16/8/24
This was our first assignment in vigyan ashram
we got an assignment to design a vessel stand in the ashram. Since we were a group of four, we were asked to make four different designs and one of the designs was to be finalised.
17/8/24
Firstly, we went to the mess to take the dimensions of the vessels for which we wanted to design a stand. The measurements we took were as follows:
Plate- Dia = 33 cm, Height = 2 cm
Bowl-Dia= 7.7cm, Height = 3.8 cm
Spoon- Length = 15.5 cm, Width = 3.6 cm
18/8/24
After taking the measurements we were asked to draw a rough drawing of the design After the rough sketch was completed we showed it to Prasad sir. Then he told us to make calculation on how much will be the pressure of all the vessels and what is the bearing capacity of our respective structures.
CALCULATION: Force = Mass x Acceleration = 0.650x 9.8= 6.37kg m/s = 6.37N
Also Area = Length x Width = 0.3m x 0.13m = 0.039 m2
Now, Pressure = Force/Area = 6.37/0.039 = 163.3N/m2
By taking some pressure of water assume approximately Pressure = 200N/mm2
Ultimate Stress = Allowable Stress x Factor of Safety = 200 x 2 = 400N/m2
20/8/24
After all the dimensions were decided we started creating the model on the Solidworks software. Following is the model that I created:
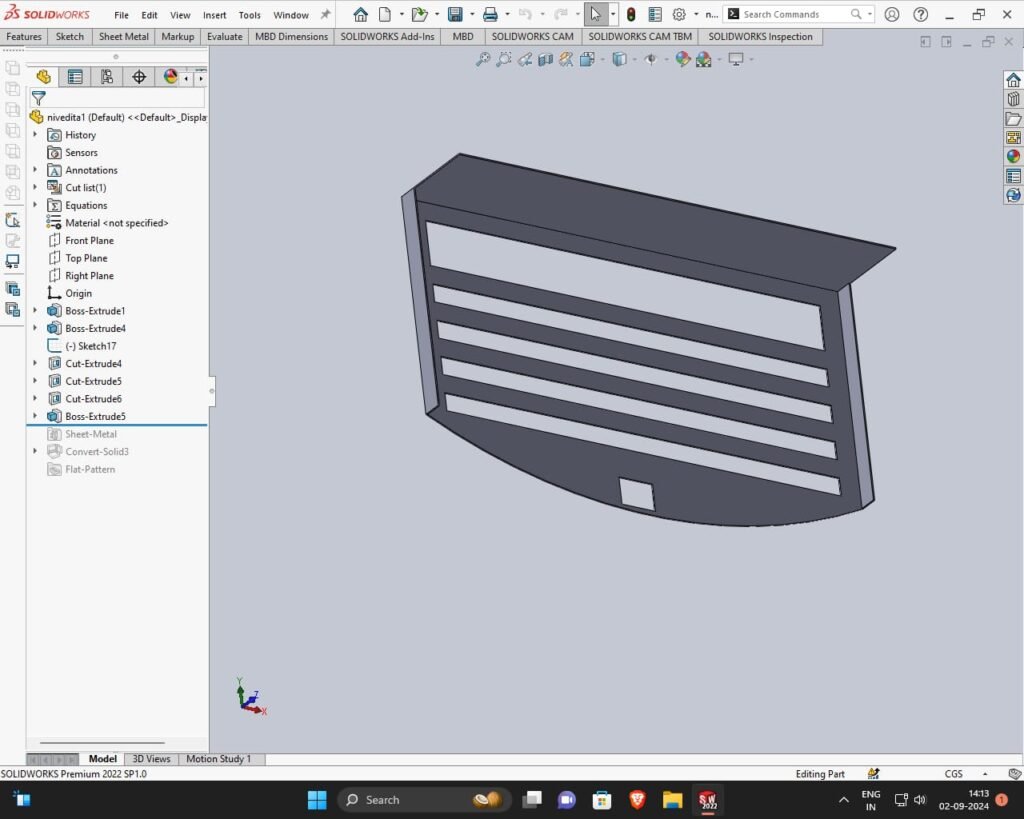
After creation of this model we converted it into sheet metal because we were going to use Plasma cutter tocut the sheet in desired shape.
