How Does Work Solar Dryer
Solar dryer receives the energy from sun and it dry the crops vegetable fruit
Solar dryer consists with different main parts
Black material is coated on heating element inside the box to absorb more heat from solar radiation . outer frame of made up of heat insulating material to maintain the temperature .when direct or diffuse solar radiation will incident then it will not exit .
There are holes at upper and lower portion of the box for circulation of air .
First of all we keep the fooding material inside the box and close the roof glass
When solar radiation incident on black coating through transparent glass then heating aliment absorb the heat from solar radiation due to heat moisture of fooding material get vaporized and vapor droplets accumulates on the roof glass
As well as cold air enter from lower portion of the box and that air get heated
Due to hot air fooding material rapidly get dry and heated air exit throught upper hole
Vaporized water droplets also remove with hot air in the atmosphere and placed fooding material like vegetables get dry
Steps.
PROCESS FLOW DIAGRAM
· MATERIAL FLOW DIAGRAM
· DESIGN MODELLING
· 3D MODELLING
- BILL OF MATERIAL (BOM)
- PROCUREMENT
- FABRICATION
Process Flow Diagram
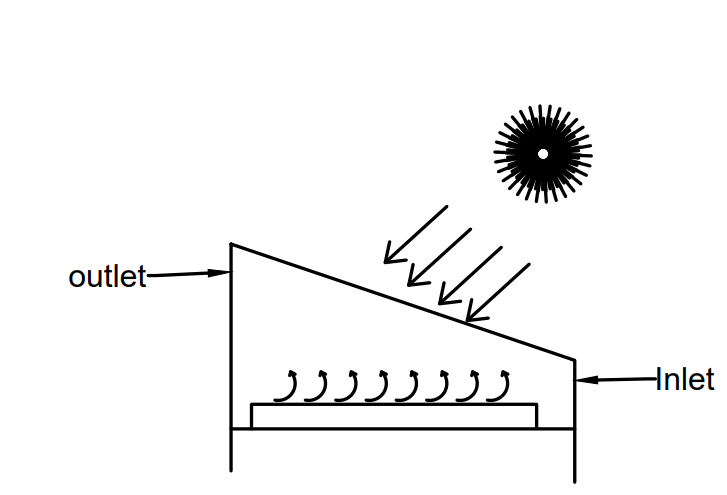
Solar dryer receives the energy from sun and it dry the crops vegetable fruit
Solar dryer consists with different main parts
Black material is coated on heating element inside the box to absorb more heat from solar radiation . outer frame of made up of heat insulating material to maintain the temperature .when direct or diffuse solar radiation will incident then it will not exit .
There are holes at upper and lower portion of the box for circulation of air .
First of all we keep the fooding material inside the box and close the roof glass
When solar radiation incident on black coating through transparent glass then heating aliment absorb the heat from solar radiation due to heat moisture of fooding material get vaporized and vapor droplets accumulates on the roof glass
As well as cold air enter from lower portion of the box and that air get heated
Due to hot air fooding material rapidly get dry and heated air exit throught upper hole
Vaporized water droplets also remove with hot air in the atmosphere and placed fooding material like vegetables get dry
Material Flow Diagram
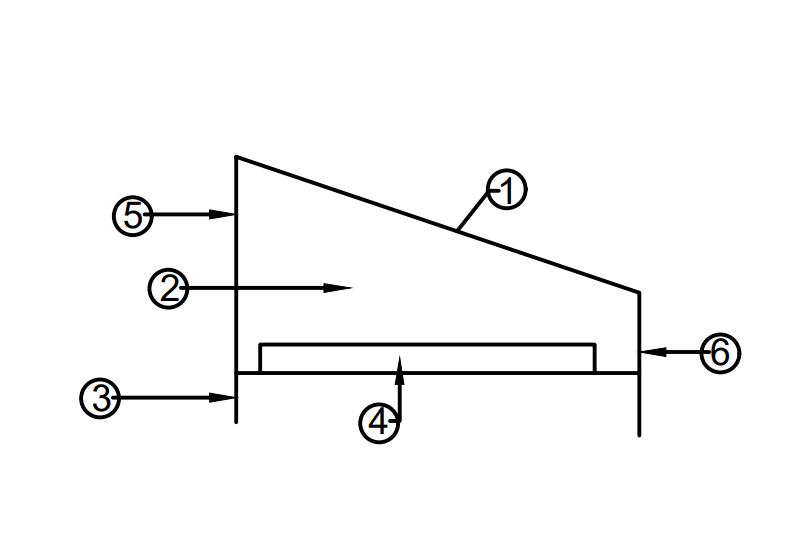
1 Polycarbonate sheet
2 Side Wall (Plywood)
3 Legs ( MS Angle)
4 Bottom ( Plywood)
5 Back Wall ( Plywood)
6 Front wall ( Plywood)
- Polycarbonate sheet
Polycarbonate sheet is a type of plastic that can withstand high temperature and high pressure. Polycarbonate sheet is used for solar dryers because it can withstand the heat from the sun and allow you to dry agricultural products without any electricity or gas.
