Introduction
Water is one of the essential commodities required by the human kind. Water can be obtained from various sources like groundwater: found in the ground water beds that have been filtered with soil and rocks; Surface water: artificial/ natural reservoirs, lakes, etc generally origin of rivers in the highlands; Flowing water: water obtained from rivers and canals that flow from the highlands to the oceans and seas; Artificially harvested water by technologies like atmospheric water generation, rainwater harvesting, desalination, etc. Not all the water received from these sources is potable and needs purification based on the use of the water. To purify the water, contaminants like suspended solids, organic and inorganic materials, micro-organisms, etc must be removed. Various methods are used to purify the water. Common types processes used to treat water is sedimentation, sand filtration, ultra-filtration, reverse-osmosis, chemical/UV disinfection.
Objectives
- To convert the continuous UV filtration method to batch filtration.
- To automate and optimize the complete process
- To provide micro-organism free water
Project description
The two most common methods of disinfecting the water from micro-organisms like bacteria is by chemical or Ultraviolet(UV) disinfection. UV light is the best to kill bacteria as it is environment friendly, chemical-free, affordable, rapid and not only acts on bacteria but also molds, fungi and a few viruses. The UV light is a electromagnetic wave present in the range 100-400 nm. It can be further divided into UV-A (315-400 nm), UV-B (280-315 nm) and UV-C (100-280 nm) . Out of the three UV-C is considered best for killing micro-organisms. The reason the UV light kills the micro-organisms is because it damages the DNA/RNA by causing a photo-chemical reaction in thymine/cystine (DNA) and uracil (RNA) dimers. The change in the genetic material lead to mutation and finally results into the death of the cells. Using this principle a automated system for purification of water was developed in continuation of the previous efforts at Vigyan Ashram . This system will disinfect the water by ultraviolet light in a batch process as opposed to the traditional continuous method. The water is filtered in batches in a small container and then added to a large container for storage. The system uses float switches to automatically cut-off the the water supply to the containers. The following flowchart best explains the working of the system.
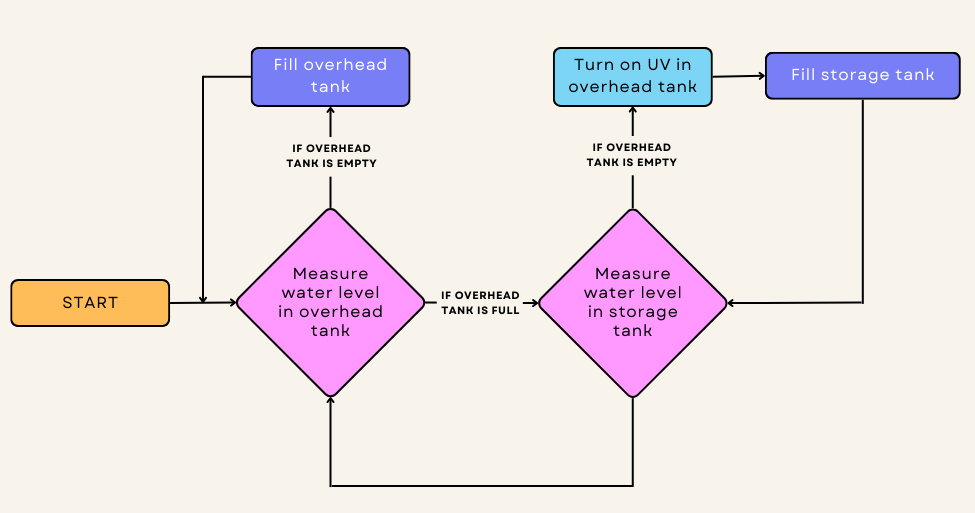
Development of the project
The whole system works on an Arduino UNO microcontroller. The Arduino UNO is connected to 2 float sensors and a multichannel relay. The relay regulates flow of AC supply to 2 motors and 1 UV tube. The float sensors avoid overflow of water from the tanks. The relay receives signal based on the float sensors activate or deactivate the motors that fill each of the two tanks along with the UV tube that disinfects the water in the overhead tank for 10 minutes. The electronic system is housed in a laser cut casing made out of MDF and acrylic sheets. In order to design the solution, a stainless steel vessel was used as an overhead tank. which would get water from the source and store for disinfection in a batch process. Initially solenoid valves we attached to these vessels in order to control the water flow. The solenoid valve required pressure to operate and took 25-30 minutes to empty the vessel completely. To increase the speed a submersible motor was tested. The motor would act as a storage for bacteria if submerged in the water and UV would not be very effective. This motor was unable to pull water to a height so it was connected to the end of solenoid valve in order to pull the water from the solenoid by increase the pressure on the solenoid valve. This arrangement reduced to time to empty the vessel to 14 minutes. This arrangement consumed more power due to two devices being utilized simultaneously. To solve the above problems, a non-submersible pump was tested. This pump could pull water up to 2 meters and push the water up to 3 meters. The pump was connected on top of the overhead vessel. This pump was able to empty the vessel in 8-10 minutes. This pump was chosen for he final design with white pipes instead of transparent pipes to avoid fungal growth due to sunlight. The system was deployed and water was tested.
Improvements required
- The system needs to be more compact and easy to install
- The electronic component should be made on a PCB
- Optimization of the time for disinfection.