Given below is the flattened form of the model
:
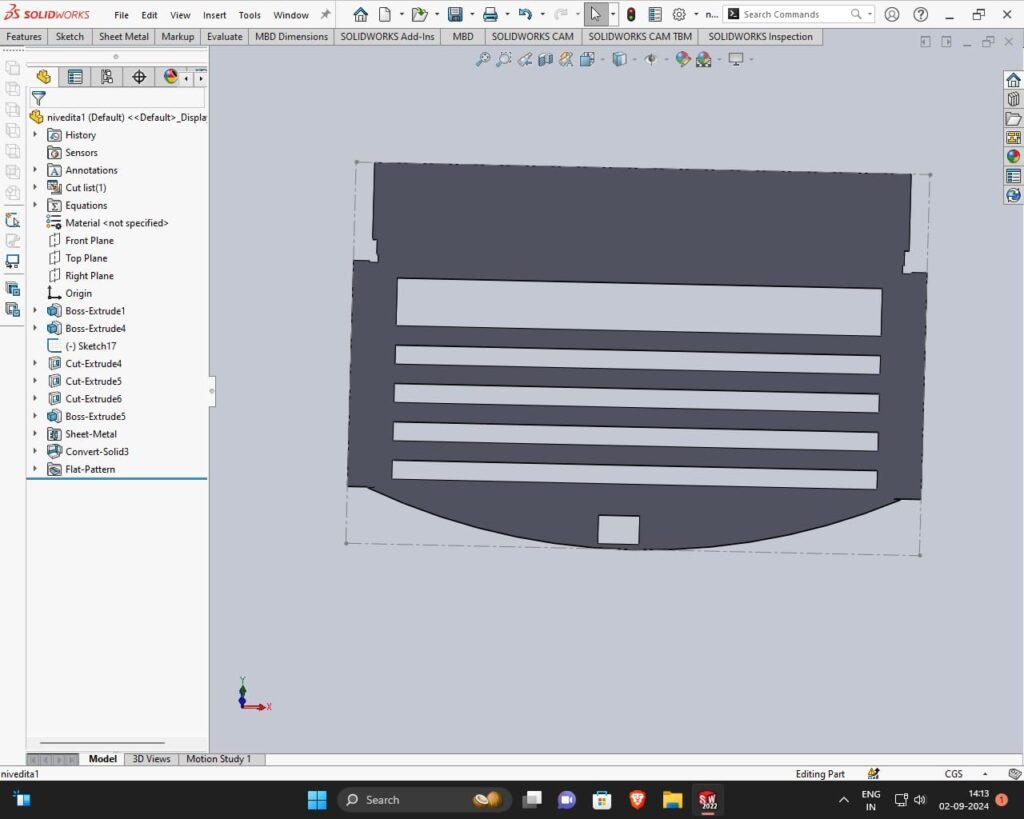
21/8/24
After creation of model I showed it to Prasad sir. Then the next step he told us to estimate the cost that will be required for making the model. Ofr that first I found out the area of the flat form of model.
The calculations of cost is as follows:
Firstly found out the area of the flat form of model
Area = 37700.59mm^2
Volume = 37700.59×0.8 = 30160.472m3
Then find Cost of material volume × Density = 30160.472× 7.96×10^-6×10^4 =0.3016kg
1kg sheet metal=65 rs
0.3016×65=19.604 rs
23/8/24
After finding the cost, we cut the design on the laser cutter. We used cardboard as material to cut on the laser cutter . To cut on the laser cutter, first save the file in dfx and then,Imported image in RD Works software and gave power 90% and speed 30 mm/s and saved file in pen drive.
