Plastics can be of the different grades but usually classified into two groups, firstly recyclable plastics and secondly non-recyclable plastics. I was given a project on HDPE recyclable plastic bottle cleaning proposed by Jayant Pai, our client.
About the client, Jayant Pai, Founder Director of Social Seva Initiatives, a Pune based Section 25 not for profit company focused on applying innovative technology solutions to enable social impact at the base of the pyramid. With over 30 years of entrepreneurial experience, Jayant also founded SETU, a group of software companies based in Boston, USA and Pune India. Jayant holds a BE in Electrical Engineering from MS University, Baroda and an MS in Computer Science from Syracuse University, New York, USA.About the client,
I, Prasad Divekar and Arun Dixit visited the existing plastic cleaning unit at Katraj on 29th Aug’2020. Namrata and Sangeeta were the two employees who used to clean the received plastic bottles. In this unit, they washed and removed the label and remaining chemicals in the bottles. Usually, harpic, moisturisers, oil cans and any other bottles having a volume less than 5L are cleaned here. The current cleaning process is soaking of the bottles in water containing detergent for night long, followed by labour scrubbing and finally allowing them to dry. After the bottles were dried they were made to pass through shredders where the bottles were shredded into small pieces. Later on these shredded pieces were melted and drawn into thin filaments which are used for 3-D printing. Katraj unit primarily looks upon cleaning and shredding operation of this whole cycle.
Manual scrubbing employed for removal of the labels. Shredding process.
Layout of Plastic Cleaning Unit, Katraj.
Problems in the current system: | Requirements: |
1.Time required for cleaning per bottle is 1min. 2.Continuous standing required for the cleaners. 3.Portability of the whole set-up. 4.Large amount of water was required and then drained ultimately.(Higher water wastage 4800L for 50kg) 5.Inefficient heat distribution in the soaking process. 6.Dried shampoo and dried moisturizers bottles were hard to clean. | 1.1500 kg/month HDPE cleaning unit. 2.Easier adhesive removal method. 3.Label removal – Cleaning the bottles – Recycling used water unit, were the main unit processes required. 4. 6ft x 2ft x 2ft compact machine. 5.Portable machine. 6.Properly insulated soaking water bath. 7.Low maintenance machine. 8.Cost margin: 5 Lakhs/unit. |
Unit Process involved in this system:
- Pre-washing of the bottles.
- Bottle Cap and Ring removal.
- Soaking.
- Label removal by manual scrubbing.
- Final wash.
- Drying.
- Shredding.
- Pre-washing of the bottles.
This initial step is very important as a hygiene point of view. These bottles are usually picked by the rag pickers from the waste and delivered here. Hence, it becomes essential to clean the outer surface before the later processing. We brainstormed and finally arrived on a rotary top load drum washer. We developed a 200L prototype for the same. Ergonomics played a important role in deciding the dimension of this drum. For fabrication details visit:http://vadic.vigyanashram.blog/2020/09/20/plastic-bottle-cleaning-unit/
Procedure followed:
Step 1:
Deciding the dimensions of the RTLD drum. Ergonomics played important role along with the strength of the material calculations. Motor specifications were also derived from the moment of inertia and torque calculations.
Step 2:
Designing the unit as per the calculated dimensions on the solid works and then later based on the design we devised the bill of materials of all the required entities.
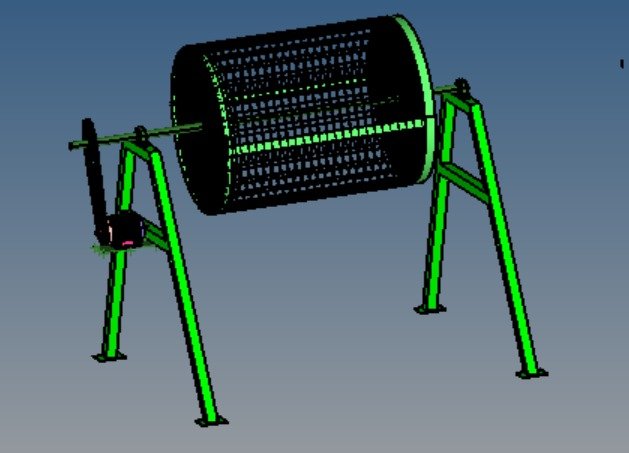
Particulars | Specifications | Quantity | Unit | Price/unit | Total Cost |
1 inch wire mesh. | 3 * 10 ft | 6.5 | kg | 80 | ₹520.00 |
Wiper Motor | 12 V, 48 rpm, 14 Nm | 1 | unit | 2200 | ₹2,200.00 |
Adapter | 1 | unit | 600 | ₹600.00 | |
Pillow block pedestal bearing | 15mm dia, P202 ans P204 | 2 | unit | 265 | ₹530.00 |
Shaft | 15 mm x 4.5 ft | 3.16 | kg | 36 | ₹113.76 |
Square tubes | 7.35 | kg | 58 | ₹426.30 | |
Chain Sproket Set | 1 | unit | 750 | ₹750.00 | |
Auxilaries | – | – | 150 | ₹150.00 | |
Castors | 4 | unit | 260 | ₹1,040.00 | |
₹6,330.06 |
Bill of materials gives us idea on both- primary materials required for the fabrication and the finance involved for construction of this unit. Hence, devising a detailed bill of material is very important.
