A polyhouse is a controlled environment designed to optimize plant growth and crop production. It utilizes materials like metal or bamboo frames and polyethylene covers to protect crops from adverse weather and pests. Different types of polyhouses exist, categorized by environmental control (naturally ventilated or environmentally controlled), shape (lean-to, even span, or gothic arch), and cost and suitability (low-cost, medium-cost, or high-cost). Key components include the structure (foundation, frame, cover, ventilation), environmental control systems (heating, cooling, irrigation), and other features like benches, shading nets, and insect nets. Polyhouses find applications in agriculture, horticulture, floriculture, research, and education. Benefits include increased crop yield, extended growing seasons, and improved crop quality. However, there are also drawbacks such as high initial investment, technical expertise requirements, and potential environmental impact. Automation plays a crucial role in polyhouse management by optimizing growing conditions, conserving resources, and reducing labor. Careful site selection, design considerations, and appropriate crop selection are essential for successful polyhouse construction.
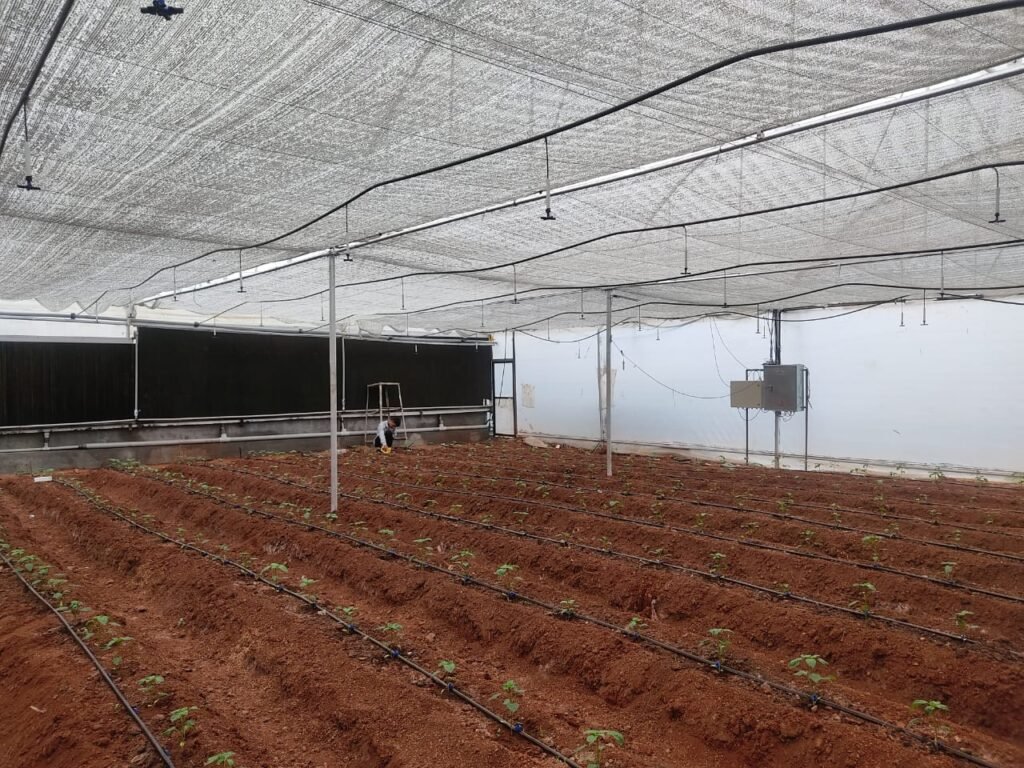
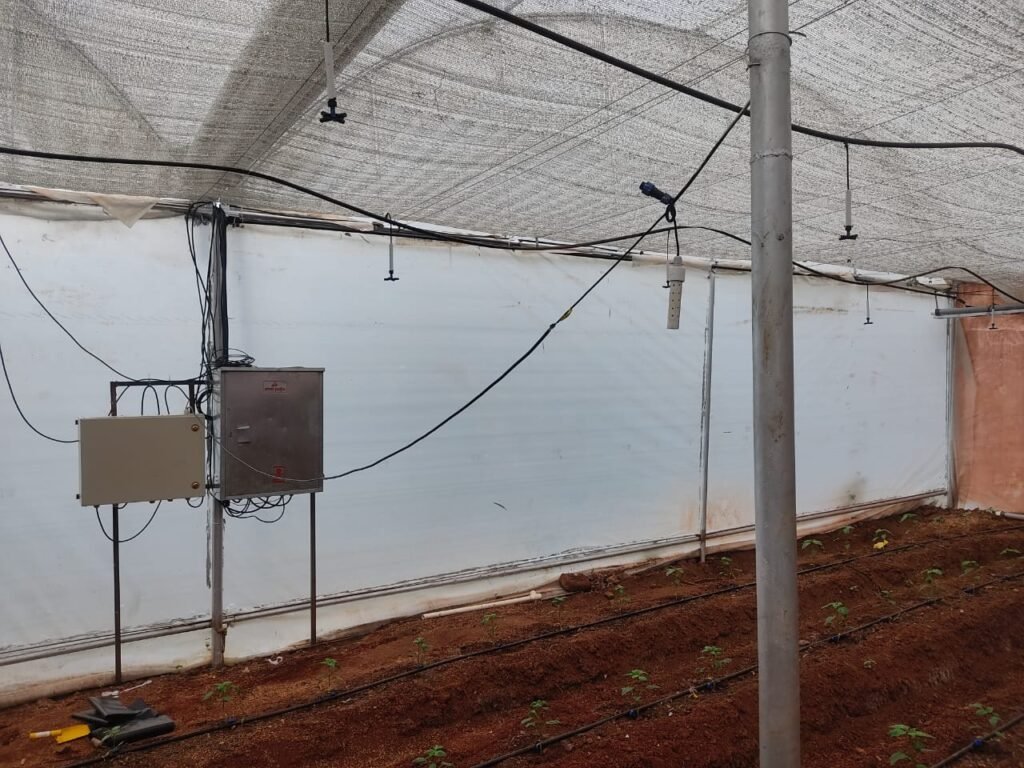
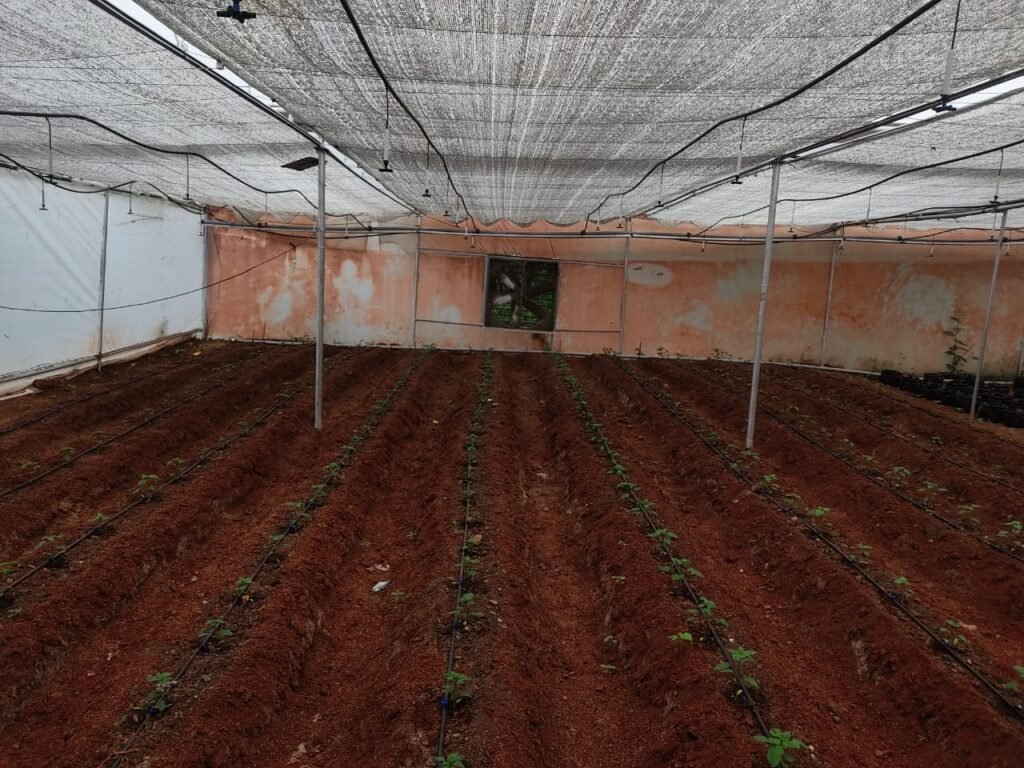
Temperature and Humidity Sensor
Humidity Sensors
- Capacitive Humidity Sensor:
- Principle: Changes in relative humidity (RH) cause a change in the capacitance between two conductive plates separated by a moisture-absorbing dielectric material. This capacitance change is measured and converted into a humidity reading.
- Pros: Accurate, stable, and widely used.
- Cons: Can be affected by contamination and temperature fluctuations.
- Resistive Humidity Sensor:
- Principle: A hygroscopic (moisture-absorbing) material changes its electrical resistance based on the amount of moisture it absorbs. This resistance change is measured and correlated to humidity.
- Pros: Simple and inexpensive.
- Cons: Less accurate than capacitive sensors and can drift over time.
- Thermal Conductivity Humidity Sensor:
- Principle: Two thermistors (temperature-sensitive resistors) are used, one exposed to the ambient air and the other sealed in dry air. The difference in their thermal conductivity, influenced by the moisture content of the ambient air, is measured and used to determine absolute humidity.
