Introduction:
Waste disposal has become a growing problem in India. The plastic used in sanitary napkins isn’t biodegradable and results in leading accumulation of used napkins in landfills through improper disposal. If these napkins are not disposed of properly it results in blockage of a drainage system and environmental and health danger.
Another problem with these accumulated is that the menstrual blood on the pads stays on them for a longer duration, and it invites lots of bacteria on napkins and emits a bad odor.
The piles of sanitary napkins with large amounts of disease-causing bacteria on them will affect on the health of people who live in the surrounding areas. There is difficulty to spread awareness about these things in regions of villages, and again sanitary pad disposal remains an issue.
Solution for that is installing incinerators in colleges, hostels, etc. Incineration is a waste treatment process that involves the combustion of substances contained in waste materials. Incinerators reduce the solid mass of the original waste by 80–85% and the volume by 95–96%, depending on the composition and degree of recovery of materials.
Date:17/02/2023
I watched LPG based pad incinerator in the ladies’ hostel of Vigyan Ashram. In that incinerator at a time 5 pads can be loaded and burned. This machine is in working condition. A larger capacity incinerator is installed in the Napate Institute which is Pune based educational institute for the use of ladies’ hostel. The problem is that the gas is leaking from the burner’s pipe and unwanted flame at that point is generated which melts that pipe. For that reason, the replacement of this pipe is needed after every month or two months. I saw that burner and dismantled some parts the pipe is made up of aluminum material and the spray nozzle is of copper.
I showed the dismantled burner parts to Arun Dixit sir. Sir said that the problem is a little complicated, it requires brainstorming to solve, so sir gave me another assignment.
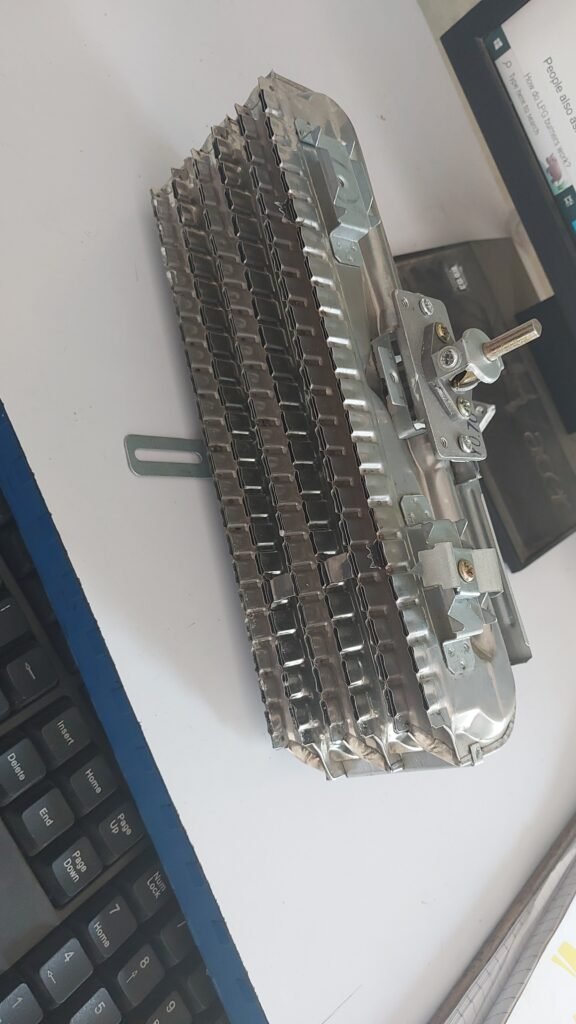
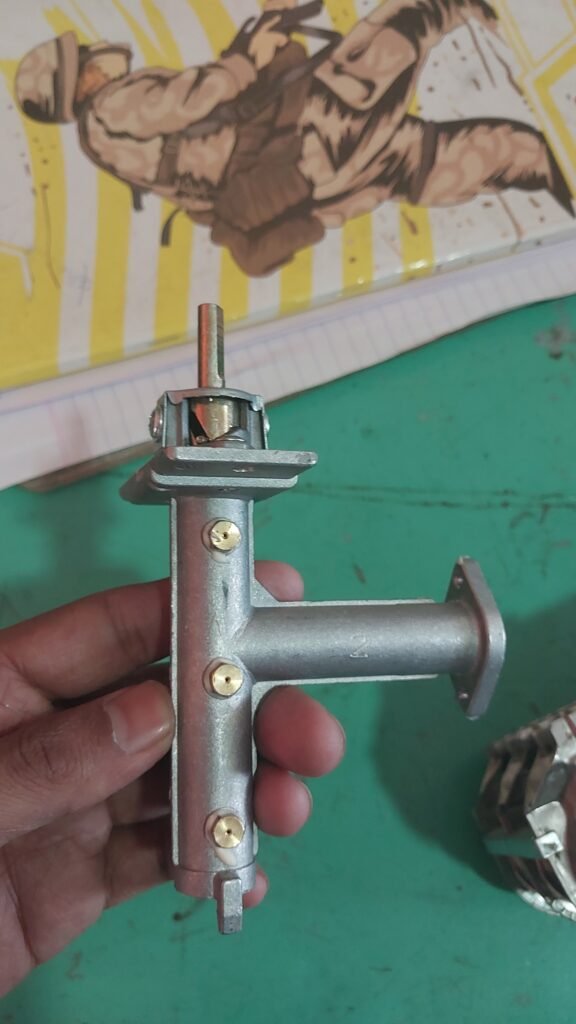
Date: 24/2/2023
For solving the problem of the incinerator Arun Dixit sir arranged one meeting with Purneshwar Shahu, who did the project work of the incinerator and some other members of the Ashram were present.
In this discussion, we mainly focused on the Position of the burner, heat removal from the system, and the material of the burner.