Step 3:
Procurement of the raw materials.
Step 4:
Fabrication. All the above like designing, bill of materials, excel sheet calculations do give a good idea about the whole construction part but a lot changes when it comes to actual fabrication. Note: Imagining and designing the machine to a very fine detail always plays an important role! Finer the design easier is the construction. Also while purchasing the prime parts don’t forget to get the needed auxiliaries.
The above fabrication has five major parts:
- Construction of the frames. Strength of material calculations helps us to decide on the material used for the frame fabrication. Frame needs to hold the strength of your drum as well as the plastic bottles and the water’s thrust applied on it for its cleaning.
- Construction of the frame for rotary drum. These frames acts as a support system for the mesh cylinder as fabricating the drum using just the mesh will provide no good strength to the machine.
- Insertion of the mesh into the frames. This was a difficult task in all. cutting the mesh, inserting the mesh into the frames and welding it.
- Installing the shaft and the bearing. Specification of each and every part plays important role as in our case already had 15 mm pedestal bearing but it so happened that procuring 15 mm thick shaft became a challenge for us and hence had to get 16 mm shaft and then thin it using the leth machine.
- Lastly upon the installation of the drum on to the frame, the last step is the uploading of the motor.
Step 4:
Surface treatment of the constructed RTLD. Surface treatment before coating or painting the metal body becomes an essential thing when lifetime of the unit is considered. Surface treatment includes cleaning, filing, grinding, pickling, grease removal and lastly primer coating.
Pickling was very important in our case as most of the surfaces were seen to rust. Few experiments were performed varying the concentration of sulfuric acid. 25% v/v sulphuric acid and distilled water solution was observed to give the desired results. For more details click on : http://vadic.vigyanashram.blog/2020/10/29/surface-treatment-of-ss-and-ms/
Surface treatment of the RTLD
Firstly, using the grinding wheel and sandpaper ensure that the surfaces are clean of physical debris. Once the surfaces are cleaned then proceed to the rust removal.
Preparation of pickling agent.
Take 25 ml conc. sulfuric acid and add it to the beaker containing 75 ml distilled water. Addition should be very slow and to be done carefully. This is an exothermic addition and hence one needs to be aware of the heat that might be generated. In a beaker take plaster of paris enough to thicken the solution that was made. Pour the mixture into the plaster of paris and ajust the amounts that you get not so thick and not so thin consistent solution.
!Note plaster of paris donot play any role but to thicken the solution so as to aid the application.
- apply the pickling paste on to the rusted surfaces.
- Let it stay for 10 mins and then wash it off with the water.
- Immediately using a dry cloth wipe it off and apply the first coat of primer.
- after the drying, apply second coat of the primer.
- Finally, paint the surfaces in the desired color.
Before treatment Application of pickling paste After the treatment
2. Bottle cap and ring removal.
This second step is a manual work. the working people will manually indulge into removal of the cap and the rings.
3. Soaking.
Soaking plays an important role. The adhesive and the contents of the bottle can be easily removed once soaked efficiently. the dried shampoos, sticky oils and moisturizers can be washed off using hot waters. Even, the adhesive in the stickers get loosen at higher temperatures. Experiments were performed varying the temperature – 45 degree Celsius, 55 degree Celsius, 65 degree Celsius and 75 degree Celsius, time and pH. Good results were obtained at 65 degree Celcius. Also, no bigger effect of pH was observed. As above 70 degrees it is observed that the HDPE bottles get softening. Also, no bigger effect of change in pH was observed. Hence, 65 degree Celcius hot water for an hour is known to be ideal for the soaking.
Parameters for design:
- 65 degree Celcius hot water for 1 hour.
- Bottles should get dipped, filled and emptied.
- Pressing action needed for the filling of the bottles.
- Insulated tank.