- Pros: Measures absolute humidity.
- Cons: Less common and can be sensitive to airflow.
Temperature Sensors
- Thermocouple:
- Principle: Two different metals joined at a junction create a voltage that varies with temperature due to the Seebeck effect. This voltage is measured and converted into a temperature reading.
- Pros: Wide temperature range, fast response, and inexpensive.
- Cons: Requires a reference junction and can be less accurate than other types.
- Resistance Temperature Detector (RTD):
- Principle: A metal’s electrical resistance increases with temperature. This change in resistance is precisely measured and used to determine temperature.
- Pros: High accuracy and stability.
- Cons: More expensive than thermocouples and have a slower response time.
- Thermistor:
- Principle: A semiconductor material changes its resistance with temperature. Thermistors can have either a negative temperature coefficient (NTC) or a positive temperature coefficient (PTC).
- Pros: Small size, fast response, and high sensitivity.
- Cons: Non-linear response requires more complex signal conditioning.
- Semiconductor-based Temperature Sensors (e.g., IC sensors):
- Principle: Integrated circuits utilize various semiconductor properties to measure temperature, often with built-in signal conditioning and digital outputs.
- Pros: Convenient, accurate, and easy to interface with digital systems.
- Cons: Can be more expensive and have limitations in extreme temperatures.
Since some error in pre-existing installed humidity sensor was observed, we had a discussion to understand the humidity sensor working from 1st principle, thinking and understanding from 1st principle challenges our shallow understanding and belief.
From the discussion we understood that in resistive type humidity sensor hygroscopic material absorb moist and conductivity increases and due to decrease in resistance, voltage drops down and because of this inverse relation it’s difficult to calibrate them.
Capacitive humidity sensors utilize the relationship between humidity and the dielectric constant (a material’s ability to store electrical energy) of certain materials.
- The Structure: These sensors have a thin layer of hygroscopic (moisture-absorbing) material sandwiched between two electrodes.
- The Process:
- As the humidity increases, the hygroscopic material absorbs moisture.
- This changes the material’s dielectric constant, which in turn alters the capacitance (ability to store electrical charge) between the electrodes.
- The sensor measures this change in capacitance and converts it to a relative humidity reading (the amount of moisture in the air relative to the maximum amount it could hold at that temperature).
Thermal Conductivity Humidity Sensors: A Closer Look
The Science Behind It
Thermal conductivity humidity sensors harness the fundamental principle that different gases conduct heat at distinct rates. Water vapor, being a gas, has a different thermal conductivity than dry air. This difference is exploited to measure humidity.
- The Two-Element Design: These sensors have two heated elements, often thermistors (temperature-sensitive resistors), arranged in a Wheatstone bridge configuration.
- Exposed Element: One thermistor is exposed to the ambient air, where its temperature is influenced by the air’s humidity.
- Sealed Element (Reference): The other thermistor is sealed in a chamber containing a reference gas with a known, constant humidity level. This element provides a baseline for comparison.
The Role of Thermal Conductivity and Specific Heat
- Thermal Conductivity: The exposed element loses heat to the surrounding air through conduction. The rate of heat loss is directly proportional to the thermal conductivity of the air. Since moist air has a higher thermal conductivity than dry air, the exposed element will cool more quickly in humid conditions.
- Specific Heat: Specific heat is the amount of heat energy required to raise the temperature of a substance by a certain amount. The specific heat of water vapor is higher than that of dry air. This means that moist air can absorb more heat energy for a given temperature change compared to dry air.
Why Nitrogen (N2) Fills the Sealed Reference
The sealed reference chamber is typically filled with nitrogen (N2) or another dry, inert gas. Here’s why:
- Known Humidity: Nitrogen has a very low and predictable humidity level. This ensures that the sealed element’s temperature remains stable and only changes in response to the ambient temperature.
- Chemical Inertness: Nitrogen is non-reactive, meaning it won’t interact with the sensor materials or change over time. This guarantees the long-term stability and accuracy of the reference element.
- Thermal Stability: Nitrogen has consistent thermal properties, ensuring that its thermal conductivity and specific heat remain constant within the reference chamber.
The Temperature Difference: The Key to Measurement
The sensor measures the difference in temperature between the exposed and sealed elements. This temperature difference is directly related to the absolute humidity of the air. The greater the humidity, the faster the exposed element cools, leading to a larger temperature difference.
Why the Sealed Reference is Essential
The sealed element acts as a reference point. By maintaining a constant humidity level and temperature with the help of nitrogen, it ensures that any changes in the exposed element’s temperature are solely due to the humidity of the ambient air. This eliminates the influence of other factors like ambient temperature fluctuations, making the sensor more accurate and reliable.