1 Position:
We discussed that the position of the burner will also make a big impact on the problem, In that there are two possibilities for burner position
A). Already existing position of the burner is vertical, so we decided to give some angle to it so heat can flow towards the pad (combustion chamber and flue gases can flow upwards without heating the burner which may occur due to backflow, this will stop the unwanted heating of burner
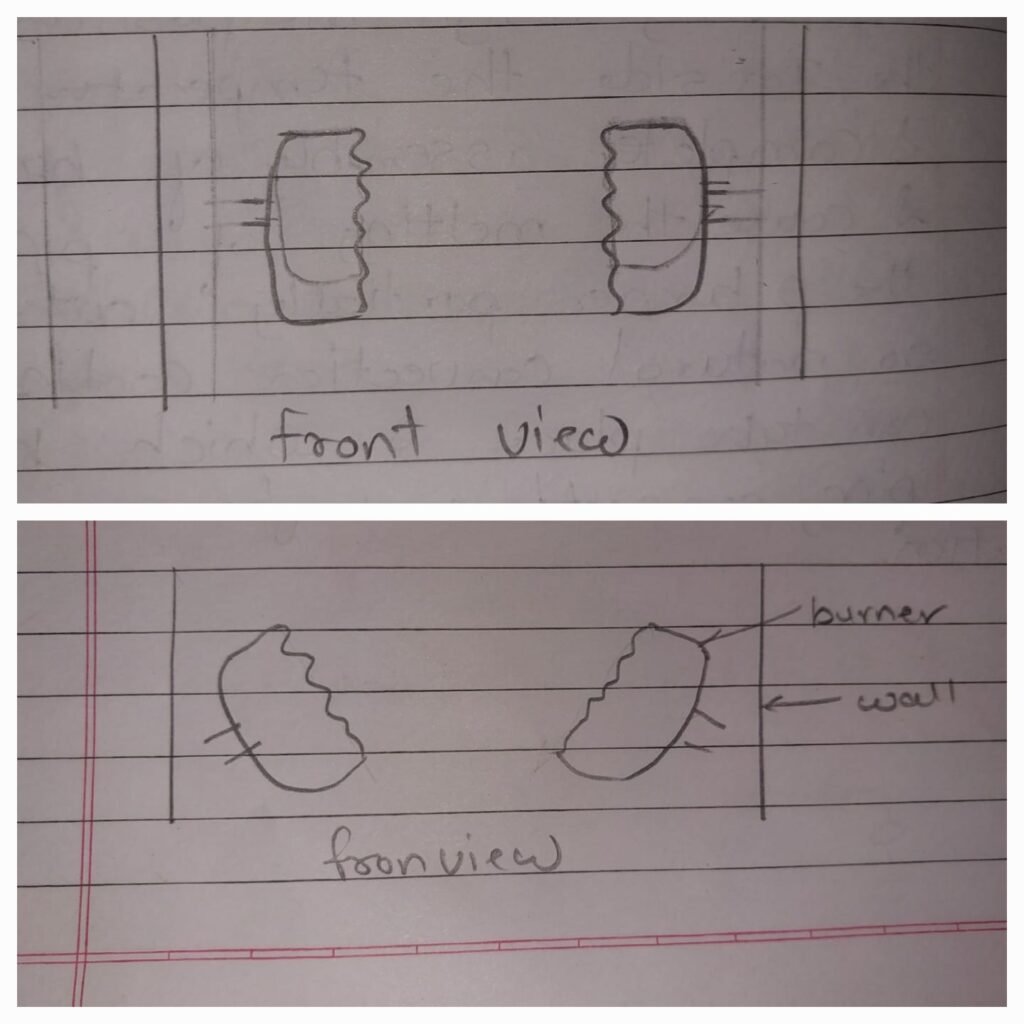
B). In the existing design the burner position is inside the wall, the temperature inside of the wall goes very high thus complete assembly gets heated and causes the melting of the burner’s pipe. We can put the burner partially outside of the wall so natural convection cooling of a burner can take place. This keeps the temperature of all pipe connections of the burner slightly low than the inner temperature.
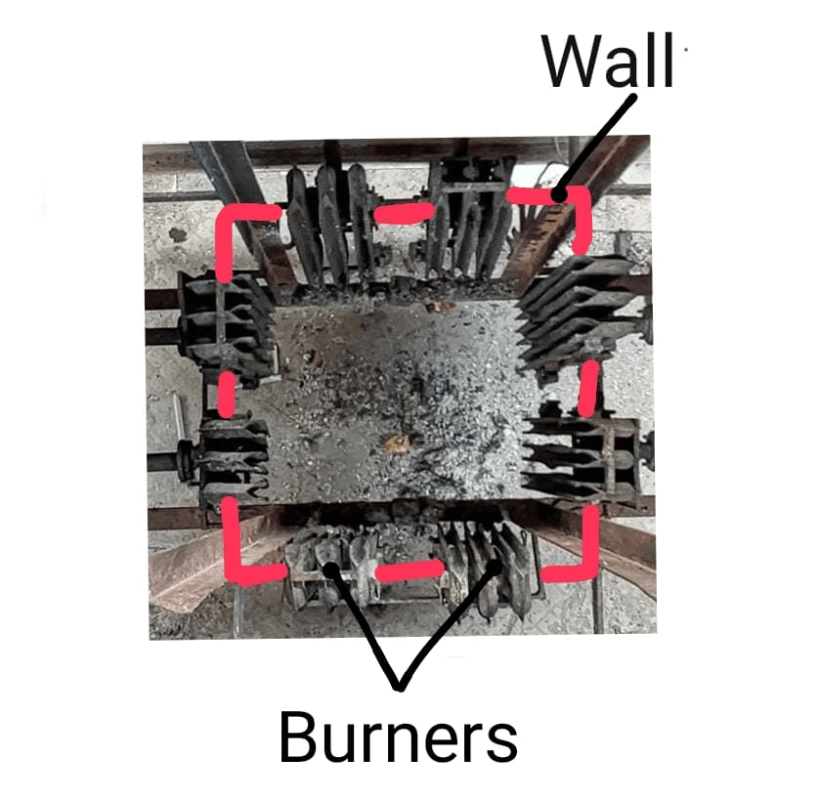
2. Heat removal:
Heat removal means cooling the pip connection of the burner, for we came up with two solutions.
A). Provide copper pipes inside the wall and near the pipe connection where cooling is required. We supply the cold water through the copper pipes which absorb the unwanted heat of the burner. This cools the burner’s connections and stops the melting. This hot water can be collected from the outlet of copper pipes and it can be used for further purposes.
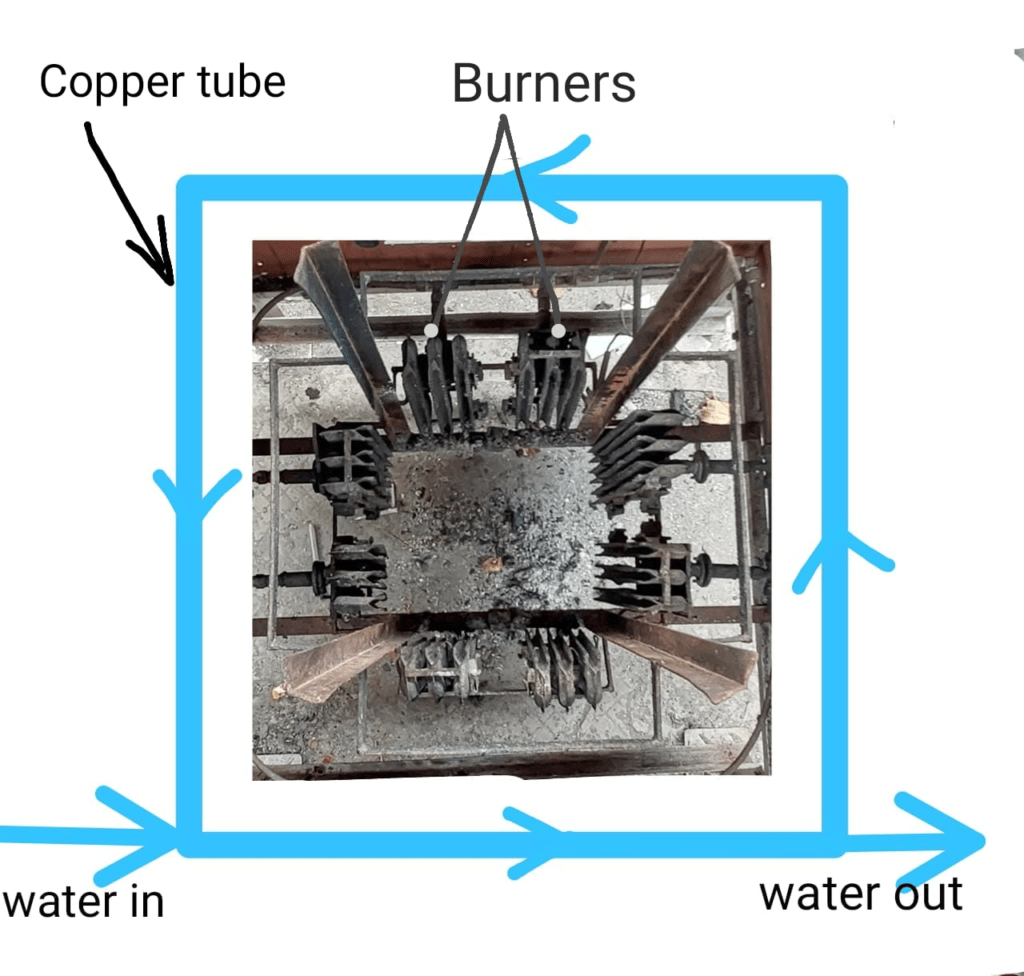
B). Another solution for this heat removal, we can place the burner partially outside as discussed earlier so the burner pipe connection will not come with heat exposure and we can provide another wall that covers all the burners. In between the inner and outer walls, we circulate forced air which will cool the space between both walls.