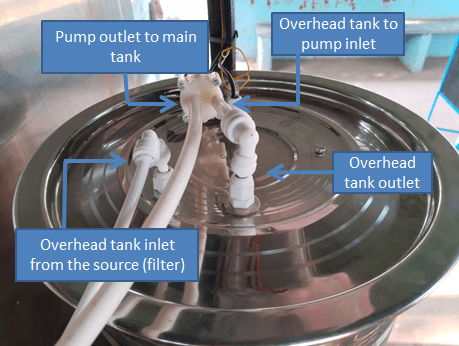
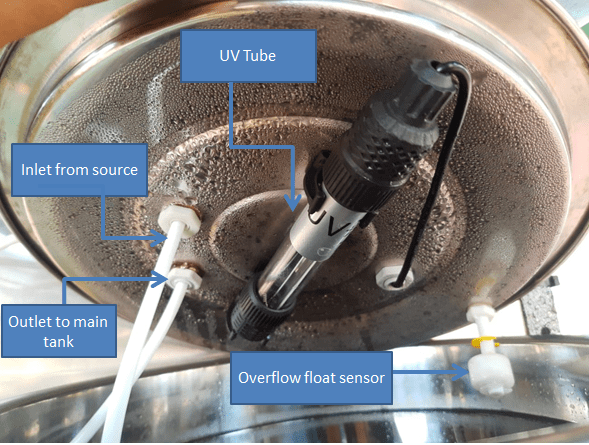
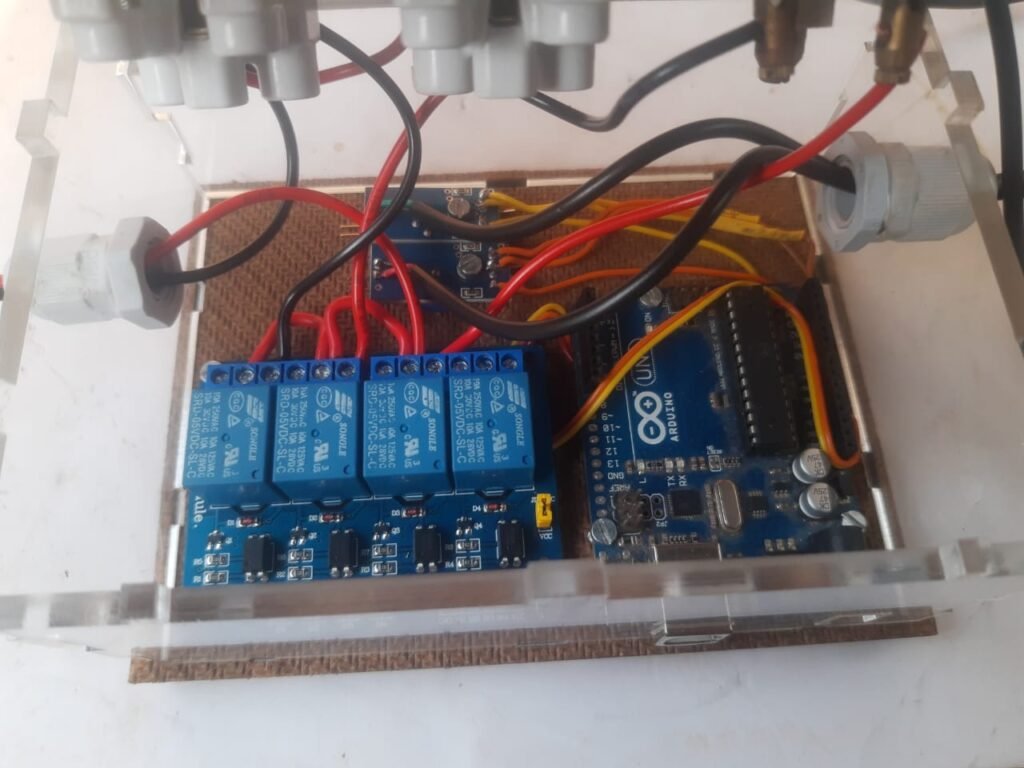
Code
int motor = 2;
int UV = 3;
int solenoid = 4;
int f1 = A1;
int f2 = A0;
int lvl1 =1;
int lvl2 =1;
int count = 0;
bool activate = LOW;
bool deactivate = HIGH;
void setup()
{
pinMode(motor, OUTPUT);
pinMode(UV, OUTPUT);
pinMode(solenoid, OUTPUT);
digitalWrite(motor, deactivate);
digitalWrite(solenoid, deactivate);
digitalWrite(UV, activate);
delay(1000);
digitalWrite(UV, deactivate);
Serial.begin(9600);
}
void loop()
{
lvl1 = digitalRead(f1);
lvl2 = digitalRead(f2);
delay(1000);
if(lvl2 == 0)
{
//Fill the over head tank
overhead();
//sterilize water
sterilize();
while(count<3)
{
if(lvl2 == 0)
{
digitalWrite(solenoid, activate);
delay(120000);
digitalWrite(solenoid, deactivate);
lvl2 = digitalRead(f2);
delay(500);
}
count++;
}
count = 0;
}
}
void overhead()
{
Serial.println(lvl1);
digitalWrite(solenoid, deactivate);
while(lvl1 == 0)
{
digitalWrite(motor, activate);
lvl1 = digitalRead(f1);
}
digitalWrite(motor, deactivate);
}
void sterilize()
{
digitalWrite(UV, activate);
delay(600000);
digitalWrite(UV, deactivate);
delay(1000);
}