For starting Laser cutting operation following steps are followed:
Going to the file – Select the Udisk+ – Select the Read Udisk – Select the Copy to Memery – Esc – On Exhaust Switch -On Laser Switch – Select Model – Start
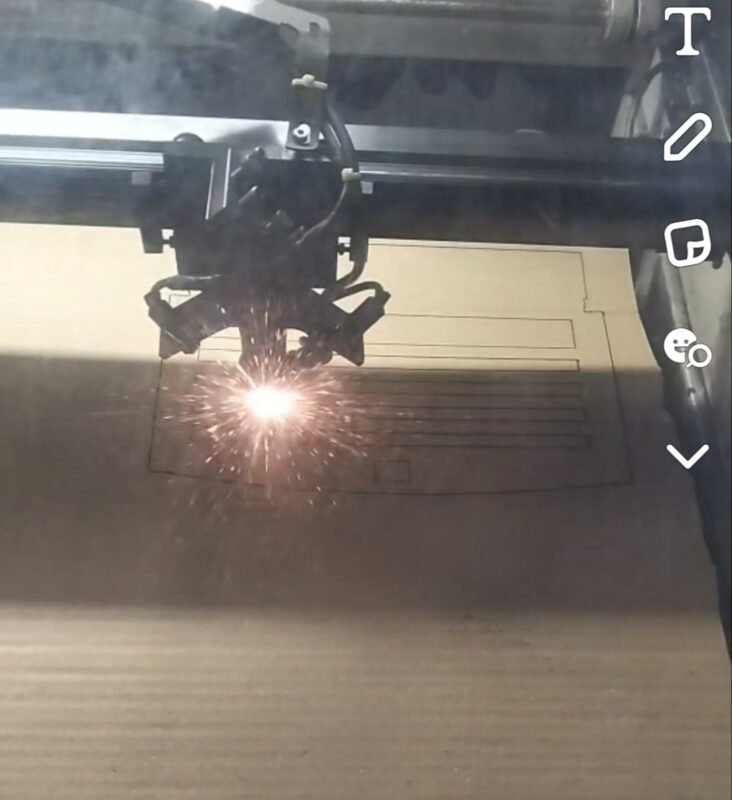
24/8/24
After four different designs were cut on laser cutter, we showed them to Prasad sir. Prasad sir asked to combine all the four designs and make one design. After that again we created a design
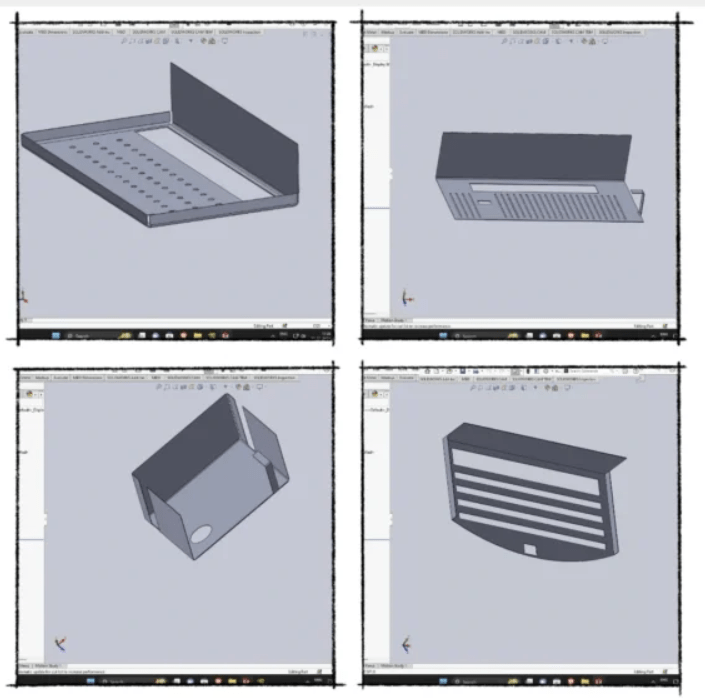
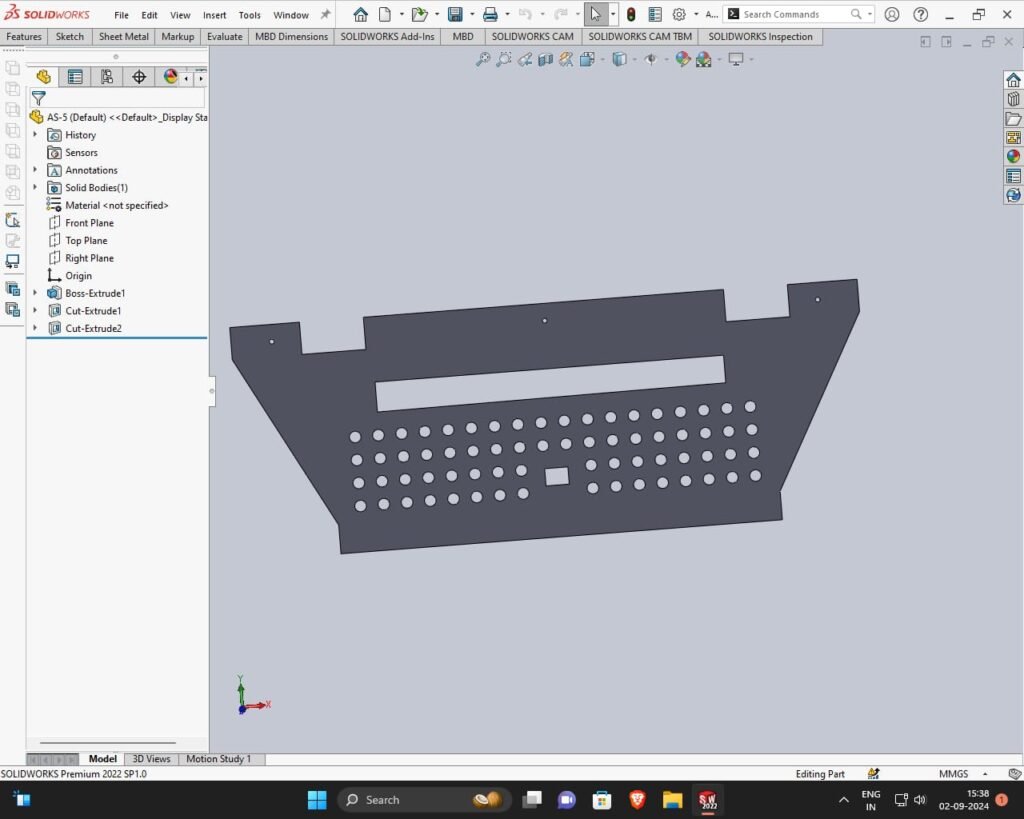
25/8/24
Dixit sir asked the question what is stress and it was discussed.
After that we learned about types of welding in workshop.