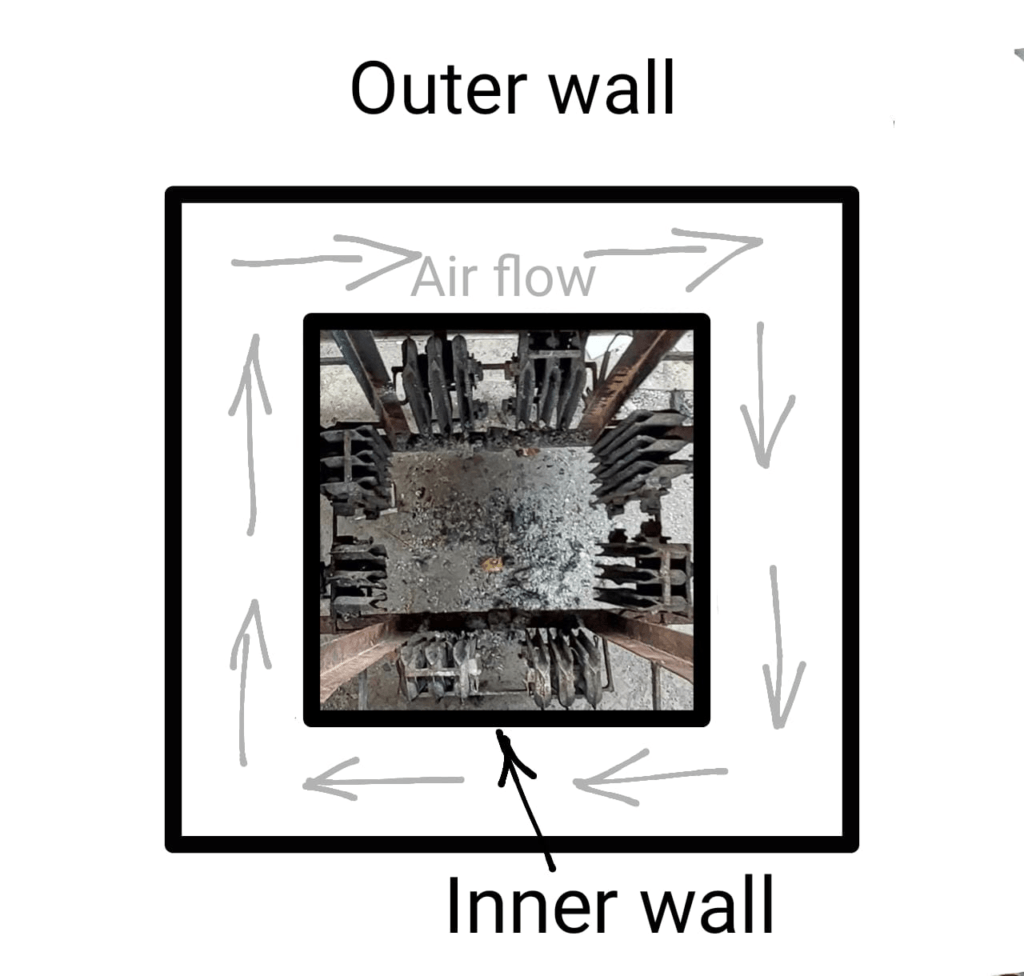
3. Material:
The part where the gas leakage occurs is at flange joint, This leakage generates small flame at flange joint which melts the gasket present inside it. The gasket is used to seal the joint and fill the gaps. we talked about material for the gasket and for sealant.
A). Graphite gasket is a better option because it can withstand higher temperatures without oxidation and pyrolysis.
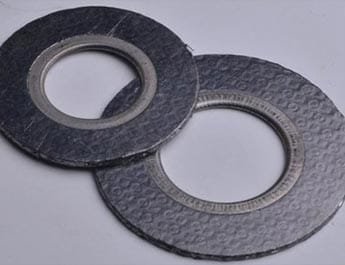
B). After changing the gasket another option is that we can apply Teflon sealant on the flange joint which stops the leakage of gas and stop flame generation.
Date: 12/03/2023
1. Removing two side walls.
Mahesh sir and I visited Napate Institute for taking a trial on the incinerator. Our main purpose is to measure the temperature at various points of an incinerator. For that, we took two trials :
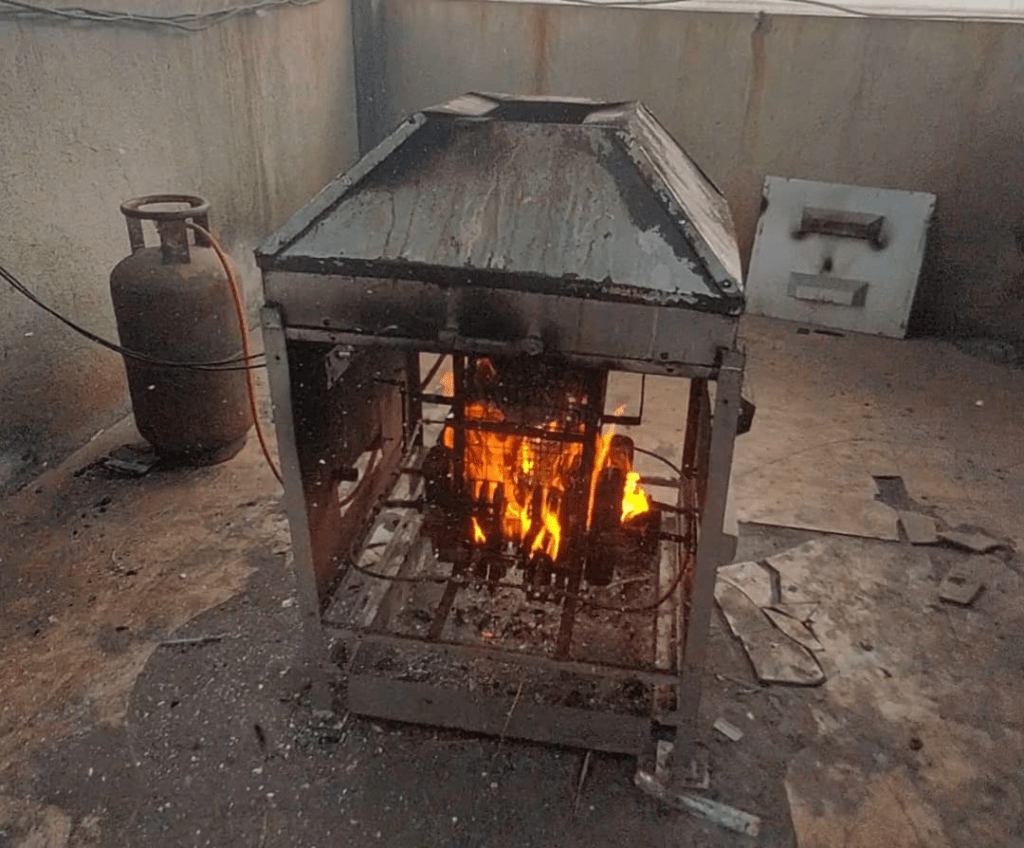
There are four walls at the sides of the machine, we removed two walls by loosening up the nuts and bolts. We kept two walls as it is because on that side control unit is present. We started the machine and ignited the gas flame. After some time we collected the reading of temperature at various points as shown below,