The polycarbonate sheet for solar dryer is a thin, transparent, and durable material that has excellent light transmission properties.
It is often used in the construction of greenhouses and solar dryers. The polycarbonate sheet for solar dryer also offers protection from UV rays and provides insulation against heat loss.
This material is made from polycarbonates, which are thermoplastic polymers. Polycarbonates are used in many applications that require a durable material that is resistant to heat and UV light. Polycarbonate sheets can be used as a substrate for solar dryers.
2. Side Wall
Plywood is a material manufactured from thin layers or “plies” of wood veneer that are glued together with adjacent layers having their wood grain rotated up to 90 degrees to one another. It is an engineered wood from the family of manufactured boards which include medium-density fibreboard (MDF), oriented strand board (OSB) and particle board (chipboard).
All plywoods bind resin and wood fibre sheets (cellulose cells are long, strong and thin) to form a composite material. This alternation of the grain is called cross-graining and has several important benefits: it reduces the tendency of wood to split when nailed at the edges; it reduces expansion and shrinkage, providing improved dimensional stability; and it makes the strength of the panel consistent across all directions. There is usually an odd number of plies, so that the sheet is balanced—this reduces warping. Because plywood is bonded with grains running against one another and with an odd number of composite parts, it has high stiffness perpendicular to the grain direction of the surface ply.
Smaller, thinner, and lower quality plywood’s may only have their plies (layers) arranged at right angles to each other. Some better-quality plywood products will by design have five plies in steps of 45 degrees (0, 45, 90, 135, and 180 degrees), giving strength in multiple axes.
We using a plywood backside with Black color
3. MS angles
MS angle or mild steel angle is an L-shaped cross-section used in the construction of various structures and buildings. The most commonly used MS angle or metal angle is the one that forms a 90-degree angle with two sides of equal length and width
4 MS Nut & bolts
In physics, in the theory of general relativity, spacetimes with at least a 1-parameter group of isometries can be classified according to the fixed point-sets of the action. Isolated fixed points are called nuts. The other possibility is that the fixed point set is a metric 2-sphere, called bolt.