Types of welding in workshop:
Co2 gas welding
Arc welding
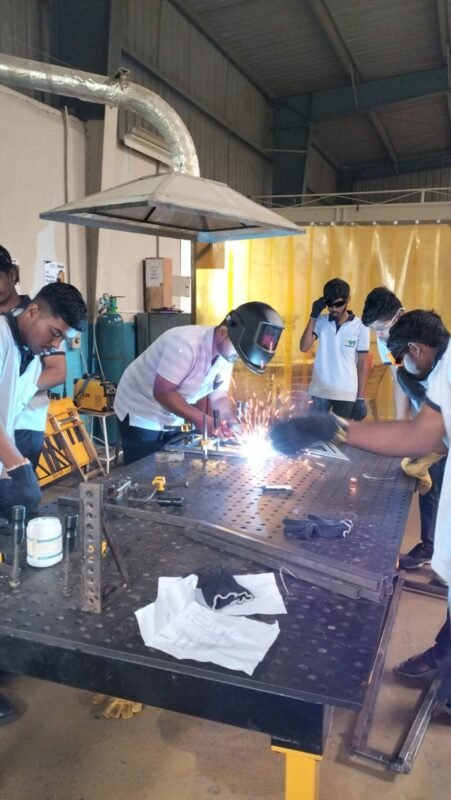

After that we again went to DIC lab and converted the model of vessel stand to dxf file and copied it into pendrive. Then we again laser cut the model in FAB Lab by repeating same previous process of laser cutting. Following is the result we got :
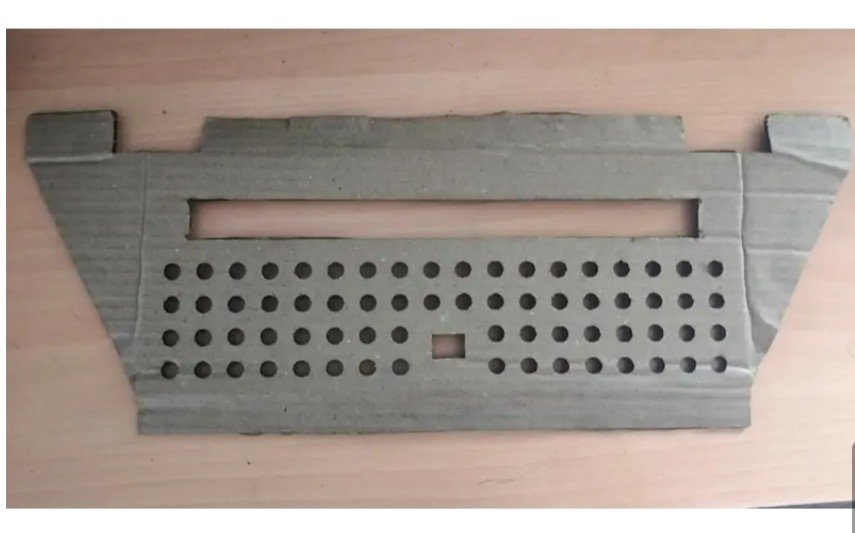
26/8/24
On this day we had discussion about the model that we cut on the laser cutter and Mahesh sir told us to make the slots for the screw.Then we edited the design again in solidworks and added the slots for the screws
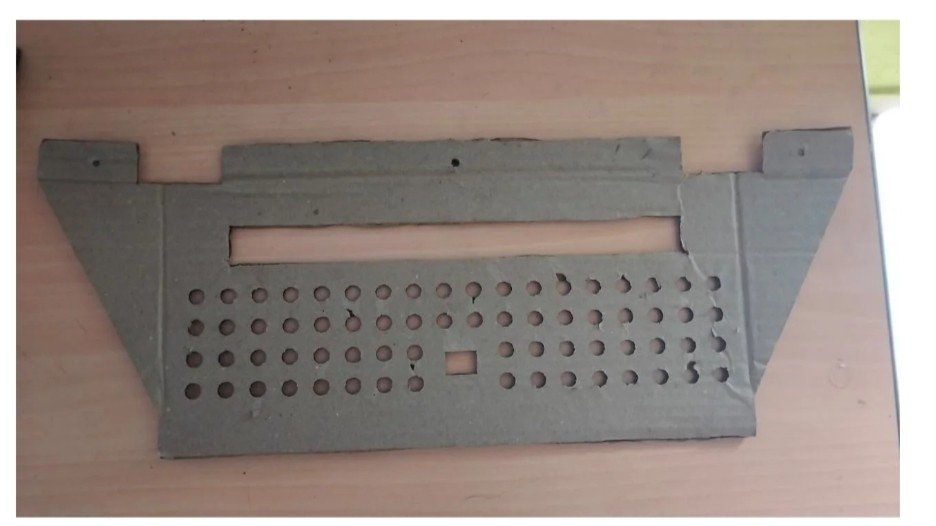
After creation of model we were told to estimate the cost of the material required so we estimated the cost.
CALCULATION:
Net Weight = Total Volume * Density of MS
Total Volume: Area * Thickness = 76899.29 mm2 * 0.8 mm = 61519.432 mm3
Net Weight = 61519.432 mm3* (7.8 * 10-6 Kg/mm3)
Net Weight = 0.47 kg
Now, Cost of MS steel per kg = Rs 65
Cost for 0.34 kg Mild Steel = 65 * 0.47 = Rs 30.55
27/8/24 – 1/9/24
On these date we attend designing thinking training of MSFDA in vigyan ashram
2/9/24
After creation of model we were told to estimate the cost of the material required so we estimated the cost.
CALCULATION:
Net Weight = Total Volume * Density of MS Total Volume: Area * Thickness = 111276.93 mm2 * 0.8 mm = 89021.544 mm3
Net Weight = 89021.544mm3* (7.8 * 10- 6 Kg/mm3)
Net Weight = 0.708kg Now, Cost of MS steel per kg = Rs 65
Cost for 0.34 kg Mild Steel = 65 * 0.708 = Rs 46.02
3/9/24
Again we showed the new model created to the Prasad sir and then he told us to bring some more modifications in the new design and also focus on some cost cutting. So we again edited this new design and we came to know that the part that we created to hold the plate and avoid it from touching the wall contains a lot of unnecessary material which results in increase in the cost. So we decided to remove the unnecessary material from that part.
24/9/24
I went for plasma cutting in the workshop but due to lack of use of plasma cutter for many days, even after trying many times, plasma cutting was not completed.