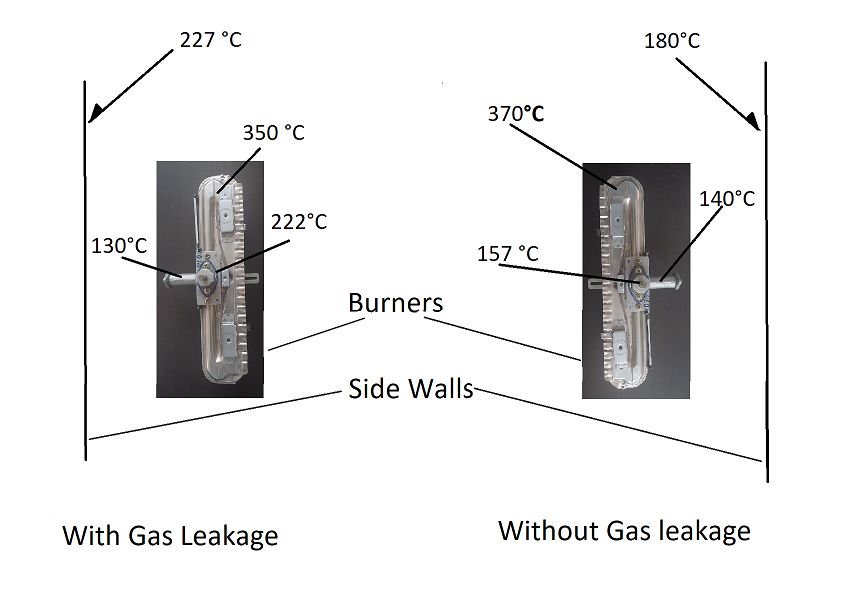
2. Removing the upper lid.
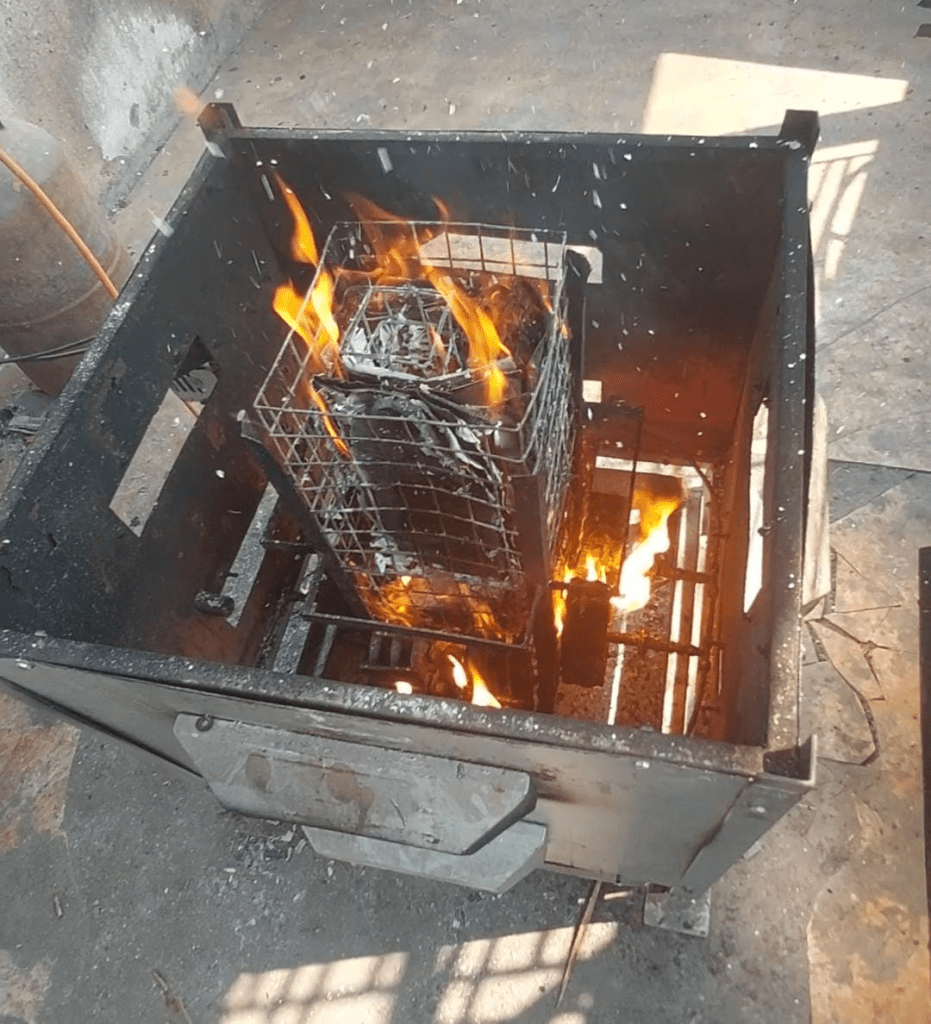
We fitted all four side walls as it is and removed the upper lid. Again we started the machine and ignited the gas flame, after some time we collected the reading of temperature at various points as shown below,
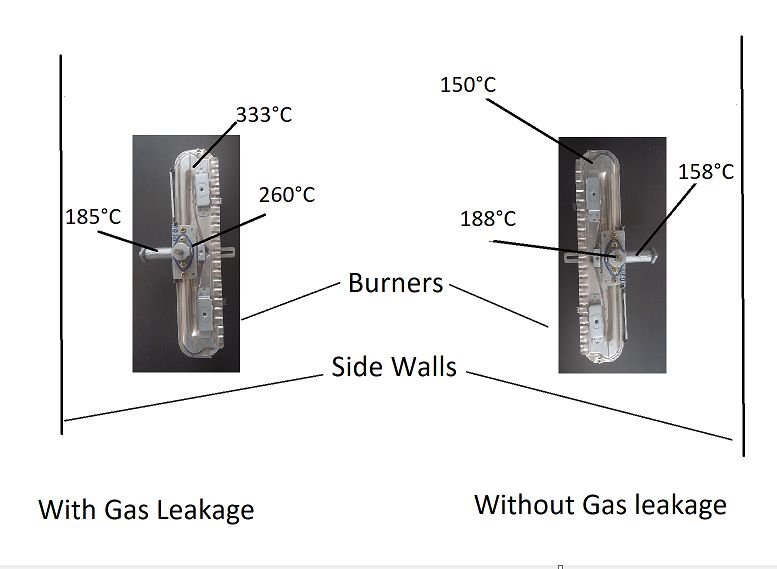
Date:13/03/2023
I have shown all the readings of trials to Dixit sir and did a discussion on that readings. When we compare the temperatures at burners with gas leakage and without gas leakage the difference is not so more, it is nearly the same. Which means we have to reduce the overall temperature of the chamber. So we changed our thinking in that way.
Solutions for reducing the temperature of the chamber:
- Changes in burner
A. Teflon
B. Graphite gasket
2. Providing tubes with water flow
3. Changing side wall with mesh wall: The side wall of the incinerator is of MS sheet with two openings. if we change the side wall with MS perforated sheet, heat circulation is good and it will get enough oxygen from the perforated holes.
4. Providing exhaust fan
Date:14/03/2023
For the above solution how much cost is required for every solution is also needed so I did the online as well as offline survey of all the above.