5 Black Paint
Black panels are expensive but are pure and more efficient. They can absorb light even in cloudy weather
Bill Of material
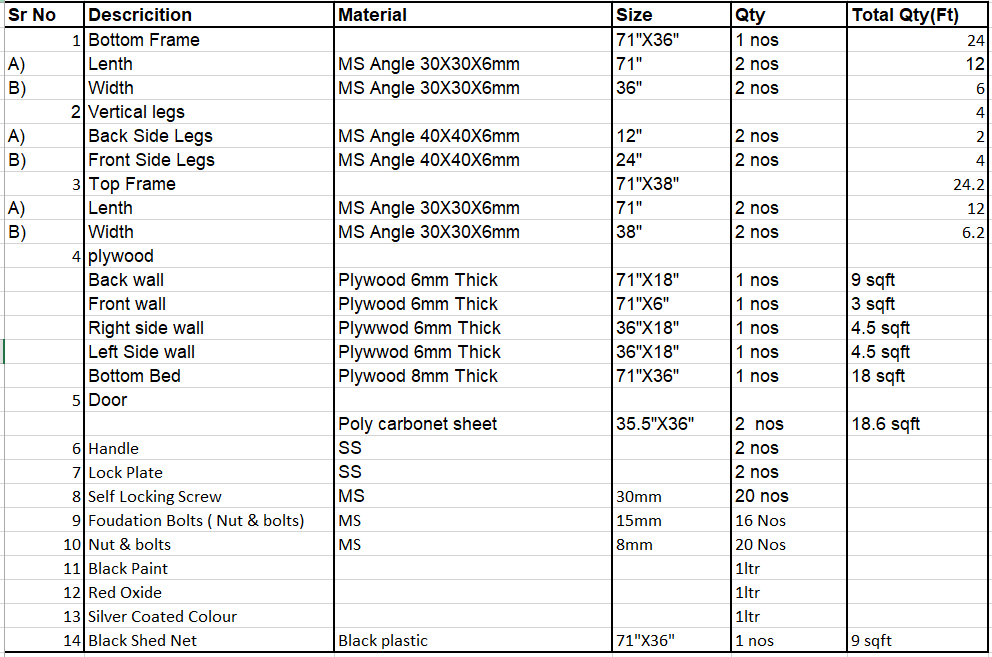
Rough Drawing ( Hand Sketch)
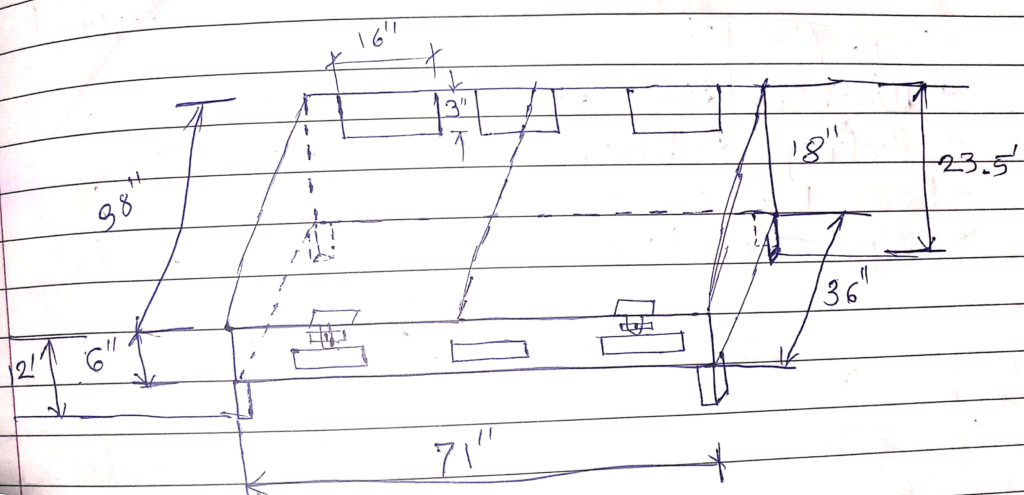
Design Modeling
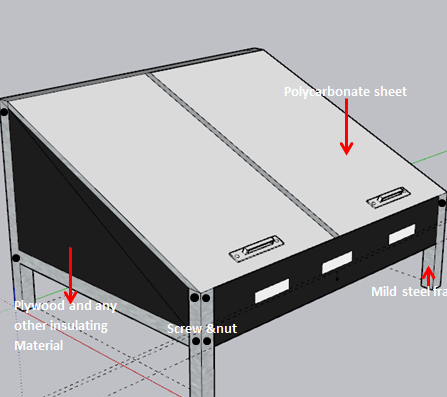
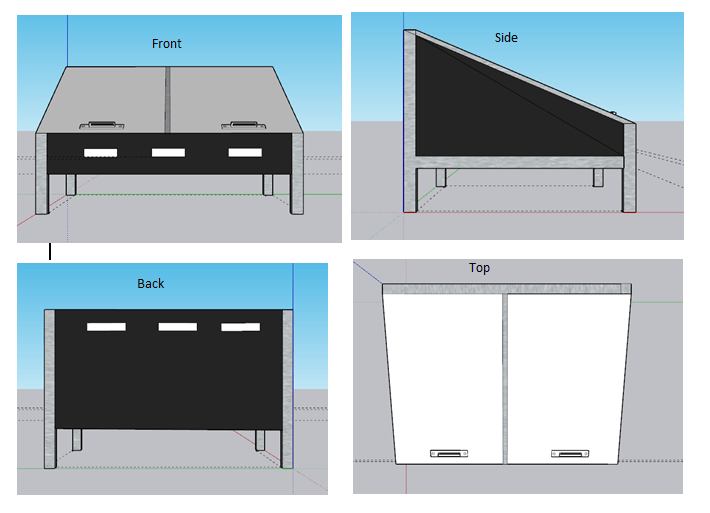
Fabrication