25/9/24
After the plasma cutter repair, we went to the workshop again. Mahesh sir informed us about plasma cutter. We all cut a part on plasma cutter
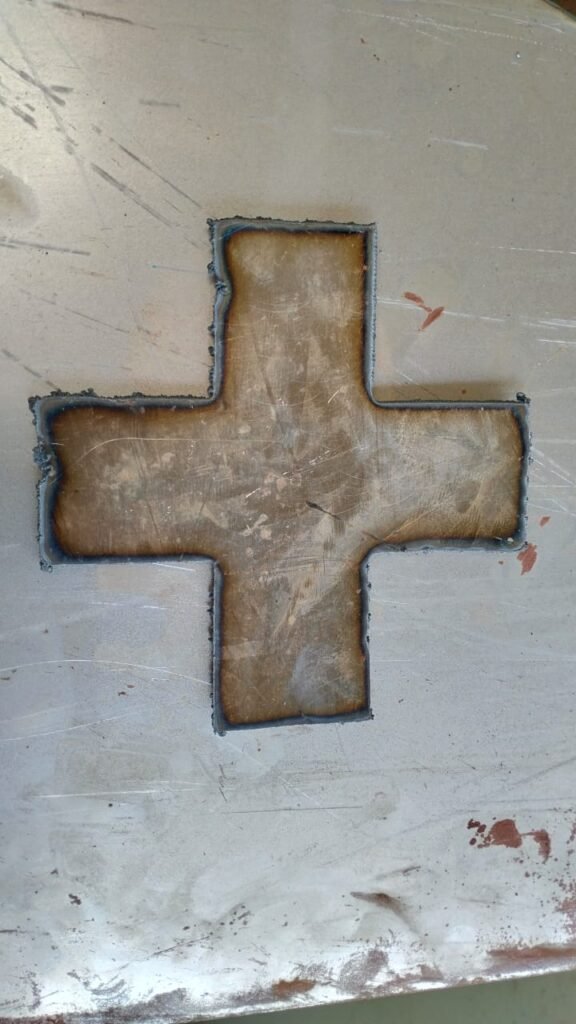
After that we again used old sheet for trail then the problem occured was the machine was unable to cut the holes of our required dimensions properly. we made some attempts but it was causing same problem so mahesh sir told us to change the design and increase the size of holes and reduce the number of holes.
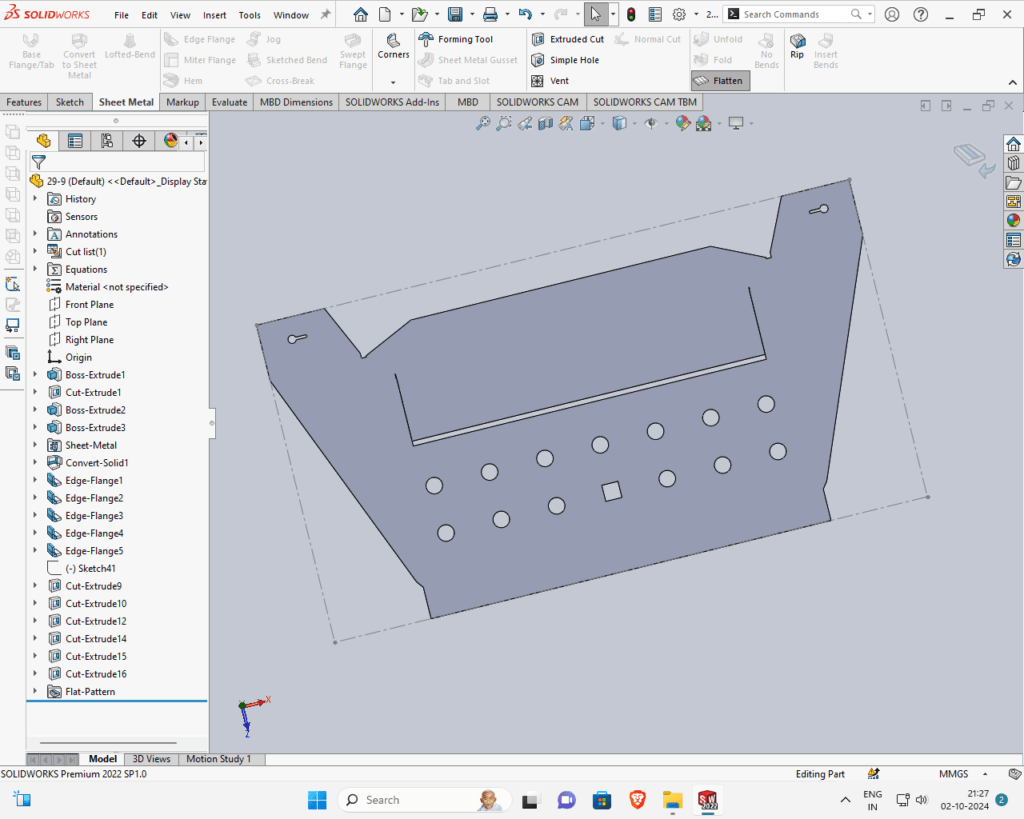
27/9/24