Sr No | Description | Detail | Cost (In Rs) | Set | Total cost |
1. | Graphite gasket | (max temp-327 °C) | 30/- | 8 | 240/- |
Pipe sealant | 454 gm (max temp-315 °C) | 6453/- | 1 | 6453/- | |
Gasket maker | 85 gm (max temp-250 °C) | 190/- | 1 | 190/- | |
2. | Copper tube | OD=6.3 mm L=7.5 m | 1485/- | 50 | 74250/- |
Copper tube | OD=12.7mm L=1500 cm | 3420/- | 13 | 44460/- | |
3. | SS mesh sheet | 90*100cm | 499/- | 4 | 1996/- |
MS perforated sheet | 121*244 cm | 1800/- | 1 | 1800/- | |
4. | Exhaust fan | 4.75*4.75 “ | 388/- | 1 | 388/- |
Date:16/03/2023
I showed the above table to Dixit sir, as we can see in the table cost of tubing is very high and water cooling is not a must, so we can change Graphite gaskets and side walls with MS perforated sheet which is less expensive.
Date:20/03/2023
In Monday’s review, we again talked about the above solutions. I did again survey of graphite gaskets, in that I found that gaskets are not available in the required size and shape and their availability is less. If we think cutting it in the required shape then it is very difficult because of its hardness. Sealants and gasket makers are available but their melting point is not so high otherwise the cost is more.
So we talked about another material for sealant or gasket. Asbestos is the best material for gaskets, its melting point is between 400 °C to 1040 °C. Its availability is good and can be cut in the required shape. Now I searched about asbestos gasket
I made a final rough BOM to show the rough cost of the redesign to Napate Institute.
LPG-based Pad incinerator Redesign (BOM)
Sr No | Items | Specifications | Qty | Rate | Amount |
1. | MS Punch Mesh | 121*244 cm | 1 | 1800/ piece | 1800/- |
2. | Gasket sheet | 16 | 1500/- | ||
3. | Industrial burner gas geyser | 5 stars 12 inches | 8 | 300/piece | 2400/- |
Total | 5700/- |
I shared a pdf of this table with Bhalerao sir on 22/03/2023.
On 27/03/2023 I sent one official mail to Bhalerao sir and I got a reply from them on 28/03/2023 to proceed with the work.
Date:29/03/2023
Calling vendors for the availability of the Asbestos sheet, Punch sheet for their detailed information.
Date:31/03/2023
I and Sumedh bhaiya went to Pune to buy the parts required. The asbestos sheet available in the shop to who I called is a different asbestos sheet, I needed a metallic asbestos sheet. We asked to some other shops for metallic asbestos sheets. In Excel Trading Corporation we got that sheet 450Rs/m2. This is the image of a metallic asbestos sheet,
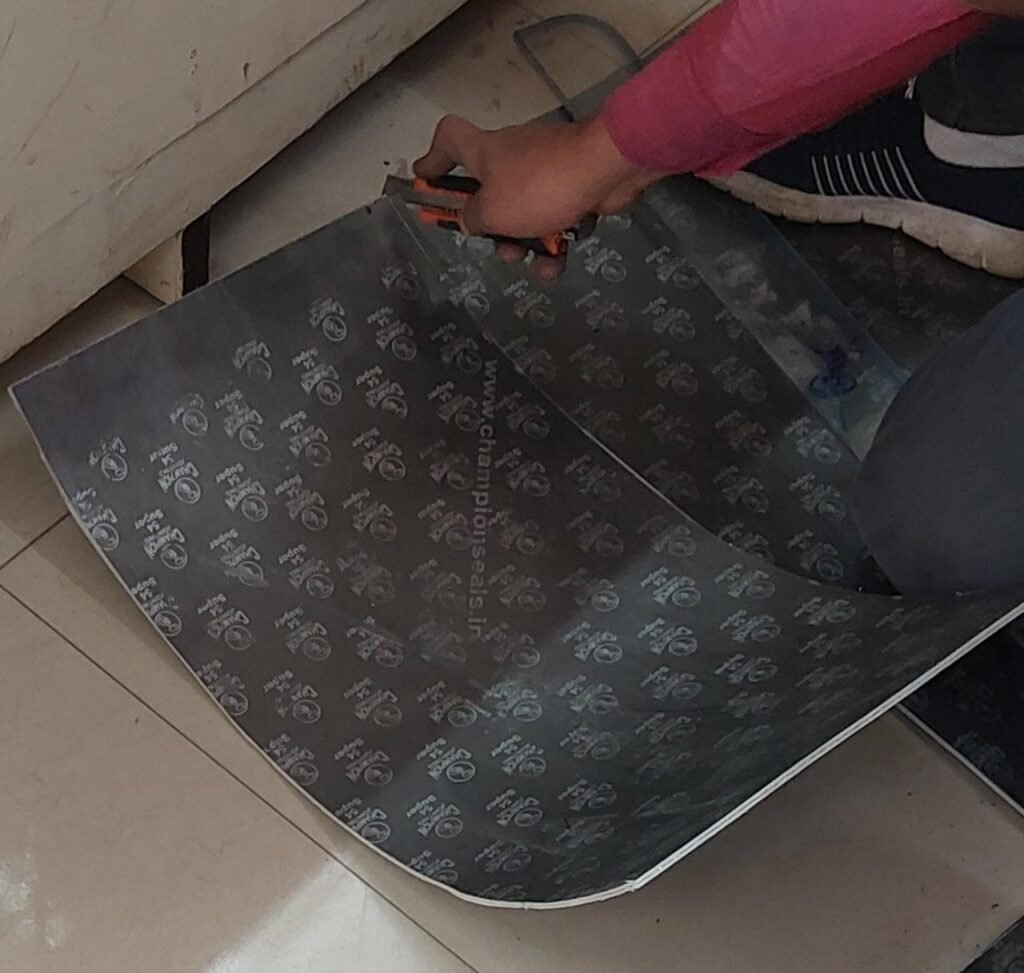
Date:01/04/2023
Now Asbestos sheet is available after that I want to cut that sheet in the required size and shape so, I did the measurement of the required washer size and did the modeling of it. Two washers are needed in each burner like this eight burners are there, two burners at each face. Total we need 16 washers, of that 8 are burner joint washers and 8 are of burner valve washers. The drafted drawing of a washer is shown below.
