Design and Development of Sheet Metal Box
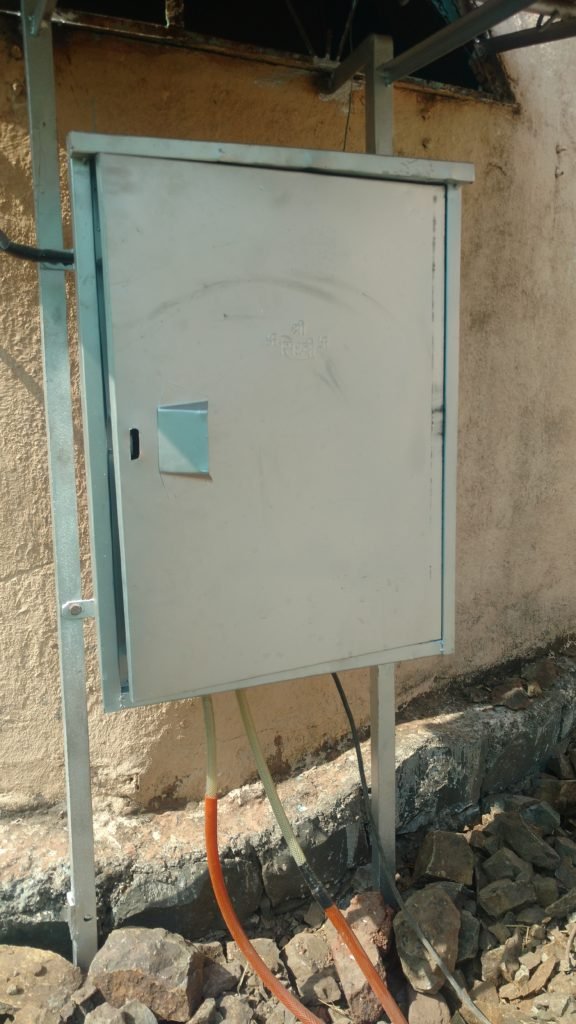
- The first parameter required in the manufacturing of any product is its dimensions. So we measured the dimensions of the box.
- Next step in manufacturing is to draw a rough drawing of the product to be prepared. So we drew a rough drawing of sheet metal box.
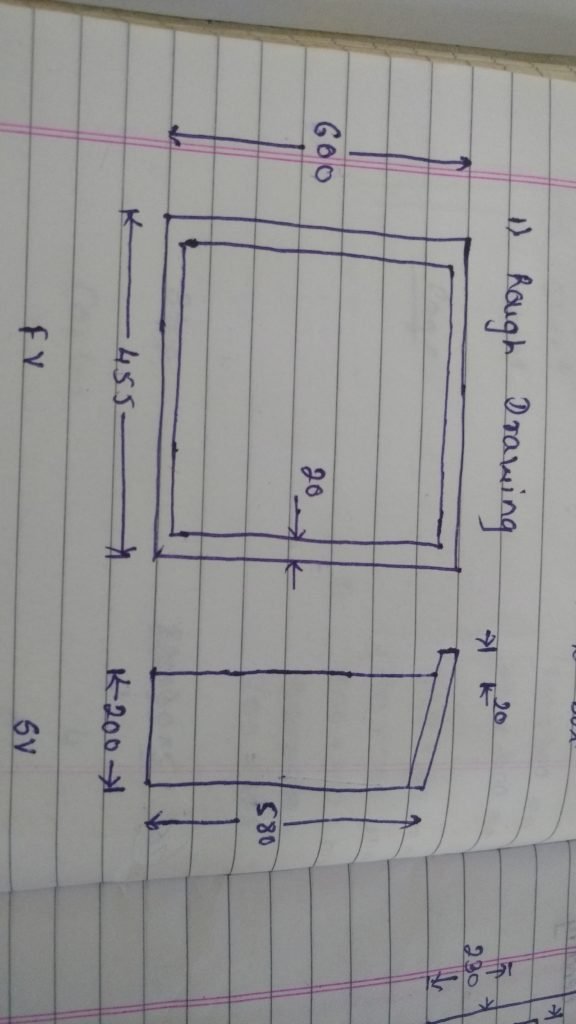