- Ergonomic dimensions.
- 100 W motor
Design Development and Brainstorming ….
- Design 1.0
Firstly a rotary system was designed and finalised. A perforated cylinder containing the bottles was to be rotated which is partially submerged in a stationary hot water containing cylindrical drum. The idea of having perforated cylinders eventually changed to four perforated rectangular blades mounted on a shaft. These four perforated blades dimensions were such that the clearance obtained between the blade and the outer cylinder’s edge is close to 30 mm. The two main jobs of the blades were to push the bottles into the water so that they are soaked and filled with the hot water and later lift the bottles in order to empty them. This will make sure that bottles are soaked along with rinsing.
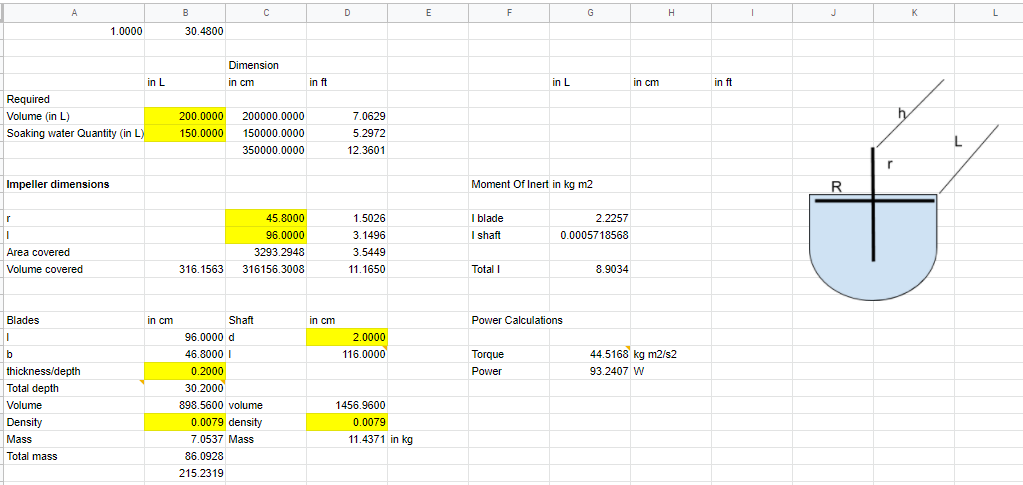
2. Design 1.1
A second brainstorming session gave rise to the issues that will occur when consider of rotary drums. The alignment and setting up a correct axis during the fabrication and maintenance of the system once installed will be of great complication when compared with other mechanical or vibrational systems. In the second session another idea of having a stationary tank with bottles immersed in the water but a plunger on a top was discussed. The bottles were supposed to be drilled with hole and then put it in the tank. The job of the plunger was to press and release the bottles in the tanks. when pressed by the plunger, the bottles will be filled and when released bottles will loose some amount of water. Initially we thought of having a mechanical plunger but later in the third and final brainstorming a lot changed again!
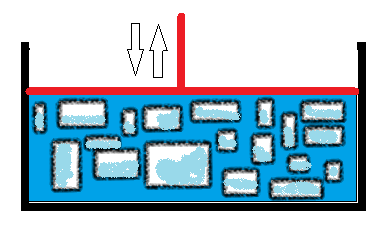
The rectangular white space denotes the plastic bottles of volume between 100 ml to 5 L.
Problems in design 1.1..
- Bottles will not be fully filled.
- Air gaps will result when bottles are randomly positioned.
- Rinsing operation would not be carried out effectively.
- Delta T (difference in temperature) at the surface and bottom was approximately 5 – 7 degrees.
- Insulation was to be done carefully as heat losses are more.
- Mechanical plunging will be tougher when size increases and when made automatic the system will be as complicated and expensive as rotary.
3. Design 1.3.
After discarding rotational and plunging action, vibration motion was discussed in detail. Again a stationary tank with a cage containing the bottles submerged in it. Bottles are drilled.
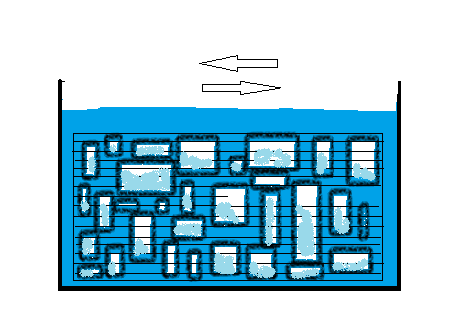
A stationary tank containing water where in a cage containing bottles is submerged in it. The cage is vibrated to and fro in the tank.