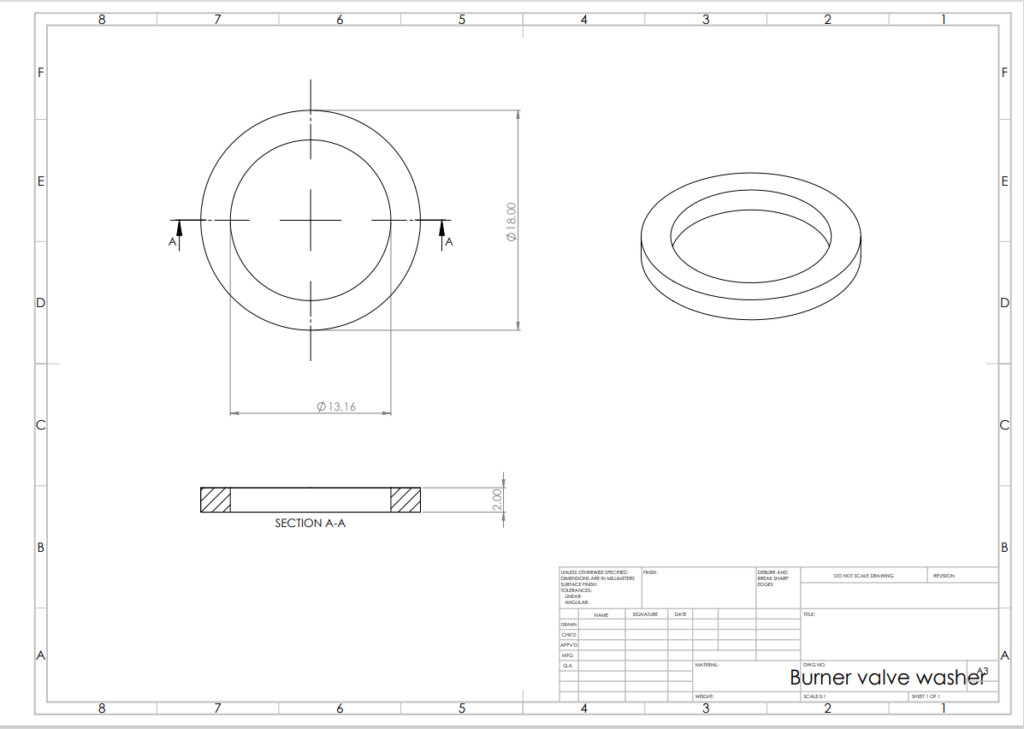
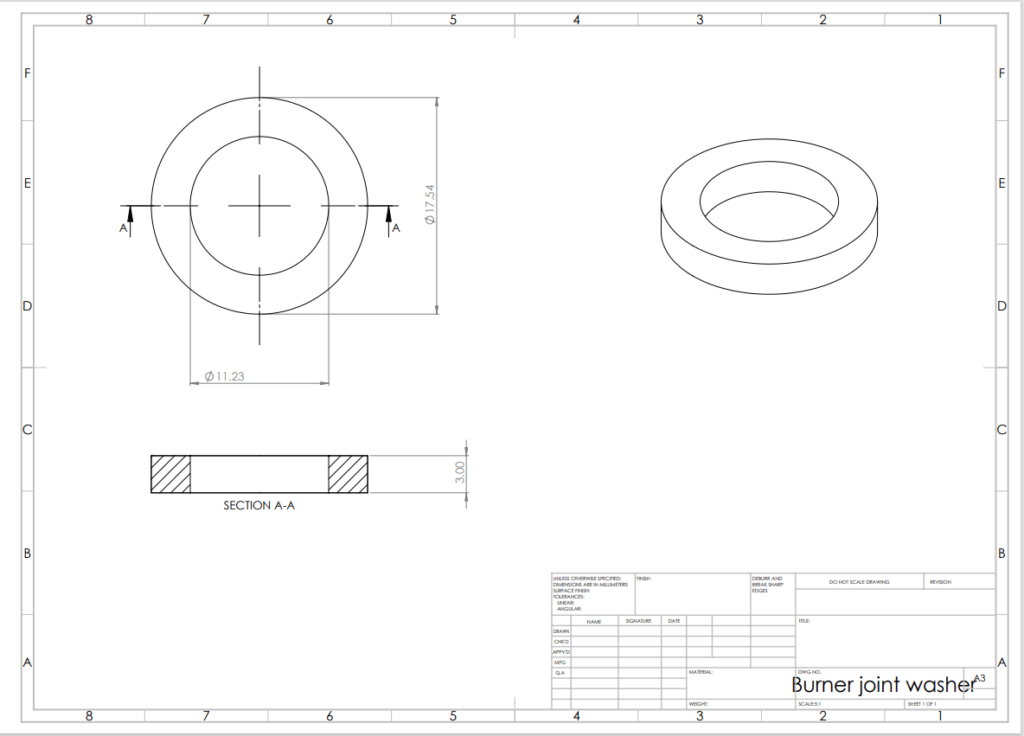
Date:02/04/2023
According to the dimensions me and Mahesh sir tried to cut the washer from a metallic asbestos sheet. first, we tried to cut the outer circle of the washer with the help of a Water tank hole cutter. An outer circle was created but the finishing was not proper and inner hole cutting was also difficult. We tried to drill the hole in that cut circle using a drilling machine. At the time of drilling the cut circle itself revolved along with the drill bit and when we tried to fix it in the jaws, it was folding so, this plan failed.
In the next trial first, we made a hole in the Metallic asbestos sheet with the help of a drilling machine and cut the outer circle using a sheet cutter, for finishing I grinded the outer circle. The washer was made but the circularity of the washer is not getting properly due to human errors and washer will not fit in the joint correctly and leakages may occur in the joints so, this plan was also unsuccessful. This is an image of trials on Metallic asbestos sheets,
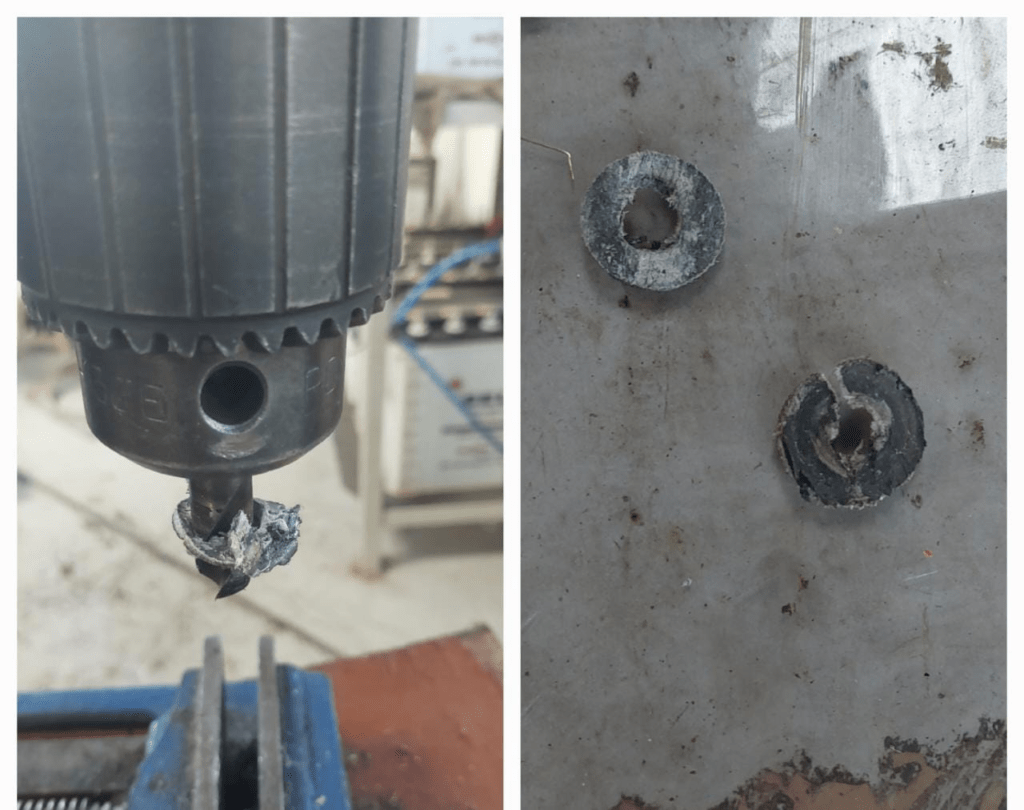