After changing the design, I started plasma cutting again, but because the sheet was not plain, the sheet was not cut properly, so I took another sheet from the workshop and cut it.Mahesh sir helped us in that we had to cut 7 sheets

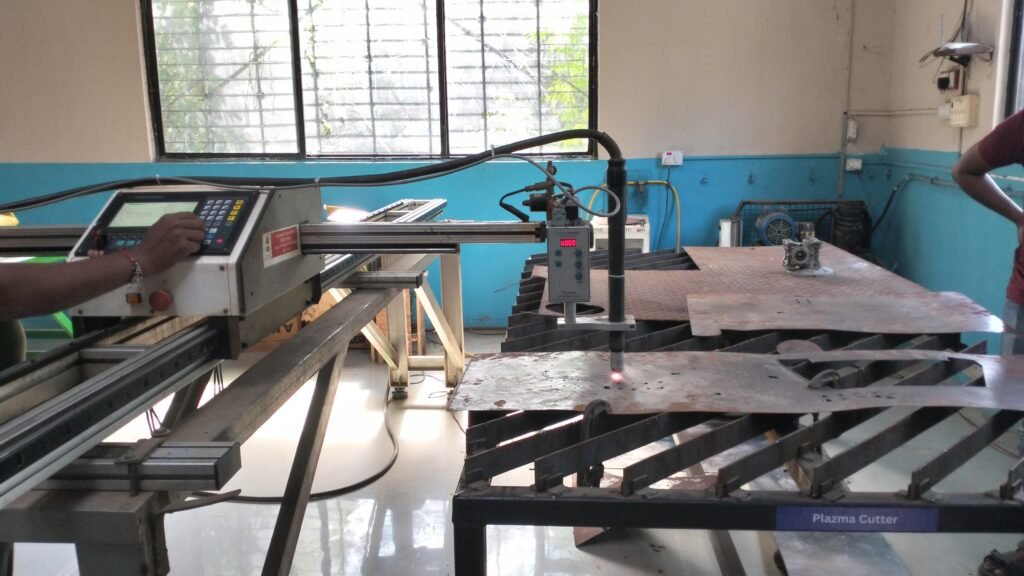
28/9/24
After the design cut, grinding operation was done on the stand so that no one should be hurt while using the stand
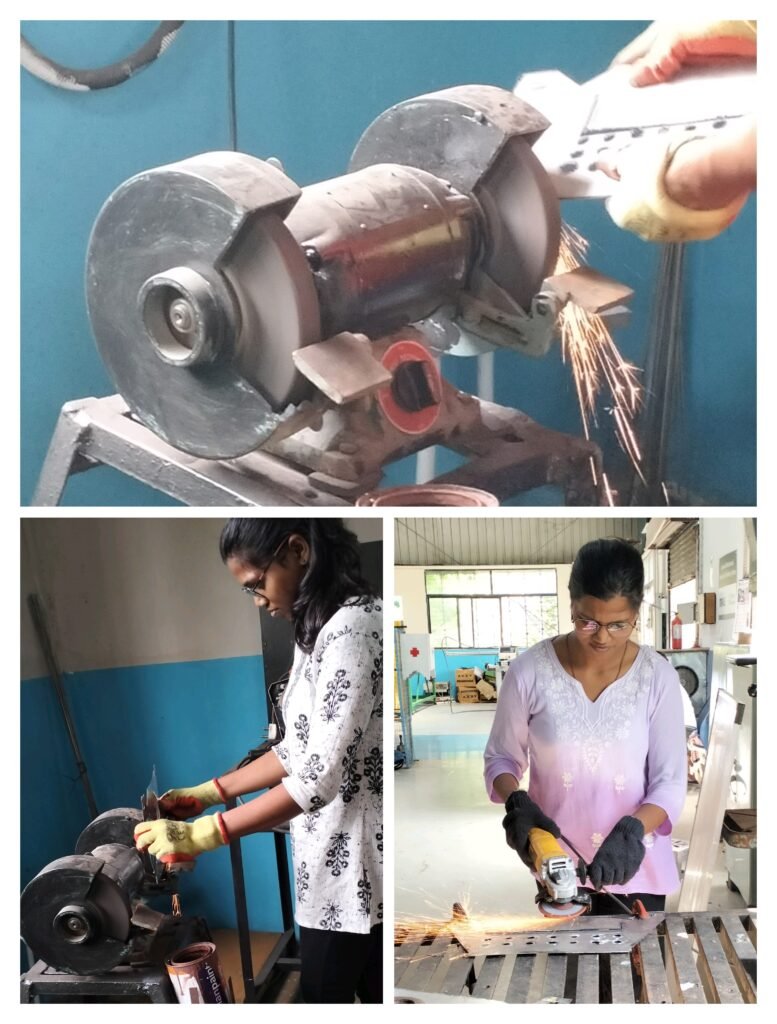
29/9/24
After the grinding operation was done we did the bending operation. For bending operation we used bending machine in workshop. Sometimes we used hammer cha as bending was not going well