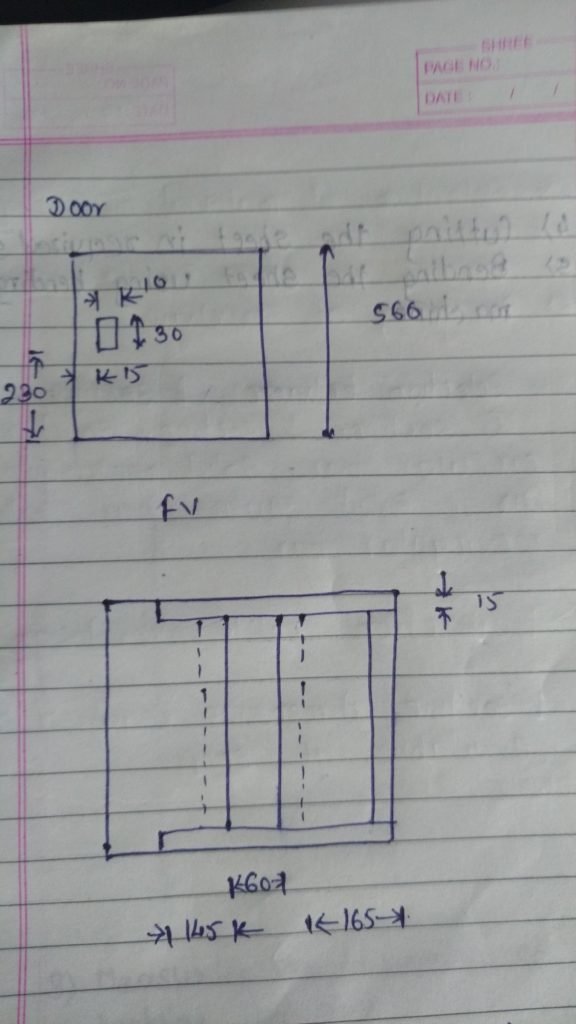
3. After rough drawing, we did the 3-dimensional modeling of sheet metal box to be manufactured using SolidWorks software.
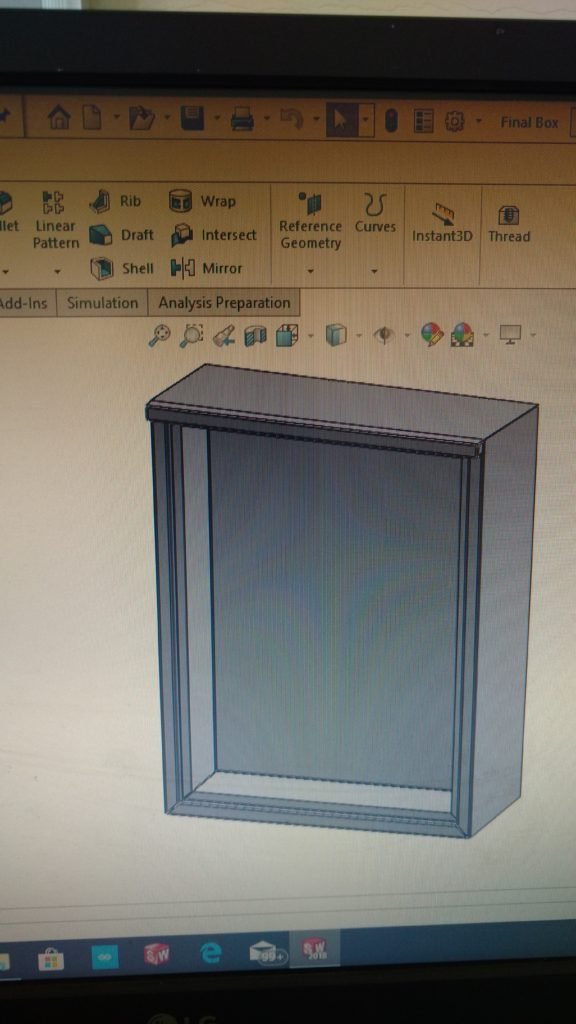
4. In next step we calculated the total area of the sheet required to manufacture the box. We decided to do FRP coating to the box and calculated the cost required to do FRP coating.