I showed all washer trials to Dixit sir, along with Dixit sir Amey dada was also present and he suggested a new solution to that problem. He said, “Take a bunch of thin copper wires, cover it with multiple layers of Teflon, and make circular washers as you require from that copper and Teflon wire”. Copper is used to create the frame of the washer and it has good malleability and ductility so, it will get deformed and fits perfectly. Teflon covering is used to seal the gaps. The melting point of copper and Teflon is 1085 °C and 327 °C respectively. This is the image of the first washer,
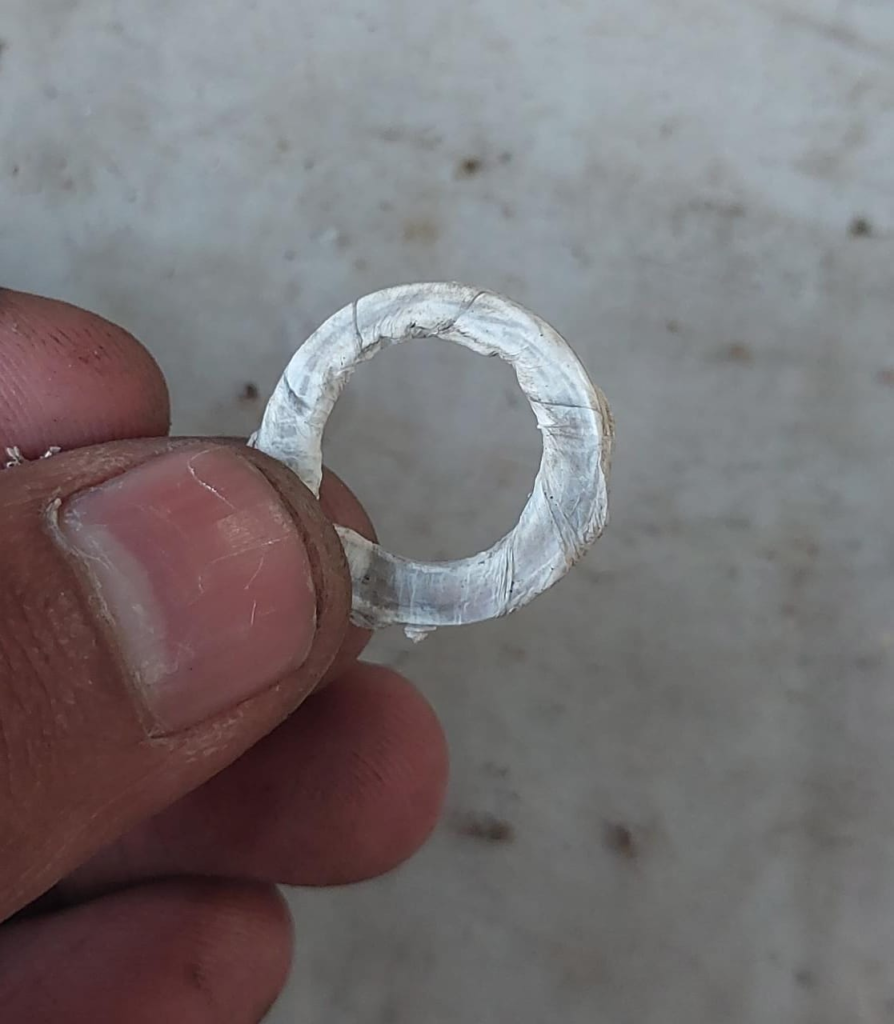
Date: 04/04/2023
Testing of Copper-Teflon washer.
I fitted that new washer in the gas burner and tested it for leakages. For testing, I connected the burner with the compressed air supply of the compressor and inserted the burner in water. There was no bubbling occurring in the water which means the washer is perfectly fitted in the burner without any leakage.
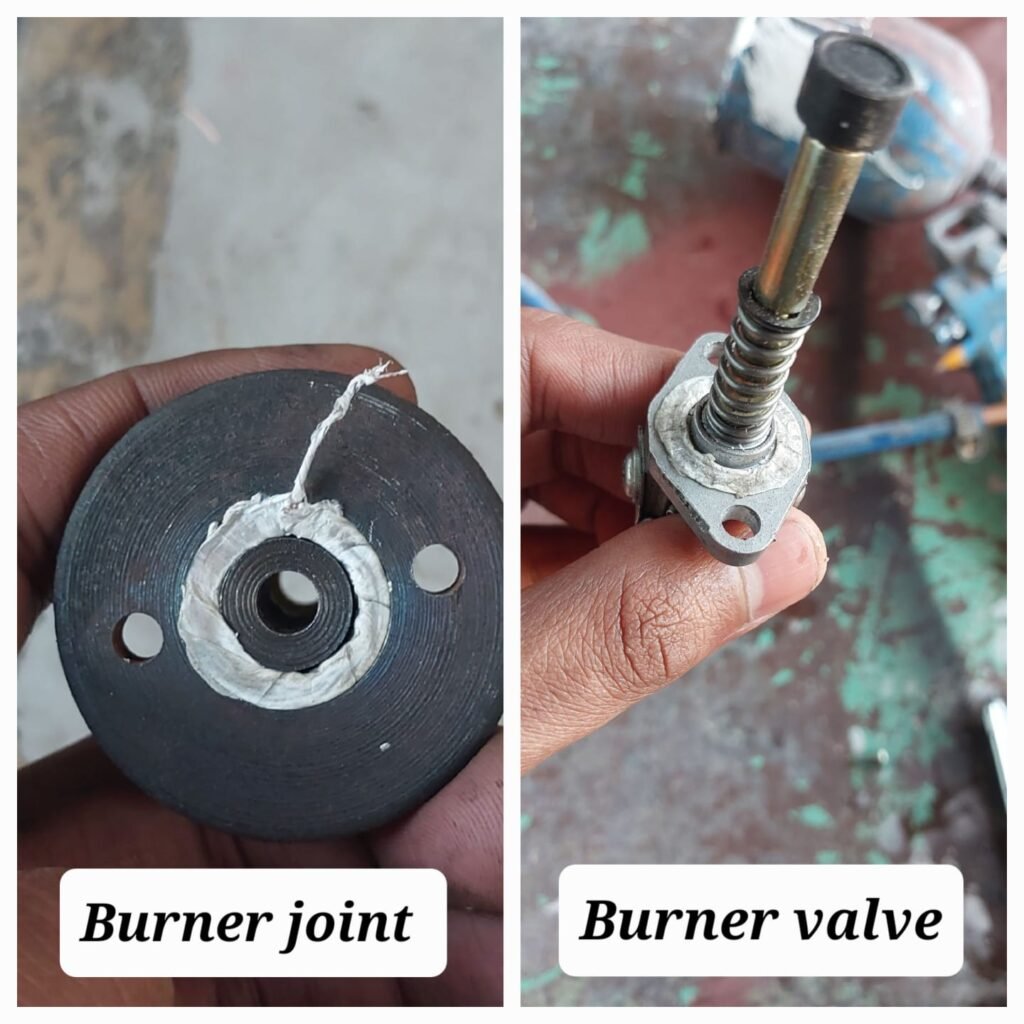

Date:05/04/2023
I made all the washers required for the burners.
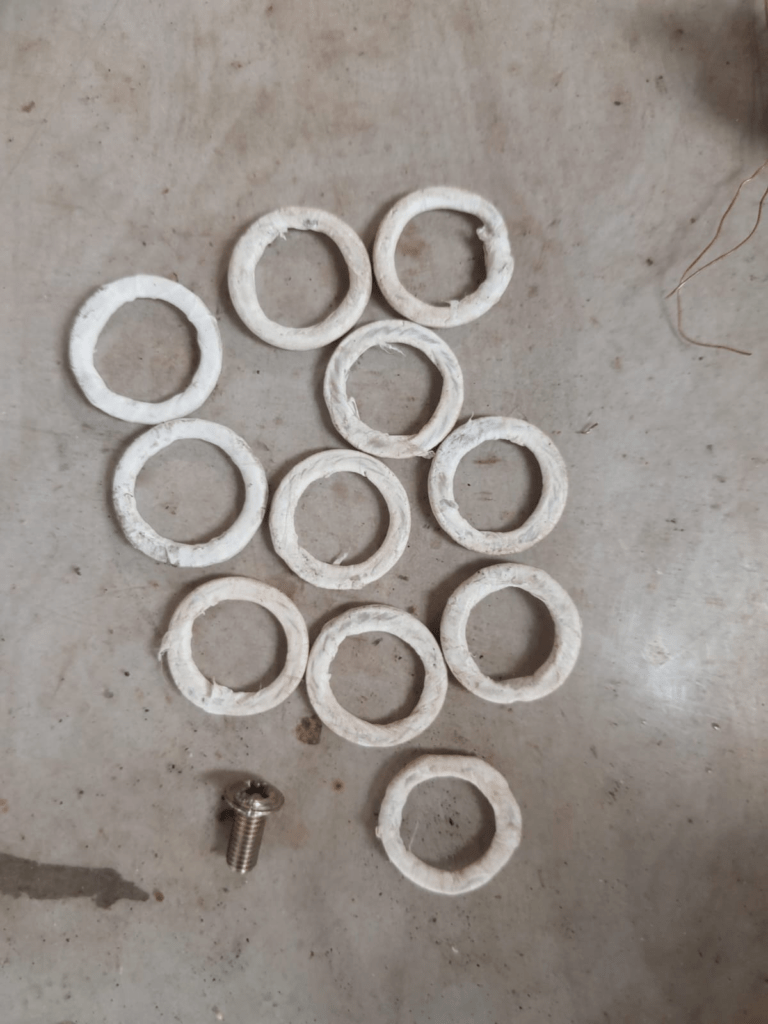
Date: 06/04/2023
I and Ghanshyam Dada brought the MS punch sheet to the Ashram on the Vigyan Ashram’s tractor. I polished the rusted part of the sheet and cut it to the required size with the help of scissor. After that made marking for the hole in which nuts and bolts are fitted and drilled hole using a drilling machine.