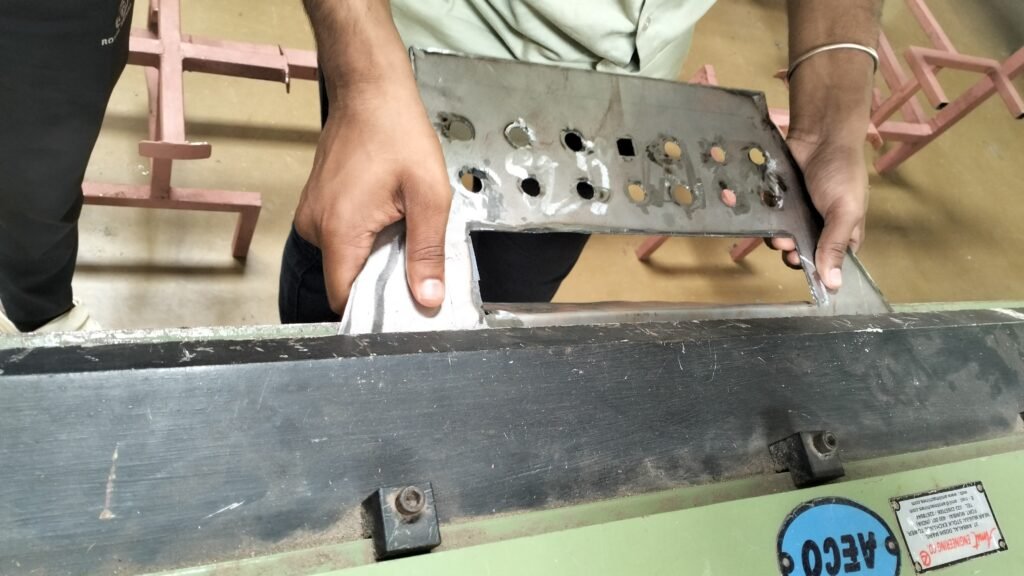
30/9/24
We completed the bending operation of some sheets
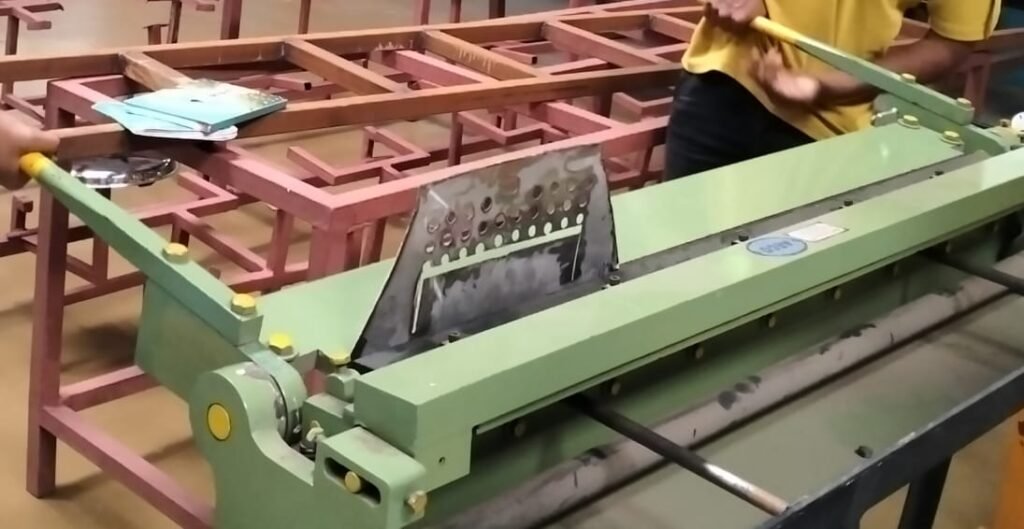
1/10/24
First it was cleaned with srands acid and then it was hanged in stand powder coating stand and powder coating was done and then it was kept in stand powder coating oven at 150 degree this process took 2 hours
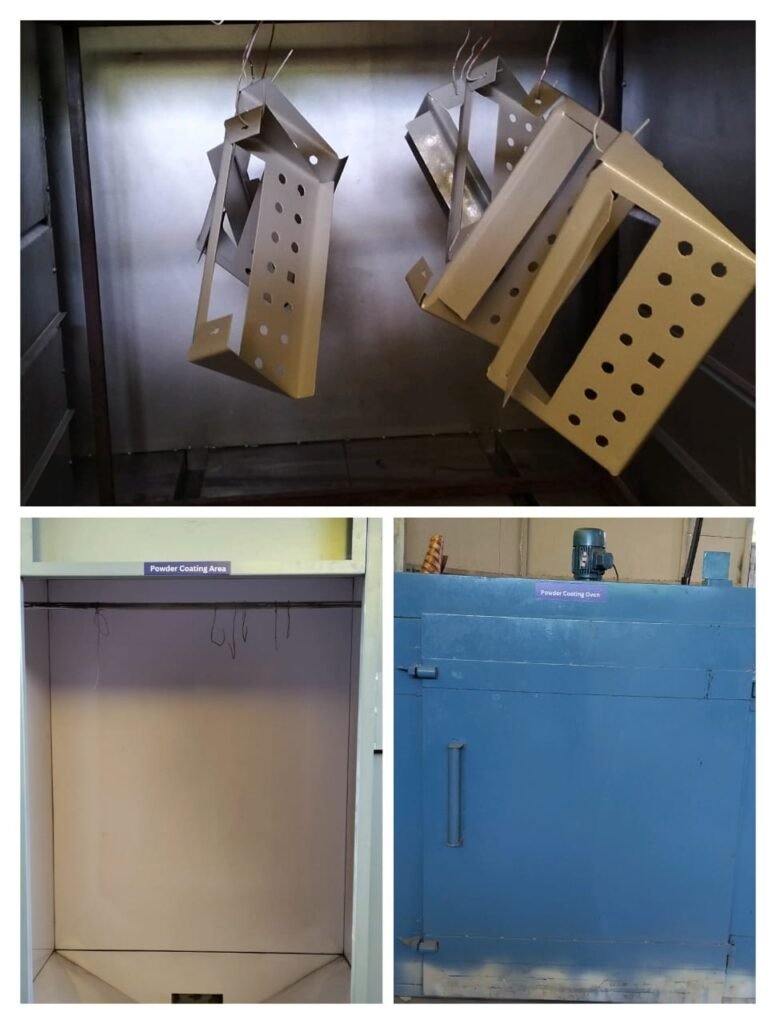
2/10/24
Today we set up a stand in the kitchen
First we removed the old stand in the kitchen.