Step 1.
Material Purchasing
purchased All materials Like a bill of material.
- 30X30X3 MS angle,
- 40X40X5 MS Angle,
- 30X3 MS Flat Plate
- 8mm Plywood
- 12mm Plywood
- 6mm Polycarbonet sheet
- 15mm NUT & BOLTS
- lock plate
- handle
Step 2
Cutting & Drilling
An MS Angle Cut as per our measurement & then Drilled & finishing by grinding


Step 3
welding work
Frame of 30X30X3 MS angle was fabricated Total two Frames were fabricated one top and other bottom frame was welded
Top Frame Size 71″X38″
Bottom Frame 71″X36″
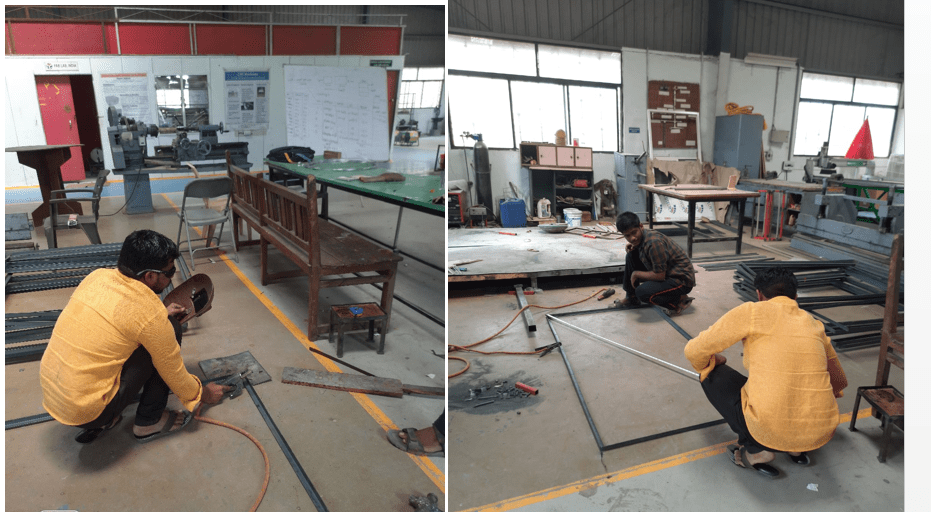
Step 4
Frame & vertical legs Join
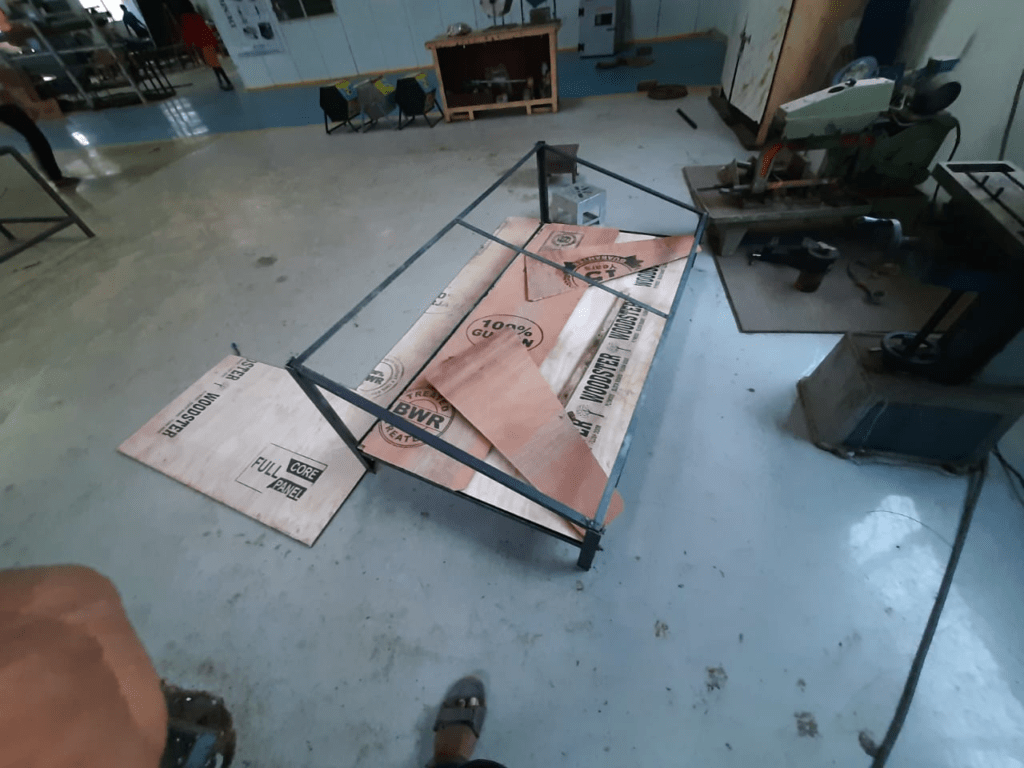
step 5
Plywood Cutting work
we cut all side of plywood
