Introduction:
Compost is decomposed organic material, such as leaves, grass clippings, and kitchen waste. It provides many essential nutrients for plant growth and therefore is often used as fertilizer. Compost also improves soil structure so that soil can easily hold the correct amount of moisture, nutrients and air.
Composting also has “upstream” benefits, which further conserve our resources and reduce greenhouse gas emissions. When this compost is used on fields, it displaces synthetic chemical fertilizers. Fertilizer production requires intensive fossil fuel energy and seriously impacts human and environmental health.
Benefits of Leaf Compost :
Composting leaves makes a dark, rich, earthy organic matter that can be used like soil. It adds nutrients to garden soil and the larger particle size helps enhance the tilth and loosen compacted earth. Compost retains moisture and repels weeds when used as to dressing or mulch.
Need of brawn matter:
The climate and seasons changes will have a big effect on composting. Small adjustments can be made when changes happen such as when the rainy season approaches.
Moisture Content:
Microorganisms living in a compost pile need enough moisture to survive. Water is the key element that helps transports substances within the compost pile and makes the nutrients in organic material accessible to the microbes. Organic material contains some moisture in varying amounts, but moisture also might come in the form of rainfall or intentional watering.
Problem occures due to high moisture and solution
problem defination :
Compost piles smell like ammonia when they give off excess nitrogen (N) in the form of ammonia (NH3). This problem occurs most often if a composter has been adding high-nitrogen products. Mixing in brown material can also restore the carbon-nitrogen balance. for shredding this brawn material ,we used pulverizer which was already designed for grains.
Objective : to convey the brawn material from hopper of pulverizer to achieve the exact efficiency of machine.M
Multipurpose pulverizer:
Image :
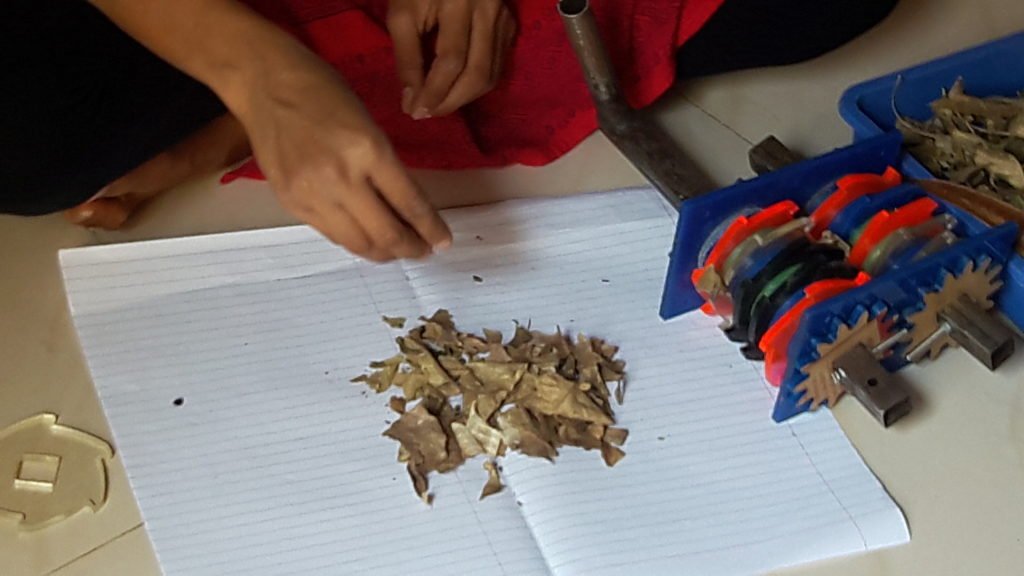
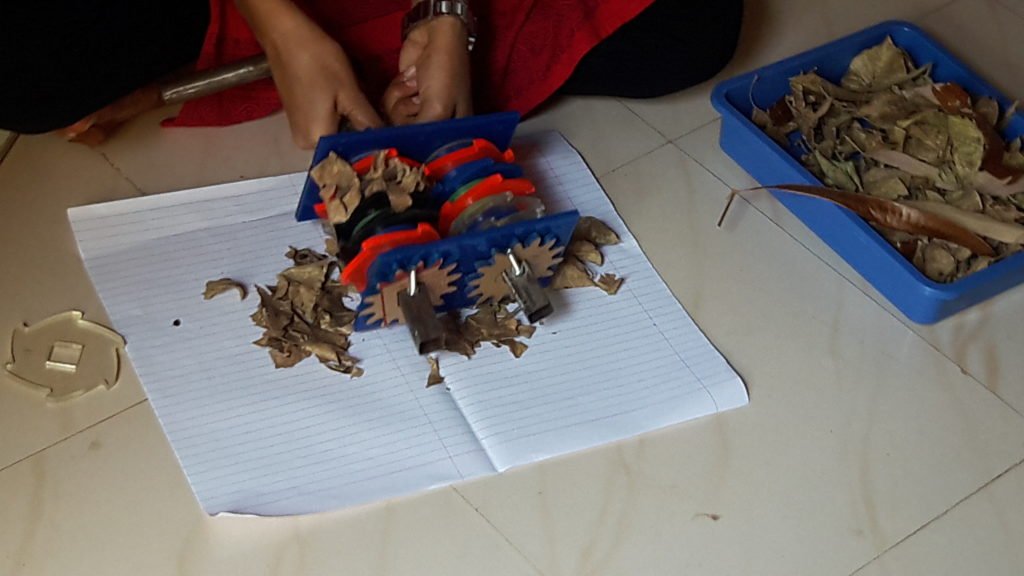
Machine specification :
Features : SSC1
grinding capacity : 10-12 kg/hr.
power consumption : 1.4 kwhr.(unit)
electric motor : 1HP single phase
weight : 30 kg
dimensions :20″×12″×30″
Pulverization: A solid substances in the form of tiny particles
