Objective: To functionalize the COD apparatus present in the Soil Lab
The COD apparatus has some issues with the electric controls and the tube holding plates. Tube holding plates are made up of MS sheet over which FRP coating has done, the holes cut on plasma cutter, as plasma do not have precise operation those holes are not properly done, they are varying in size so the COD apparatus user could not use the machine because the safety issue as the acid inside the tube can come out while loading it. So the machine is not in operation.
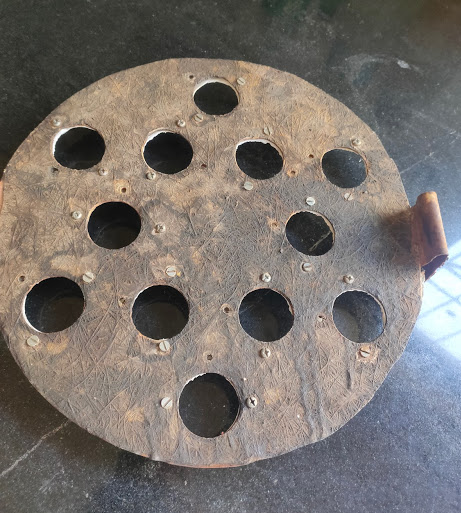
Apart from this it has one guide plate which symmetrical to the holding plate for long length tubes, but its alignment is not accurate. So both these two plate need tp be fabricated as single unit, by giving long threaded bolt support.
Design of holding plate: 25/04/2021
The above design are so designed that it will become a single unit when nut bolted with each other, so the it will provide correct alignment.
The above design was cut on laser cutter, laser cutter has very good precision so the tube is accurately fits in the given hole without any difficulty. now the problem is Laser cutter cannot cut the MS and FRP material and plasma cutter is not accurate. So for precise operation we need to cut these designs on precise plasma cutter, so we need to outsource it for cutting operation.
laser cutting New design cut on MDF material on Laser cutter 26/04/2021
In the above picture we can see that, All the tube holders are so accurate in its dimensions and the sample tube can easily we mounted and taken out without any friction and difficulty. Therefore, to obtain the accurate dimensions we need to fabricate it on high precision cutting machine.
Cutting on plasma
Upper mounting plate lower mounting plate hole on plates
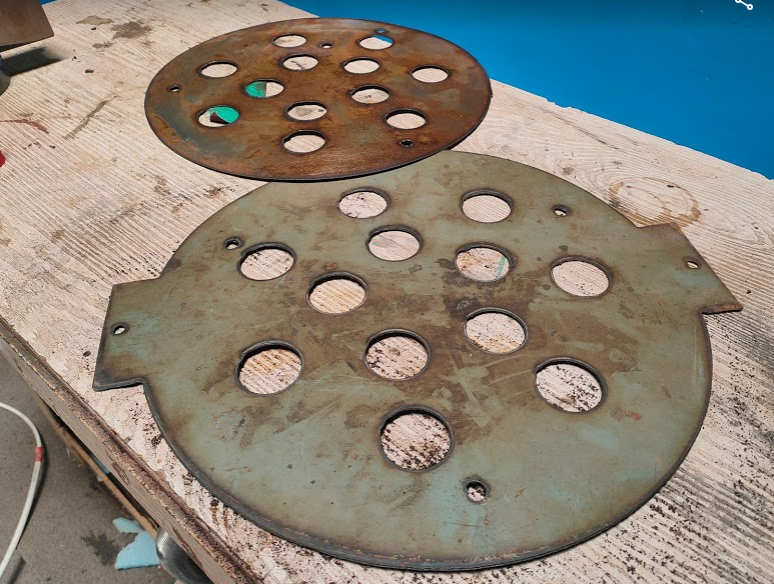
The electrical connections was very disturbed due improper wiring connections. Some connections were loosely tight it can cause short circuit. Also the panel box was of GI material, which is highly conductive. So that need to replaced by any of the non conductive material. Therefore before removing the connections from the circuit, all the wires were labeled by its unique codes so as to easily identify the connections in future scope, otherwise we may waste our time in finding the connections in circuit diagram.
Cable glands on each wire for identification
Design of panel box done on Solidworks.
Panel box cutting on Laser cutter DXF generation 3D box design
Modified panel box old panel box
In the below picture we can see the black colored tube mounting plates are so designed that they easily fits on the surface of oil container. But as its height is too high so the amount of oil required is more. so to overcome this problem we redesigned the dimensions of the plates and it is so adjusted that it could be inserted inside the container without disturbing the system.
Now, we can see the other picture in which the mounting plate is inside of the container and therefore we require less amount of oil.
Previous design in which tube mounting plate is over the surface mounting plate inside the container
Old COD app Modified COD App
The system was tasted on water with PID controller’s temperature control function. Temperature was set to 95°C for water. Then the system allowed to heat the water inside. Once the temperature raised upto 95°C the PID started its operation and it triggered off the relay. Then this ON-OFF triggering continued to maintain the temperature at 95°C. The same process done on several different temperatures ( 75,80,85°C) and the results was satisfactory with error of 4°C.
After the successful trials on water, COD apparatus handed over to Soil Lab for lab testing.
To calibrate COD apparatus we pour vegetable ghee in it and set the temperature to 150. but we could not get the temperature accurate, from several observations we came to know that, Temperature sensor position plays an important role in maintaining the temperature evenly inside the container. so we put the sensor middle level of the oil, so that we get the right temperature readings on PID.
Feedback from Soil Lab Team:
COD apparatus helping us to test 12 samples at a time now. So we don’t need to wait and use 4 sample COD apparatus when we have to measure more than 4 samples. the electrical connections and electronics are working automatically as per set in the PID controller.