Back wall plywood 8mm thick 18″X71″
Front wall plywood 8mm thick 6″X71″
Side wall plywood 8mm thick 38″X6″X18″ 2 Nos
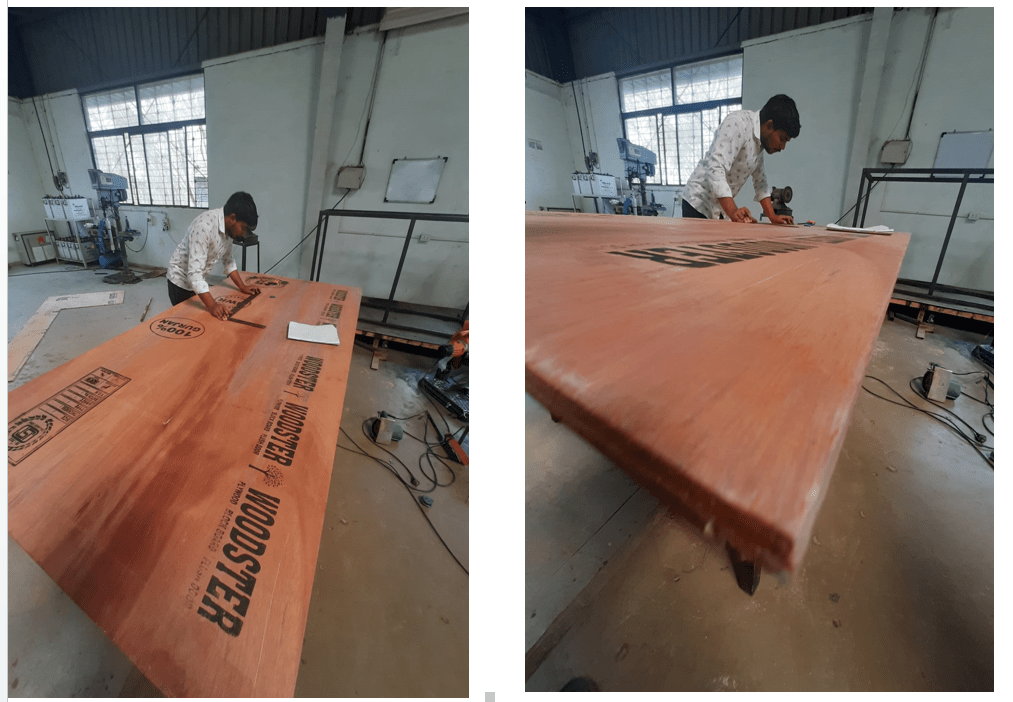
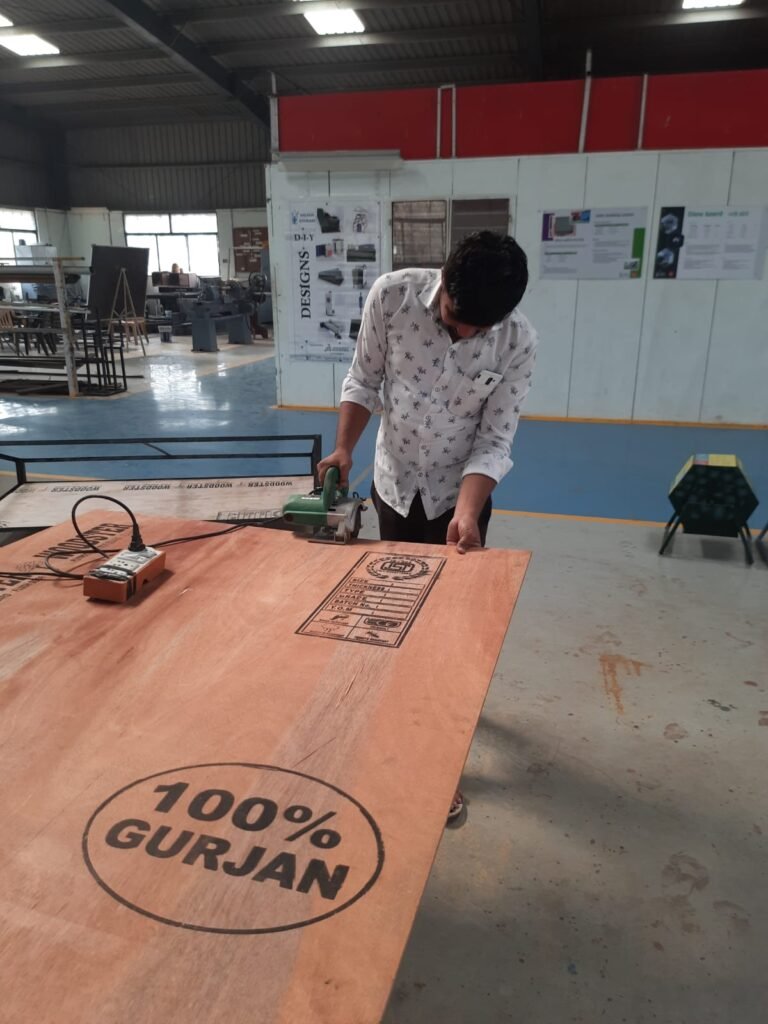
Step 6
Painting work
All Plywood & Structure Painting work
Plywood = Black japan
Structure = Red oxide + Silver coated color
Step 7
Bottom Plywood Cutting & Black Covering.