5. To cut the sheet in required shape we used plasma cutter. To use plasma cutter for cutting we required G & M codes.
6. By using fastcam software we converted 2 dimensional sketch in G & M codes.
7. Then by using plasma cutter we cut the sheet in required shape
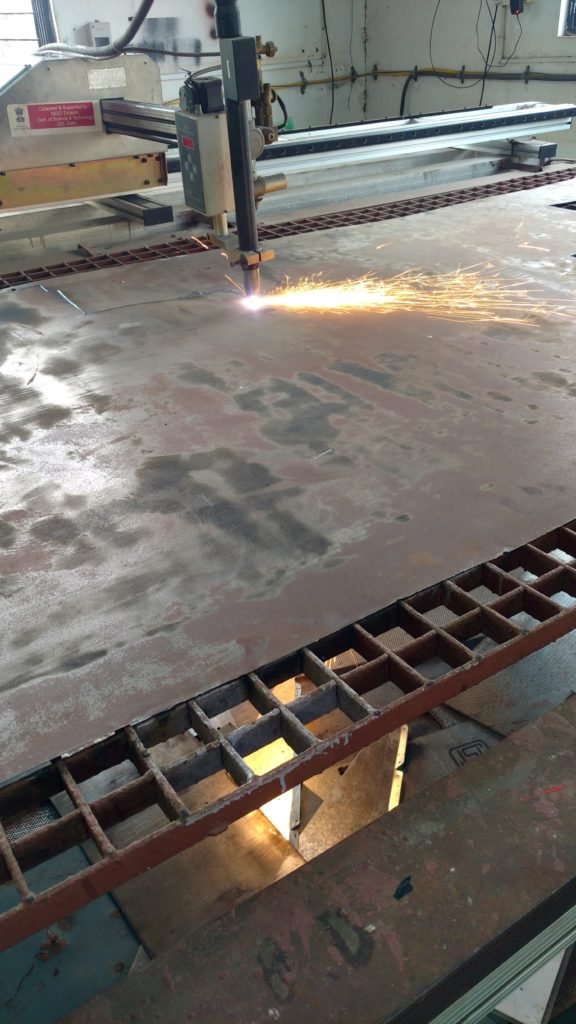
8. Using manual bending machine bending in required shape is done.
Design and Development of Welding Machine Cage
- First step we did was to search for available models of weld machine cage on the internet.
- Then we drew the rough drawing of the model.
- Then we measured the dimensions of the welding machine(LxWxH= 160x380x300).
- Then we searched for the dimensions of argon cylinder on the internet we have to put in welding machine cage.
- We selected argon cylinder of medium size(E2) and the dimensions of it are Diameter x Height x Weight= 204 mm x 780 mm x 24.5 kg.
- Then we selected material on strength basis i.e Mild Steel.
- We selected L angle for the structure because it will be sufficient enough to give the required strength.
- If we have selected c section, i section, solid circular bar, solid rectangular bar or hollow rectangular bar we would have overdesigned.
- Then we did the bill of material required for weld machine cage.
- After that, we were short on material, so we brought the material from the shop.
- Then we did the cutting of L angle in required dimensions.