And then fixed it to the wall with the help of stand 4 mm screw. Three stands were built with the help of wire because it was not possible to drive screws because of the grill of the window.
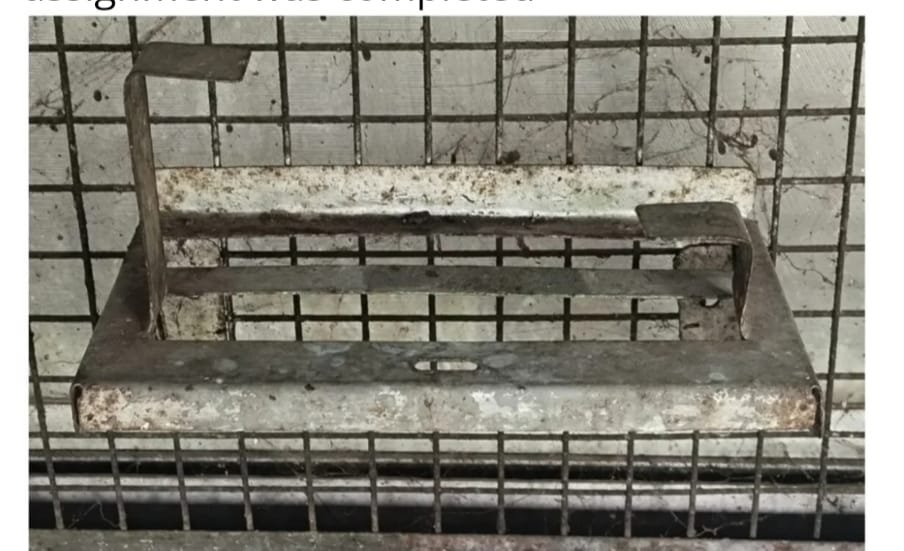
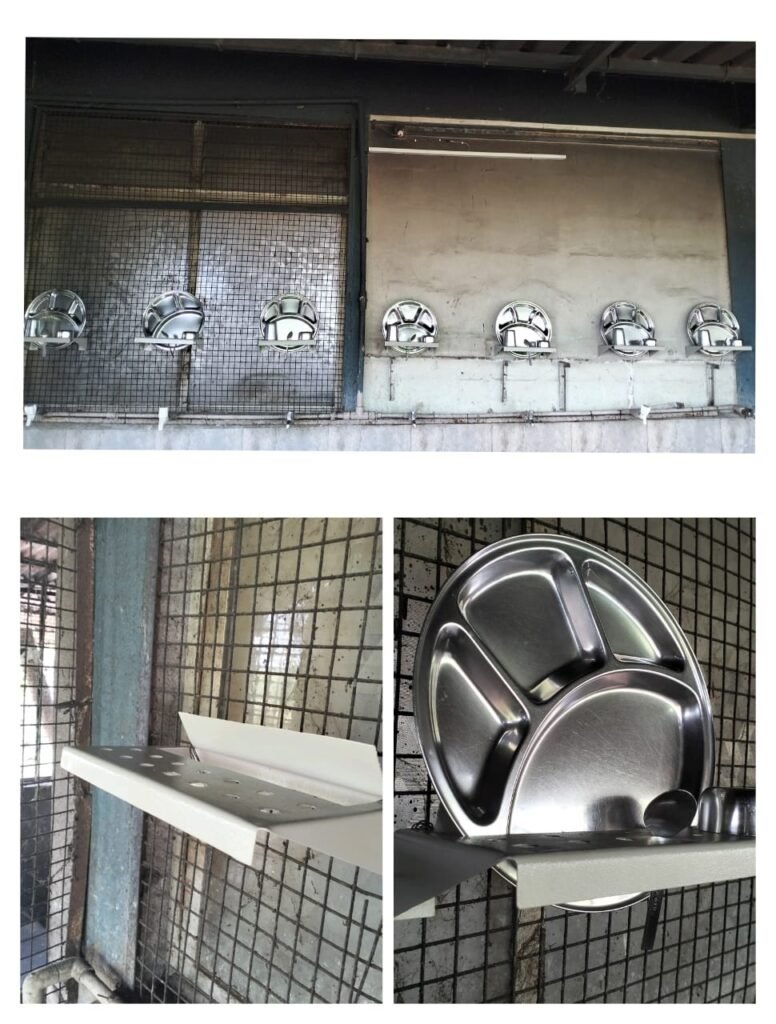
After creation of model we were told to estimate the cost of the material required so we estimated the cost.
CALCULATION:
Net Weight = Total Volume * Density of MS
Total Volume: Area * Thickness = 76146.33mm2 * 0.8 mm = 60917.064 mm3
Net Weight = 60914.064 mm3* (7.8 * 10-6 Kg/mm3)
Net Weight = 0.48kg
Now, Cost of MS steel per kg = Rs 65
Cost for 0.34 kg Mild Steel = 65 * 0.47 = Rs 31.2
Thus our first assignment was completed.