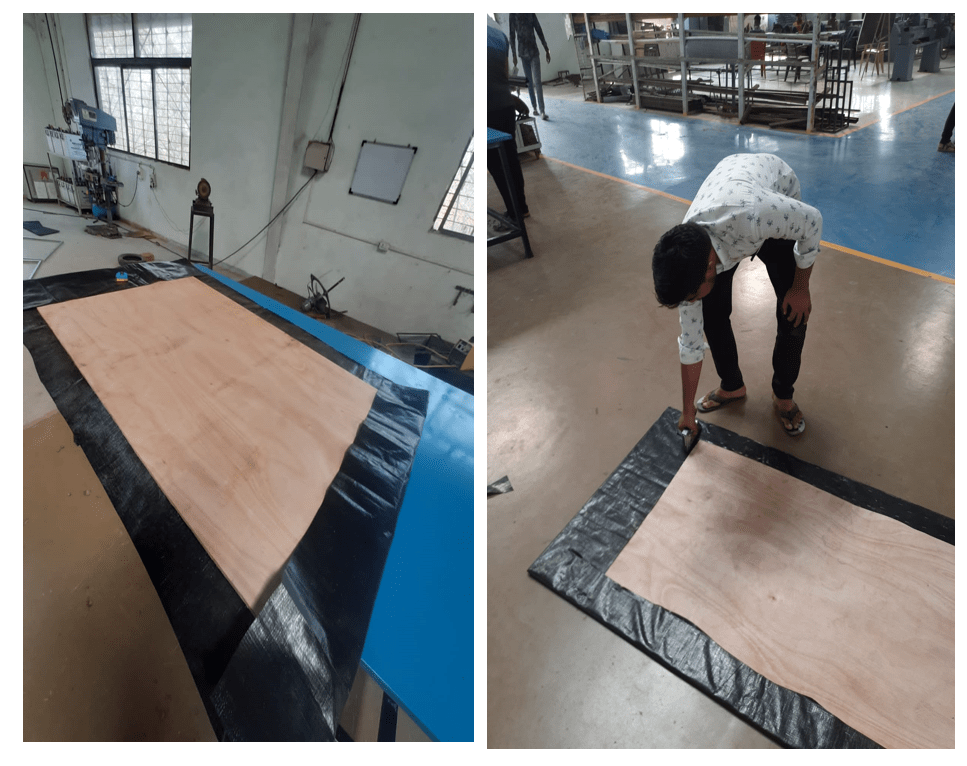
Step 8
Door Work
Polycarbonate Sheet two Sheet cutting work
36″X38″
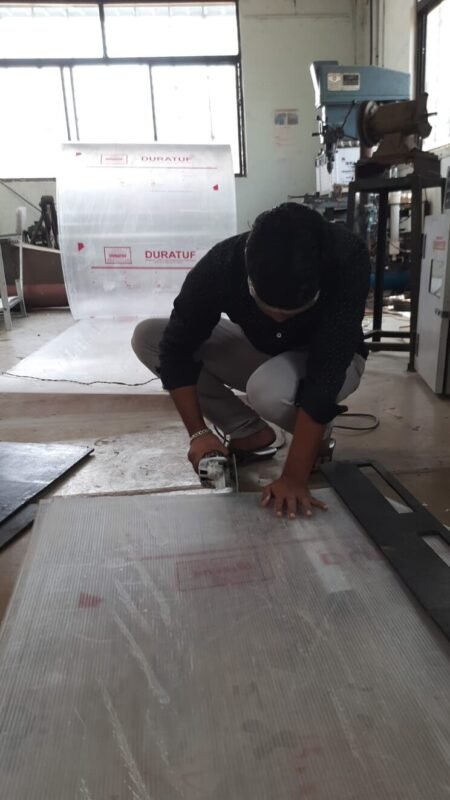
Door Fitting Work