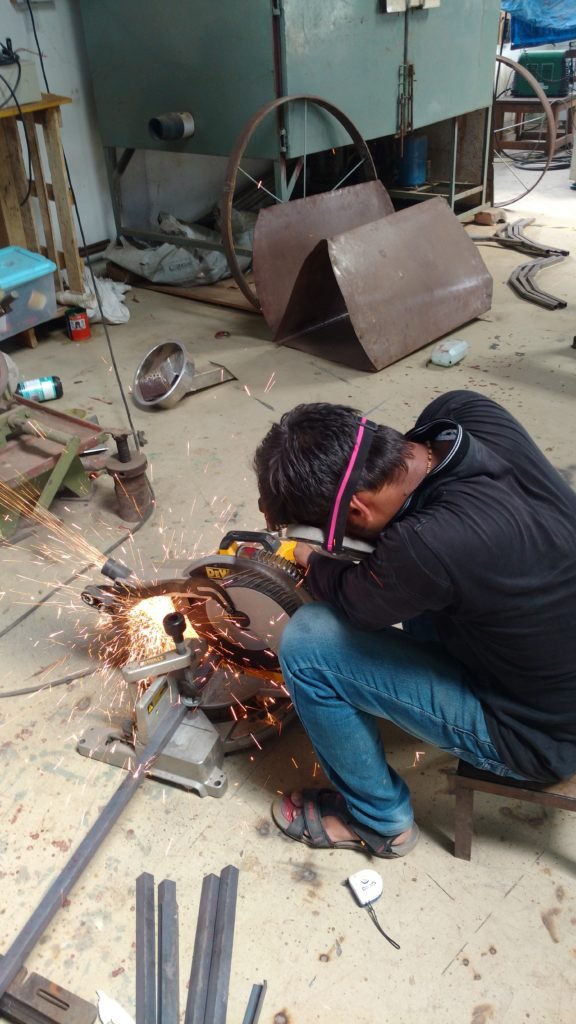
12. After that we did the spot welding of L angles to form the structure.
13. Then we did the full welding of structure to form strong welds.
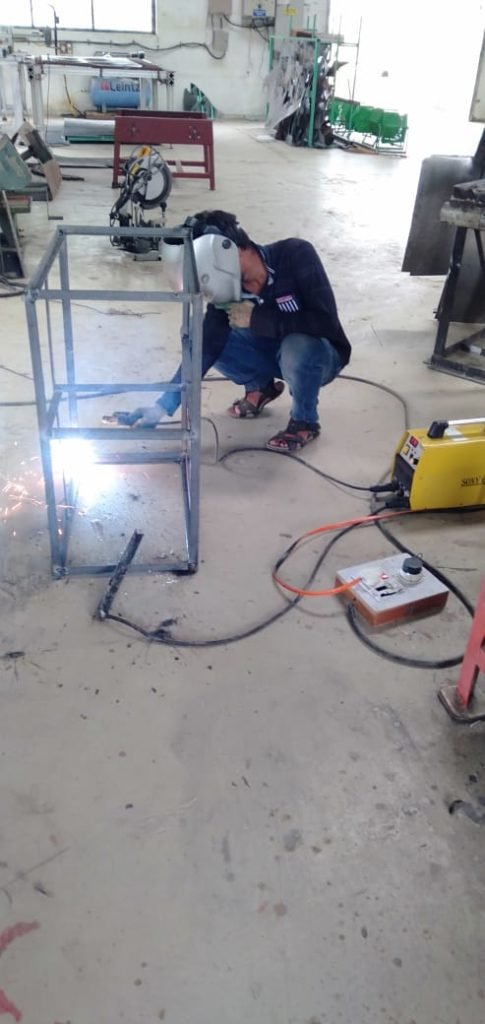
14. After full welding we took the dimensions of doors and other sheets required.
15. Then the required sheet was cut on plasma cutter.
16. Then we attached the sheet at bottom by using riveting.
17. Then we did the CAM of door and converted it into CNC codes by using fastcam software.
18. After cutting and bending on sheet bender, the doors are bolted to cage.
19. Punched mesh of required size and shape was cut on plasma cutter and riveted to cage.
20. Caster wheels are welded at the bottom of cage.
21. By using pipe of diameter 30 mm handle was made and bolted to the cage.