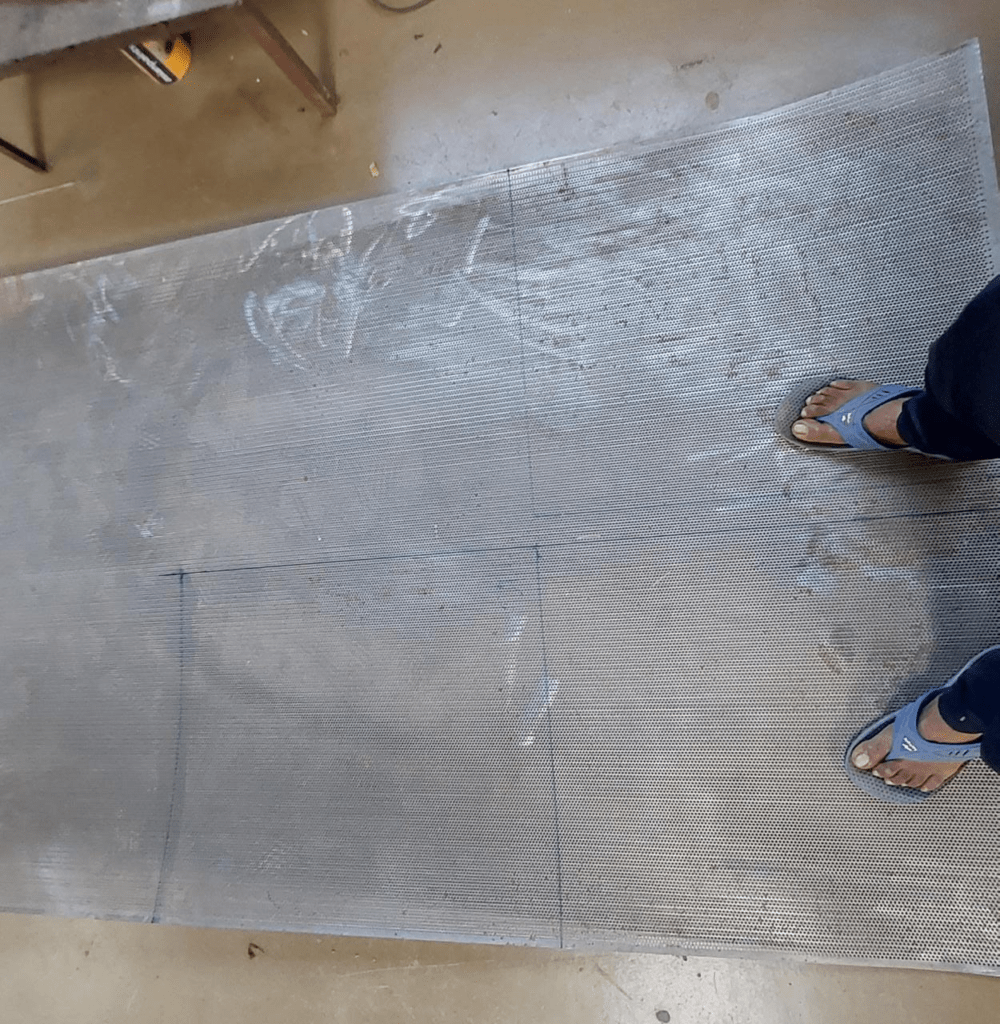
Date: 11/04/2023
I fitted all the washers in burners and tested them. In testing some leakages were present, so I again wound some layers of Teflon on the washer and made it thicker. fitted it in the washer and tightened the burner in the wise jaw. In testing again some bubbles were there.

Date:12/04/2023
The applied pressure was not sufficient and applying further pressure will damage the burner because the burner is made up of aluminum by casting method. Prasad sir suggested that heat the burner after fitting it. Heating the burner causes the Teflon to deform and leakage gets sealed. I used the Hot air gun to heat the burner, after heating tighten the screws so, the deformed Teflon gets fitted. Now the joint was fully sealed. I followed the same procedure for all burners.
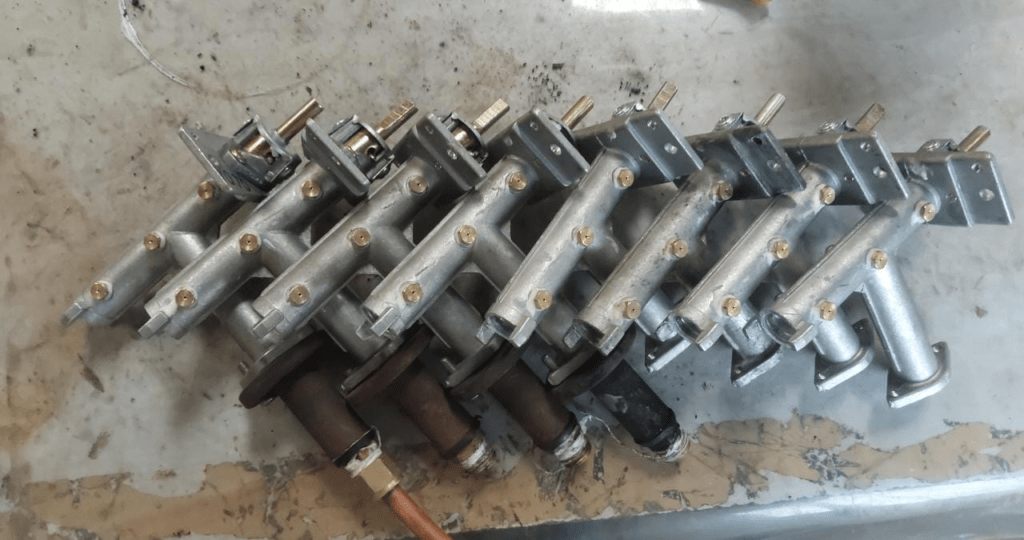
Date:13/04/2023
Mahesh sir, Ghanshyam dada, and I went to Napate Institute with the required part and tools to change the parts of the Incinerator. We replaced all required parts like burners, and punch mesh sheets. We took two trials on the incinerator after doing modification and tested the burner for leakage by applying soap solution.
After the trial, we had two to three calls with Napate Institute for asking them, was there any issue with Incinerator? They replied it is working well, and if any problem arises they will inform us.