Door fitting work with help of hinges
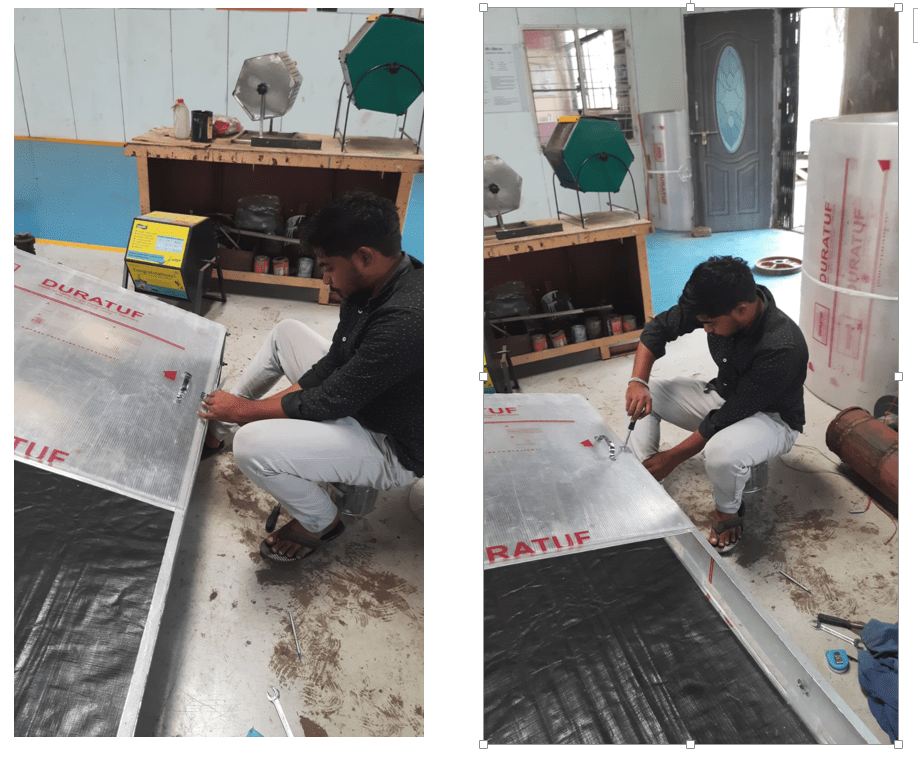
Step 11
Cleaning & Finishing Work
Dryer Clean work
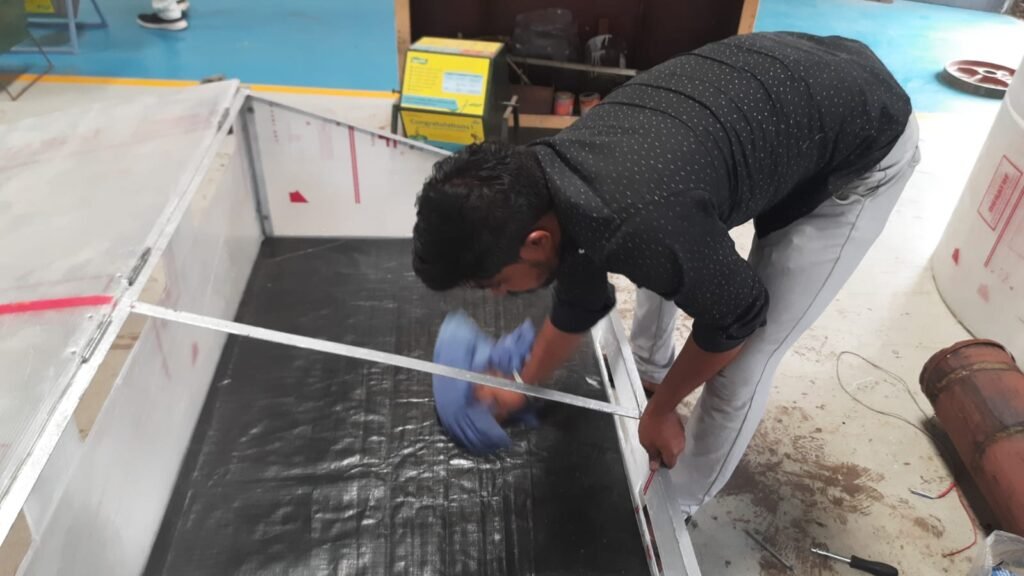