’t connected took me five days. Additionally, I was attached to a fan as I turned the beet, and drying took three days.