Pulverizer :A pulverizer or grinder is a mechanical device for the grinding of many different types of material.
Trials
Objective: To find out the conveying mechanism for dry mass
Trial 1
The 1 trial for conveying dry matter through hopper was carried out on mechanism which was made by siddhesh sir.
1 | shaft | 2 | 25mm dia. |
2 | blades | 12 | 10 mm thick |
3 | gear | 2 | |
4 | Clearance between two blades | 5mm | |
5 | Weight of dry material | 100 gm | |
6 | Time require to convey material | 4min.3sec. | |
7 | Speed | 12 rpm | |
8 | Material used for prototyping | Acrylic sheet | 10 mm |
Problems occurred in operation,
- The assembly required more energy to operate.
- Distance between two blades or clearance was too less, it caused blockages.
- It’s required more time to convey and cut the material.
Conclusion:
from the above trial it concluded that the mechanism can’t work properly due to less clearance between blades.
Random calculation of Maximum -minimum size and thickness of dry leaves
Sr. No. | Length(cm) | Width(cm) | Thickness(mm) |
1 | 14 | 2 | 1 |
2 | 11 | 6 | 1 |
3 | 8 | 5.5 | 1 |
4 | 8 | 4 | 0.5 |
5 | 11 | 2 | 0.5 |
6 | 16 | 2 | 0.5 |
7 | 7.5 | 5 | 1 |
8 | 7 | 5 | 0.5 |
- Maximum length of dry leaves =16cm
- Maximum width =5.5 cm
- Maximum thickness =1mm
Bulk density of dry mass:
- Weight of tray = 300 gm
- Volume of tray =length ×width× height
= 36×25×7 = 0.006300 m3
- Mass of dry leaves = 0.288 kg
- Bulk density of dry mass = mass/volume
= 45.714 kg/m3
Trial 2
Objective: The 2 trial was carried out on same mechanism with decreasing size of assembly and increase the clearance between blades
Assembly consist of,
1 | shaft | 2 | 25mm dia. |
2 | blades | 7 | 10 mm thick |
3 | gear | 2 | |
4 | Clearance between two blades | 8mm | |
5 | Weight of dry material | 100 gm | |
6 | Time require to convey material | 3min.40sec. | |
7 | Speed | 14 rpm | |
8 | Material used for prototyping | Acrylic sheet | 10 mm |
Conclusion : It’s also required more energy to operate but reduce time as compare to 1st one
Trial 3
Objective: design and development of conveyor cum cutting shredder mechanism (prototyping).
Material: acrylic sheet pencil, scale, cutting tools etc.
To found out the conveying mechanism for pulverizer, we design another prototype mechanism and test it.
Procedure:
- Firstly, collect the information about different blades which was used for shredding and also for conveying.